Maximizing Manufacturing Efficiency with Operations Dashboards
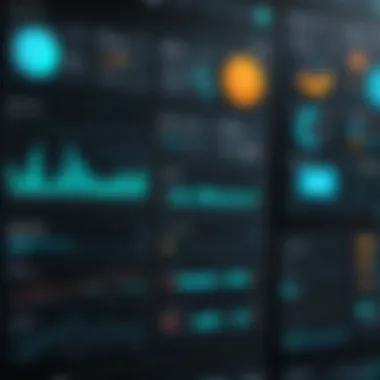
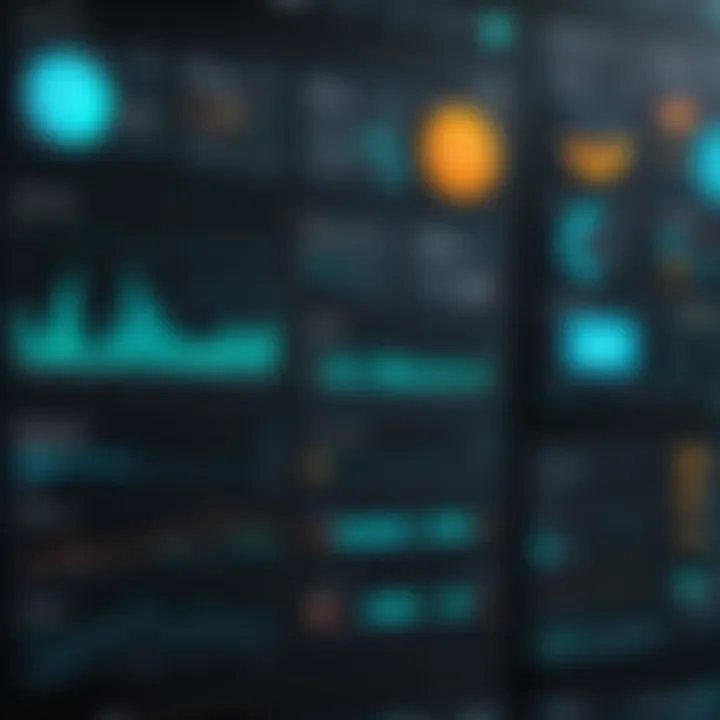
Intro
In an era where data drives every significant decision in the manufacturing sector, operations dashboards emerge as pivotal tools for enhancing efficiency. These dashboards present a holistic view of operational metrics, enabling industry stakeholders to monitor performance in real time and make data-driven choices. Understanding the finer points of operations dashboards is essential for professionals looking to optimize production workflows and address challenges swiftly.
As manufacturing businesses seek to improve productivity, it becomes vital to evaluate how dashboards can serve their unique needs. A clear understanding of software offerings and best practices not only facilitates informed decision-making but also promotes alignment within teams. This article will delve deeply into the diverse facets of manufacturing operations dashboards, spotlighting their significance, primary features, and implementation methods.
The following sections will provide insights into key functionalities and metrics, helping professionals appreciate how these dashboards can transform operations. Through exploration of these topics, the article aims to equip industry leaders with effective strategies to harness dashboard technology for enhanced manufacturing efficiency.
Software Overview
Manufacturing operations dashboards are categorized under business intelligence and analytics software. Their primary purpose is to consolidate data derived from various production processes into a single visual interface.
Key Features and Functionalities
The functionality of manufacturing dashboards is paramount. They typically include:
- Real-time Data Visualization: Easy-to-read graphs and charts that reflect current operational metrics, enabling quick responses to issues.
- Customizable Alerts: Automated notifications that inform users of important changes or anomalies in production metrics.
- Integrations: Capability to interface with existing software solutions, such as ERP and MES systems, ensuring a seamless flow of information.
- Performance Tracking: Monitoring of critical KPIs relevant to production efficiency, quality control, and resource utilization.
