Key Features of Auto Repair Work Order Software
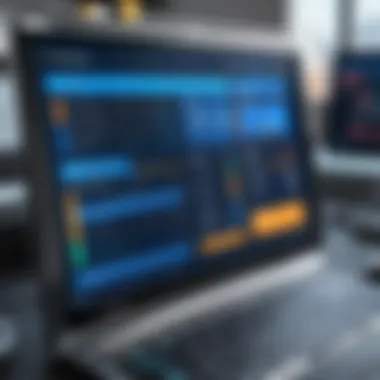
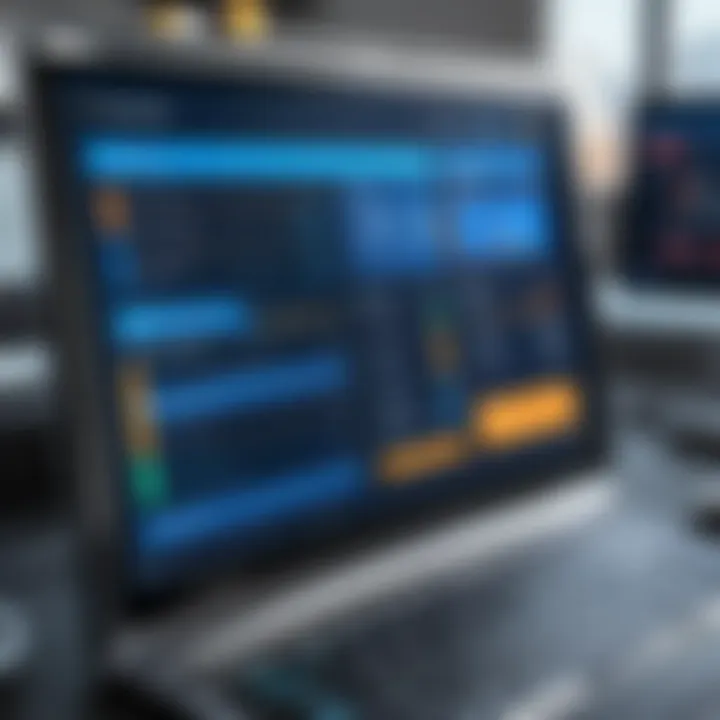
Intro
In today’s fast-paced automotive industry, the efficiency of repair operations can make or break a business. Auto repair work order software has emerged as a vital tool for workshops, enabling them to streamline their processes and enhance customer satisfaction. This software allows for a seamless flow of information between various aspects of the repair process, from initial customer contact to invoice generation. As businesses seek to improve operational effectiveness, understanding these solutions becomes crucial.
With numerous options on the market, navigating through the myriad features and functionalities can be overwhelming. This article offers a comprehensive exploration of auto repair work order software, aiming to equip IT professionals, business owners, and decision-makers with the knowledge necessary to choose a solution tailored to their unique needs.
Software Overview
Software Category and Its Purpose
Auto repair work order software falls into the broader category of automotive management solutions. Its primary role is to automate and enhance the various tasks associated with vehicle repair and maintenance. By integrating elements like scheduling, tracking, invoicing, and customer communication, such software seeks to create a cohesive environment that fosters productivity and efficiency.
Key Features and Functionalities
When assessing different software solutions, several critical features should piqué the interest of potential users:
- Job Management: Simplifies tracking tasks and job progress, enabling staff to prioritize effectively.
- Estimate Creation: Provides quick and accurate quotations for repairs, improving customer service and trust.
- Inventory Control: Facilitates the management of parts and supplies, ensuring that the necessary items are always available.
- Reporting Tools: Delivers insights into key performance indicators, helping businesses make data-driven decisions.
- Customer Relationship Management (CRM): Enhances interaction with customers through reminders, follow-ups, and maintaining detailed service histories.
These features contribute to a more organized shop environment, allowing technicians to focus on repairs rather than administrative tasks.
"Using work order software can reduce the chaos of a busy shop and give time back to owners and employees."
Comparative Analysis
Comparison with Similar Software Products
In a market that boasts a variety of solutions, softwares like Mitchell 1 and Shop-Ware often come to the forefront. These platforms offer overlapping capabilities but differ in user interface and pricing structures, catering to distinct market segments. For example, Mitchell 1 focuses heavily on information accessibility and repair procedures, while Shop-Ware emphasizes user experience with its visually appealing dashboard.