- Reporting Tools: Generation of comprehensive reports for analysis and decision-making, providing insights into trends over time.
By leveraging these features, manufacturing companies can effectively track their operational performance and make necessary adjustments. Understanding these components is the first step toward realizing the potential of operations dashboards in today's data-centric manufacturing landscape.
Understanding Manufacturing Operations Dashboards
Manufacturing operations dashboards serve as critical tools for organizations seeking to streamline their processes and make data-driven decisions. These dashboards integrate various data sources, allowing stakeholders to visualize essential metrics and trends. Understanding the role they play is crucial for professionals aiming to enhance operational efficiency, swiftly respond to challenges, and uphold high standards of production.
Definition and Purpose
Operations dashboards are visual representations of key performance indicators and metrics. They consolidate real-time data into a comprehensible format, facilitating quicker interpretation. The primary purpose of these dashboards is to provide decision-makers with immediate access to relevant data, thus enabling informed choices that align with organizational goals. This capability can dramatically mitigate the risk of misinterpretation or oversight of critical data.
Key components usually include:
- Real-time updates: Allowing for timely reactions to fluctuations in production.
- Customization options: Adapting the display of data to fit specific needs and roles within the organization.
- User-friendly interface: Simplifying navigation and comprehension for users with varying levels of technical expertise.
In summary, the definition and purpose of manufacturing operations dashboards lie in their ability to simplify complexity and enhance visibility across the production process. They transform raw data into actionable insights, which is essential in today's data-centric industrial landscape.
Historical Development
The evolution of manufacturing operations dashboards can be traced back several decades, though their significant rise began with the advent of digital technology. Initially, information was presented through traditional reporting methods, such as printed documents or static spreadsheets. These formats, while functional, limited interactivity and real-time updates.
With the emergence of software solutions in the late 20th century, organizations started adopting computerized systems for data management and reporting. Gradually, firms recognized the need for efficient data presentation, leading to the development of early dashboard technology in the early 2000s.
As technology advanced, so did the intricacies of these dashboards. Today, they encompass sophisticated data visualization tools that enhance user experience. Functions like predictive analytics and machine learning integration have become standard, fostering a more proactive approach to operational management.
Key Components of an Operations Dashboard
The effectiveness of an operations dashboard is contingent upon its key components. These elements are integral to delivering the necessary insights that drive manufacturing efficiency. Each component plays a role in how data is visualized, what metrics are prioritized, and the overall user experience. Focused attention on these aspects can lead to better decision-making and improved operational outcomes.
Data Visualization Techniques
Data visualization techniques are essential for making complex data comprehensible at a glance. The primary aim is to translate raw data into visual contexts. Common practices include the use of graphs, charts, and gauges.
- Graphs and Charts: Line graphs and bar charts help in identifying trends over time. They allow users to make quick comparisons and draw conclusions without diving deep into the numbers.
- Gauges and Heat Maps: Gauges represent performance against pre-set targets. Heat maps are effective at highlighting areas that require attention, allowing for swift reactions to problems.
- Interactive Visuals: Interactive dashboards encourage user engagement. They allow users to manipulate data and view different correlations or drill down into specifics as needed.
Employing a variety of visualization techniques is crucial for catering to diverse user preferences and enhancing understanding of the data presented.
Core Metrics to Track
The choice of metrics is central to the dashboard's relevance and effectiveness. Key performance indicators (KPIs) should be aligned with the organization’s operational goals.
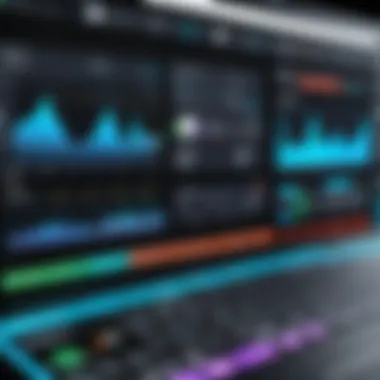
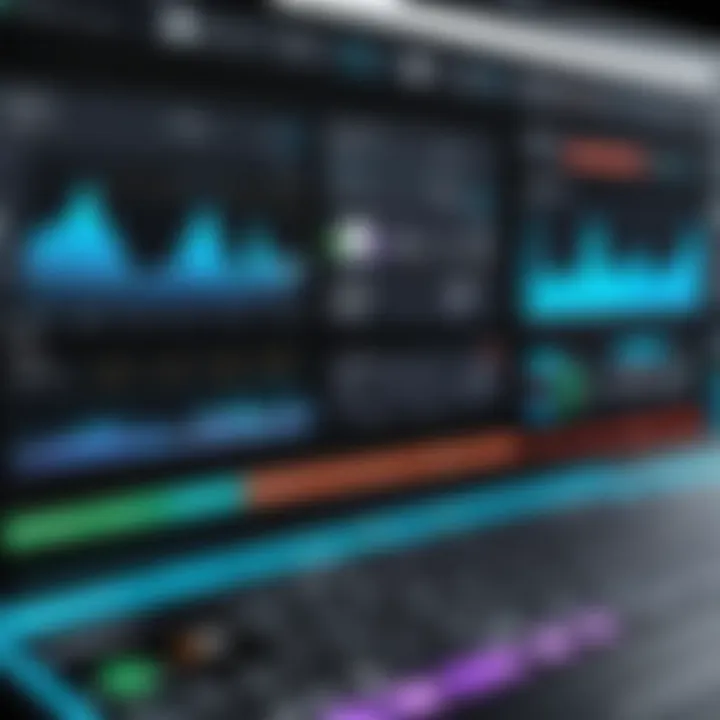
Some core metrics to consider include:
- Production Volume: Tracks the number of units produced within a certain timeframe.
- Cycle Time: Measures the total time taken to complete one cycle of production, revealing areas for efficiency gains.
- Downtime: Assesses periods when production is halted, which is crucial for identifying bottlenecks.
- Quality Metrics: Evaluates defect rates and customer complaints, essential for maintaining standards.
- Utilization Rates: This metric indicates how much of your production capacity is being used effectively.
The selection of metrics should offer a clear and actionable view of manufacturing performance. Proper emphasis on relevant metrics helps stakeholders pinpoint weaknesses, allowing for focused improvement efforts.
User Interface Considerations
A well-designed user interface can make or break the effectiveness of an operations dashboard. It should facilitate easy navigation and aid in rapid comprehension of data.
Key considerations include:
- Clarity and Simplicity: The interface should avoid clutter. Information must be displayed clearly, ensuring that users can focus on the most important data without distractions.
- Customization Options: Allowing users to customize dashboards to fit their needs enhances usability. Each user may have different priorities or roles requiring distinct data.
- Responsive Design: As organizations often use mobile devices, a responsive design ensures that dashboards are accessible across platforms.
- User Feedback Integration: Continually collecting and integrating user feedback can enhance the dashboard’s usability over time.
Ensuring these aspects are front of mind during development promotes a productive and intuitive user experience, making it easier for users to engage with the dashboard effectively.
Effective dashboard design is more than just aesthetics; it's about functionality and usability that drives better operational outcomes.
A dashboard that incorporates these major components will best serve its purpose in enhancing manufacturing efficiency.
Importance of Manufacturing Dashboards
Manufacturing dashboards serve as a critical tool in modern operational environments. They integrate various data points to provide insights that drive performance improvement. Understanding the importance of these dashboards can significantly impact decision-making processes and operational strategies.
Enhanced Decision-Making
Effective decision-making is essential for any organization aiming for success. Operations dashboards enhance this by providing vital information at a glance. When decision-makers have access to real-time data, they can identify trends and anomalies quickly. This means they can react to issues like production delays or equipment failures before they escalate. By visualizing complex data, manufacturing dashboards empower managers to make informed decisions, rather than relying on instinct or outdated information. This clarity reduces the risk of errors and omissions, ultimately leading to better business outcomes.