Market Positioning and User Demographics
Understanding the target audience is crucial when analyzing auto repair work order software. Typically, the user base consists of workshop owners, managers, and technicians. Their varying levels of technical aptitude necessitate user-friendly interfaces and tailored training solutions. While larger shops may prioritize comprehensive features that cover complex operations, smaller businesses might seek more straightforward options that meet basic needs without a hefty price tag.
Understanding Auto Repair Work Order Software
Understanding auto repair work order software is like peeking under the hood of a finely tuned engine. It’s crucial for anyone navigating the complex landscape of the auto repair industry. This software acts as the nerve center of a workshop, ensuring that everything runs smoothly, from customer check-ins to tracking inventory and managing staff workloads. Without it, you'd be left to the whims of paperwork and guesswork, which nobody wants.
Definition and Purpose
At its core, auto repair work order software is a digital solution that assists auto repair shops in managing their operations more effectively. Think of it as a highly organized ledger but with a modern twist. The primary purpose of this software is to streamline processes, eliminate inefficiencies, and enhance communication among stakeholders in the repair shop environment.
By automating tasks such as appointment scheduling and inventory management, this software frees up vital time that can be better spent on enhancing customer service. It spells out the scope of work for each vehicle, tracks labor hours, and offers transparency in pricing. In essence, it’s designed not just to make the day-to-day easier but to drastically improve customer experience by enabling clearer communication about repairs, costs, and timelines.
Key Components of Work Order Systems
Understanding the key components of work order systems is essential. While the specifics may vary from one software solution to another, some core elements tend to be universally acknowledged:
- Job Management: This functionality coordinates tasks, ensuring that mechanics understand their assignments clearly and that workflows are optimized.
- Customer Database: A well-maintained database helps to keep customer records, previous repairs, and needs handy, fostering improved customer relationships through personalized service.
- Inventory Tracking: Effective inventory management ensures that parts are readily available when needed, cutting down on delays due to waiting for parts to arrive.
- Invoicing and Billing: The software can automatically generate invoices once the work is complete, which promotes swift payment and minimizes errors.
- Reporting and Analytics: Many systems offer in-depth reporting features that allow shop owners to analyze performance metrics over time. This insight can be invaluable for improving service quality and profitability.
Common Users in the Auto Repair Industry
Several types of users benefit from auto repair work order software, each with their unique responsibilities and needs. The principal user groups typically include:
- Auto Repair Technicians: They rely on the software for clarity in assigned tasks and updates on job statuses.
- Service Managers: Their role includes overseeing shop operations, and they often utilize the software to manage schedules and assess productivity.
- Owners/Operators: Business owners use the insights generated by the software to make informed decisions on pricing, staffing, and overall operations.
- Customer Service Representatives: They depend on smooth interactions with the software to schedule appointments and follow up with customers effectively.
"Choosing the right work order software can drastically change how a repair shop operates, making processes smoother and communication clearer."
By grasping these elements and understanding who the pivotal users are within the auto repair ecosystem, stakeholders can better appreciate the immense value that work order software brings to the table. It’s not just a luxury; it’s nearly a necessity in today's fast-paced automotive landscape.
Benefits of Using Work Order Software
When it comes to running an auto repair shop, the sheer volume of tasks and customer interactions can be overwhelming. Work order software plays a significant role in streamlining the daily operations. The benefits go beyond merely having a tool to manage repairs. It's about enhancing efficiency, improving customer interactions, and making data management a breeze.