Operational Efficiency
Operational efficiency is another key focus for businesses looking to optimize processes. Dashboards allow organizations to monitor various metrics related to production, quality control, and resource allocation. With this information, managers can pinpoint inefficiencies and areas for improvement. For instance, if a specific machine displays frequent downtimes, it can lead to targeted maintenance efforts, thereby increasing overall productivity. Moreover, by integrating multiple data sources, dashboards can reveal unexpected connections between different parts of the manufacturing process. These insights can lead to streamlined workflows, reduced cycle times, and ultimately, higher profit margins.
Real-Time Monitoring
In a fast-paced manufacturing environment, real-time monitoring is indispensable. Operations dashboards provide up-to-the-minute data that keep production on track. This capability is particularly useful for managing supply chains and inventory levels. By tracking these metrics in real time, businesses can optimize stock levels and improve forecasting accuracy. Furthermore, dashboards can alert managers to potential issues as they arise. This proactive approach minimizes disruptions and keeps operations moving smoothly. Companies can maintain a consistent quality of output, meeting customer expectations without unnecessary delays.
"Access to real-time data is like having a compass in a stormy sea. It keeps you oriented amidst chaos."
In summary, the importance of manufacturing dashboards lies in their ability to enhance decision-making, improve operational efficiency, and facilitate real-time monitoring. For organizations that embrace this technology, the benefits are clear: increased agility, improved resource management, and a stronger competitive edge.
Challenges in Implementing Operations Dashboards
Implementing manufacturing operations dashboards is not without its challenges. These obstacles can significantly impact a company’s ability to leverage data for enhancing efficiency. It is essential to understand these challenges to create a robust strategy that facilitates successful implementation.
Data Integration Issues
Data integration is often regarded as one of the most critical challenges. In a manufacturing environment, data can originate from various sources, including machines, production systems, and supply chain management tools. The complexity increases when these systems do not communicate seamlessly. Disparate systems can cause delays in data availability, which in turn affects decision-making processes.
To effectively implement an operations dashboard, companies must address data silos. Here are notable considerations:
- Standardization: Establishing a common data format across all systems is necessary for effective integration.
- Real-time Data Streaming: Utilizing technologies that allow real-time data streaming can improve response times and accuracy.
- Data Cleansing Practices: Before integrating, data must be cleansed to remove inaccuracies that could lead to errant analyses.
User Resistance
User resistance is another significant barrier that organizations face. Employees may be accustomed to traditional methods of operation and may be skeptical or hesitant about adopting new technologies.
Understanding the root of this resistance is fundamental. Typically, it stems from a few factors:
- Fear of Change: People often fear what they do not understand. Changes in routine can lead to anxiety about job security or performance evaluations.
- Insufficient Training: If employees are not properly trained on the new dashboard system, they may feel unprepared to use it effectively.
- Lack of Stakeholder Involvement: Engaging users in the development process encourages buy-in. When users feel their input is valued, they are more likely to embrace the change.
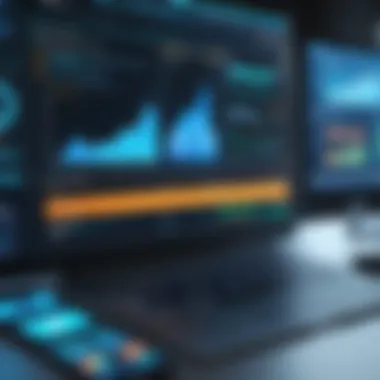
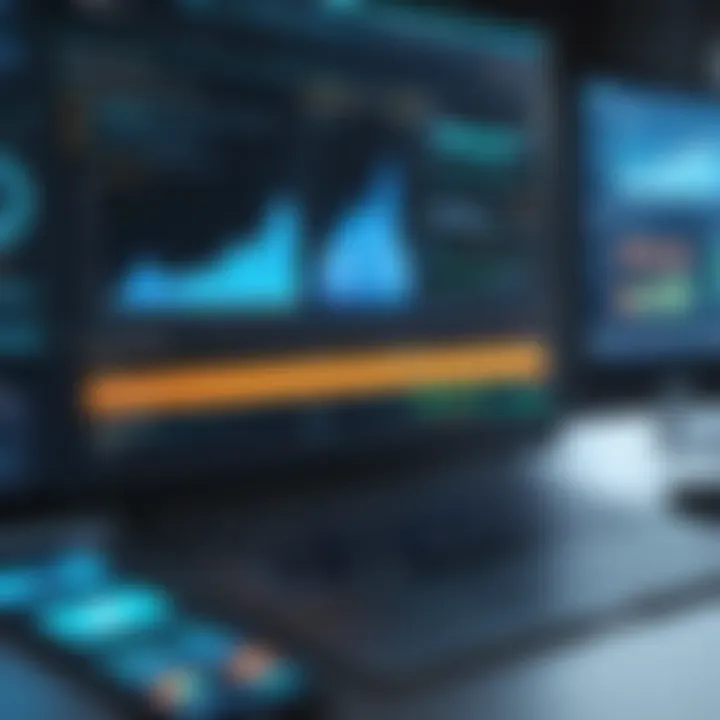
Maintenance and Updates
The work does not stop after implementation. Constant maintenance and updates are vital for the sustainability of operations dashboards. As technology rapidly evolves, dashboards must be updated to reflect new capabilities and security protocols. Common maintenance challenges include:
- Resource Allocation: Ensuring that the right resources, both time and personnel, are dedicated to maintenance can be difficult.
- User Feedback Loop: Establishing iterative feedback processes helps in identifying areas that require improvement but may often be neglected.
- Adapting to New Data Sources: As businesses grow and evolve, they may need to integrate new data sources, requiring adjustments to the dashboard.
Implementing an operations dashboard is a multifaceted endeavor. Recognizing and planning for these challenges can guide companies to reap the benefits of improved efficiency and data-driven decision-making.
Best Practices for Utilizing Manufacturing Dashboards
Manufacturing dashboards are crucial tools that can leverage data visualization to enhance operational efficiency. However, using these dashboards effectively requires a deep understanding of best practices. Applying these best practices ensures that dashboards are not just functional but truly transformative for manufacturing processes.
Customization for User Needs
Customization is essential for maximizing the utility of manufacturing dashboards. Each user in an organization has specific needs and perspectives that must be catered to. Tailoring dashboards allows users to focus on relevant metrics and KPIs that pertain to their role within the company.
For example, a production manager may prioritize efficiency metrics, while quality control personnel might focus on defect rates. By providing personalized dashboard views, organizations can increase user engagement and enhance decision-making processes. In addition, customization fosters a sense of ownership among users, leading to greater satisfaction and utilization. While implementing customization, it is vital to gather input from users during the design phase to ensure the dashboard meets their expectations.
Regular Training and Support
Manufacturing dashboards can be complex tools. Providing regular training and ongoing support is necessary for ensuring users are comfortable and proficient with these systems. Organizations should establish a comprehensive training program that covers both the technical aspects of using the dashboard and the strategic importance of the data being analyzed.
Training should not be a one-time event. Continuous education will keep users updated on new features, functionalities, and best practices. Facilitating small workshops and creating user guides or online tutorials can significantly boost user expertise. Moreover, having dedicated support teams to assist with questions or issues can create a safety net that encourages users to rely on the dashboard more confidently.
Iterative Feedback Loops
Establishing feedback loops is an effective strategy for improving manufacturing dashboards. It involves setting up consistent channels for users to share their experiences and suggestions regarding dashboard performance. This ongoing dialogue can reveal areas for improvement that may not be immediately obvious to developers.
For example, after the initial rollout of a dashboard, collecting feedback can help identify which features are underutilized or confusing to users. From this feedback, organizations can prioritize necessary adjustments and enhancements. Creating iterative feedback mechanisms also cultivates a culture of collaboration and innovation. Users feel valued when their input leads to tangible changes.
The integration of user feedback can lead to more effective dashboards that adapt over time, aligning with evolving user requirements and ensuring sustained relevance.
In summary, applying these best practices—customization for user needs, regular training and support, and iterative feedback loops—can significantly enhance the effectiveness of manufacturing dashboards. By focusing on these areas, organizations can unlock the full potential of their data and drive continuous improvement in manufacturing processes.
Technological Frameworks Supporting Dashboards
In the context of manufacturing operations, technological frameworks are foundational. They provide the necessary infrastructure and tools to create, manage, and utilize operations dashboards effectively. These frameworks support data integration, visualization, and analysis, which are crucial for enhancing manufacturing efficiency. As the industry evolves, so too do the requirements for the systems in place. The advent of real-time data processing, cloud computing, and machine learning has further emphasized the importance of robust technological frameworks.
The benefits of well-implemented technological frameworks include improved data accuracy, easier access, and a more cohesive user experience. Beyond these, they help organizations adapt quickly to changing market conditions. The flexibility of various frameworks allows businesses to select solutions that best meet their specific operational needs. In short, technological frameworks do not merely support dashboards; they are the backbone of data-driven manufacturing strategies.
Software Solutions and Tools
Software solutions are critical components of any operational dashboard. These tools enhance the functionalities of dashboards by enabling better data management, visualization, and analysis. Commonly used solutions include Tableau, Power BI, and QlikView. Each of these tools offers specific capabilities, such as real-time data visualization and customizable reporting features, which empower manufacturers to make informed decisions more quickly.
Moreover, many of these solutions come equipped with user-friendly interfaces that promote accessibility. Technicians and managers, regardless of their technical backgrounds, can navigate the systems with relative ease. This ease of use is essential for maximizing the potential of operations dashboards. As users become more comfortable with the tools, they can leverage dashboards for not only monitoring but also for discovering insights that may improve overall operation.
Cloud vs. On-Premises Solutions
The choice between cloud and on-premises solutions is a vital consideration for organizations developing their operations dashboards. Cloud solutions offer several advantages, including scalability, cost-effectiveness, and easy access from various devices. This flexibility allows manufacturers to manage significant datasets without heavy upfront investments. However, concerns around data security and compliance remain critical, as sensitive information may be vulnerable when stored off-site.
On-premises solutions, in contrast, provide higher control over data and security. They allow organizations to tailor the infrastructure to precisely fit their operational requirements. However, this often comes with increased maintenance costs and the necessity of a full IT support team.
Ultimately, the decision between cloud and on-premises solutions should be guided by the specific needs of the business, considering both immediate requirements and long-term goals.
"Technological frameworks are not just tools; they are essential for leveraging data to drive manufacturing excellence and innovation."
Case Studies in Manufacturing Dashboard Implementation
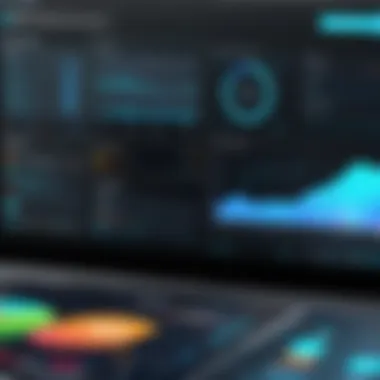
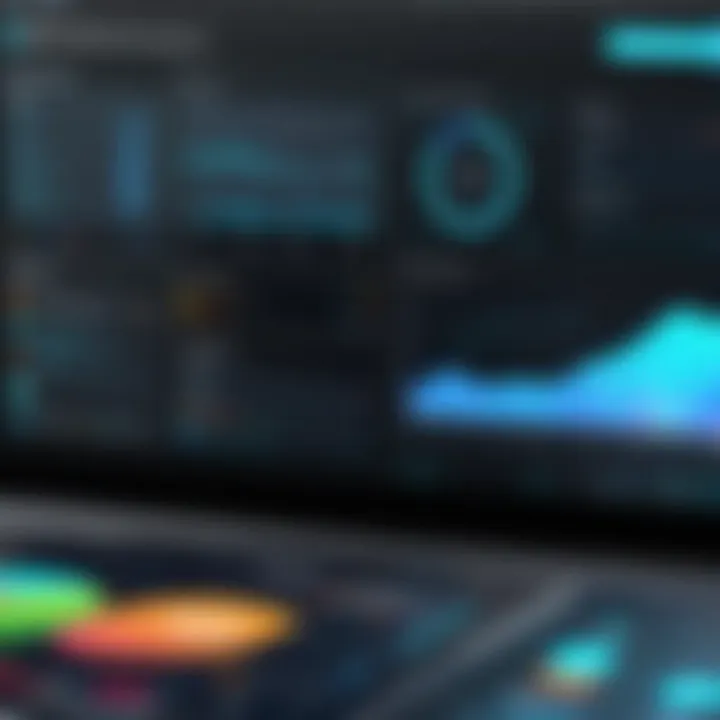
The implementation of manufacturing operations dashboards in real-world scenarios provides invaluable insights into their effectiveness and benefits. These case studies illustrate not only the success stories but also the challenges faced during integration. By examining actual applications, businesses can glean practical strategies for deploying dashboards in their operations. The primary advantage of reviewing these case studies is to understand the tangible results that can be achieved, encouraging business stakeholders to make informed decisions regarding their adoption.
Company Profiles
Company profiles offer a glimpse into how various organizations have integrated operations dashboards into their manufacturing processes. Each profile highlights unique approaches and solutions tailored to specific operational needs.
For instance, a well-known automotive manufacturer recently adopted a comprehensive dashboard to monitor production efficiency. This dashboard tracks key performance indicators (KPIs) such as defect rates, production cycle times, and labor productivity. As a result, the company reported a 15% increase in output over six months.
Another example can be found in a consumer goods company. They implemented a dashboard focusing on supply chain visibility. By visualizing data from suppliers to retailers, they reduced lead times by 20%. This not only improved inventory management but also enhanced customer satisfaction.
Outcomes and Learnings
The outcomes of these case studies underscore the transformative impact of operations dashboards on manufacturing efficiency. These implementations frequently reveal significant improvements across multiple operational metrics.
- Informed Decision Making: Companies utilizing dashboards experienced a measurable enhancement in decision-making capabilities. With real-time data, management teams can respond to issues swiftly.
- Increased Transparency: Dashboards provide visibility into the entire production process. This transparency helps in identifying bottlenecks and inefficiencies, leading to targeted interventions.
- Cultural Shift: Organizations have noted a shift towards data-driven cultures. Employees at all levels become more engaged when they can visualize their contributions through dashboards.
"The integration of operations dashboards leads to a more streamlined workflow and empowered employees—two key aspects that drive manufacturing success."
Future Trends in Manufacturing Operations Dashboards
The landscape of manufacturing operations is rapidly evolving. As technology continues to progress, various trends are emerging that aim to enhance the functionality and utility of operations dashboards. Understanding these trends is crucial for industry stakeholders looking to optimize their data utilization. The integration of modern technologies into manufacturing dashboards is not just a matter of keeping up; it is a necessity for increased efficiency, better decision-making, and a competitive edge.
AI and Machine Learning Integration
The integration of artificial intelligence (AI) and machine learning (ML) into manufacturing operations dashboards is possibly one of the most significant advances in recent years. AI and ML can analyze vast data sets in real-time, identifying patterns and anomalies that might be invisible to human analysts. The result is a more agile manufacturing process that can adapt to changes swiftly.
For instance, AI algorithms can recommend adjustments in production schedules based on equipment performance data. This predictive capability helps mitigate downtime and increases overall productivity. Moreover, machine learning models can improve over time, adapting their monitoring and responses based on new data, thus becoming more effective in handling complex operational tasks.
Some key benefits include:
- Real-time insights: Immediate data processing allows for prompt decision-making.
- Predictive maintenance: Identifying potential equipment failures before they occur reduces operational disruptions.
- Enhanced quality control: Continual learning from production data ensures sustained product quality.
"Employing AI tools not only saves time but also allows for deeper insights, paving the way for smarter operations."
The considerations for successful integration involve robust data governance and the need for skilled personnel who can interpret AI results. Companies must strategically invest in training and resources to harness the full potential of these technologies.
Predictive Analytics Capabilities
Predictive analytics is another critical trend that influences the efficacy of manufacturing operations dashboards. This technology leverages historical data to forecast future events and trends, allowing decision-makers to plan accordingly. Manufacturing processes benefit enormously from predictive capabilities, as they facilitate
- Demand forecasting: Adjusting production rates based on predicted market needs helps in inventory management.
- Quality assessment: Recognizing when defects are likely to occur aids in maintaining product standards.
- Resource allocation: Streamlining the use of materials and labor based on anticipated production levels promotes efficiency.
Incorporating predictive analytics in dashboards makes it possible to create simulations based on various scenarios. This empowers companies to navigate uncertainties with a clear action plan.
Adopting these capabilities is not without challenges. Integration into existing frameworks can be complex and requires careful consideration of data inputs. Organizations must balance between data volume and relevance to not overwhelm users with excessive information that could lead to confusion.
Overall, the shifts towards AI, machine learning, and predictive analytics signify a pivotal transformation in how manufacturing operations dashboards are utilized. These trends enhance strategic planning capabilities, operational monitoring, and available analytical insights, ultimately leading to improved manufacturing efficiency.
Culmination
The conclusion section provides a final synthesis of the key insights presented throughout the article. Manufacturing operations dashboards serve as crucial tools in enhancing efficiency, promoting informed decision-making, and ensuring that manufacturing processes run smoothly. The importance of this topic cannot be understated. With the rapid evolution in manufacturing technology and data analytics, understanding the role of dashboards is essential for any organization aiming to stay competitive in the industry.
Summary of Key Insights
- Operational Optimization: A well-designed operations dashboard aggregates real-time data that allows leaders to quickly identify inefficiencies and establish metrics to enhance productivity. The integration of various data sources means that companies can view relevant information in one place, driving better decisions.
- Empowering Stakeholders: By utilizing dashboards, stakeholders from diverse functions, including operations, finance, and supply chain, can gain insights tailored to their specific needs. This capability fosters a culture of transparency and data-driven decision-making across the organization.
- Navigating Challenges: Implementing these dashboards involves addressing challenges such as integration of old systems, managing user resistance, and ongoing maintenance. Recognizing these potential pitfalls can lead to more effective strategies during the adoption phase.
"The design and implementation of manufacturing operations dashboards is not merely a task but a strategic initiative that instructs the health of a business."
Final Thoughts on Adoption
Adopting operational dashboards is a multi-faceted endeavor that requires careful consideration and planning. Organizations must ensure that the chosen technology aligns with their specific operational needs and capabilities. Moreover, providing comprehensive training is imperative to facilitate user engagement and acceptance of the new tools.
The benefits of implementing manufacturing dashboards are profound. These tools contribute not only to enhanced visibility over production processes but also to improved compliance with industry regulations and standards. As industries continue to embrace the Fourth Industrial Revolution, organizations that effectively integrate advanced data analytics through operations dashboards will likely thrive.
Ultimately, as the landscape demands more agile and data-informed decisions, the adoption of manufacturing operations dashboards will be a defining factor in achieving lasting operational efficiency.