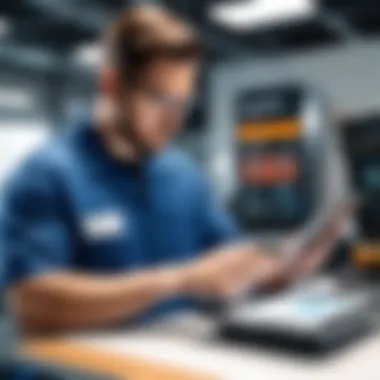
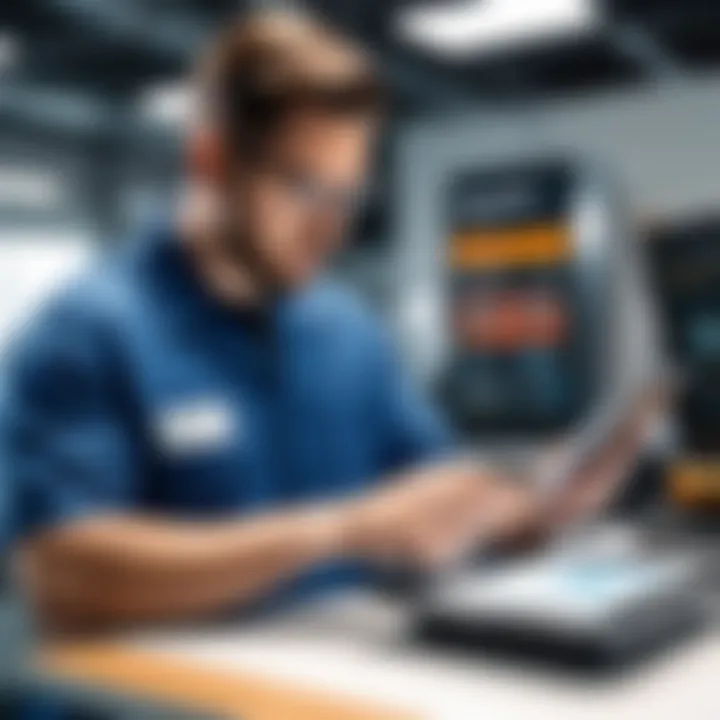
Increased Efficiency
Efficiency is the name of the game in any business, and auto repair shops are no exception. Implementing work order software can significantly reduce the time taken to process jobs, manage parts inventory, and keep track of customer interactions. Think about it: when every detail of the repair process is at your fingertips, there's less room for error.
With automation, the mundane tasks can take a backseat, allowing staff to focus on repairs and customer satisfaction. For instance, a good work order system can automate notifications for customers regarding their vehicle's status. You can also schedule maintenance work based on customer preferences and vehicle history. So instead of juggling papers and spreadsheets, everything can be neatly organized on one platform. The result? Quicker turnaround times and a happier clientele, much like a well-oiled machine running smoothly.
Enhanced Customer Communication
In the auto repair industry, communication is crucial. Customers often feel anxious about the condition of their vehicles and the costs involved in repairs. A work order system facilitates effective communication between the shop and its clientele. Imagine sending instant updates via text or email about the progress of repairs. It's all about keeping the lines open.
A robust software solution enables staff to easily access customer histories, preferences, and previous services. This context helps in personalizing interactions, making customers feel valued. In an environment where trust is paramount, reassuring a customer that you know their vehicle well can go a long way. This fortifies the relationship and improves the chances of repeat business, akin to a handshake sealing a deal.
Data Management and Reporting
Effective data management is leading to more informed decision-making. With comprehensive auto repair work order software, shops can collect and analyze vast amounts of data. From tracking repair progress to managing inventory levels, the insights gained from data reporting can immensely impact operational efficiency.
Using this software, businesses can easily generate reports and analyze trends over specific periods. For example, if a particular service is frequently requested, the shop can adjust its marketing strategies accordingly or stock up on necessary parts. Not only does it protect against inventory shortages, but it paves the way for better financial planning.
The power of data can be transformative for any auto repair shop, helping to refine processes and enhance profitability.
In summary, the benefits of using work order software extend far beyond mere convenience. By increasing efficiency, enhancing communication with customers, and facilitating improved data management, the software acts as a backbone for any modern auto repair shop. As the industry evolves, embracing these tools will position businesses ahead of the curve.
Essential Features to Consider
When delving into auto repair work order software, understanding the essential features is paramount. The right software can significantly bolster the overall efficiency of an auto repair business, aligning its workflows with customer demands and operational goals. Selecting a system with the necessary elements is a stepping stone toward optimizing your repair operations.
User-Friendly Interface
Imagine walking into a garage filled with tools scattered everywhere; it would feel chaotic. Now, think of a neat toolbox where everything is organized. That's the difference a user-friendly interface makes in software. A clean and intuitive design allows technicians and staff to access necessary information without sifting through menus upon menus.
It’s crucial that the software provides a seamless experience that facilitates ease of use. Staff, who might not be tech aficionados, should be able to navigate without feeling lost or overwhelmed. This reduces the likelihood of errors and ensures that tasks can be completed quickly.
Integration Capabilities
Auto repair shops often utilize a variety of systems for inventory, accounting, and customer relationship management. If work order software doesn’t integrate well with these existing systems, it can create a jumbled mess. Integration capabilities serve as the glue that holds everything together, allowing data to flow smoothly between platforms.
Some key considerations include:
- Compatibility with accounting software like QuickBooks or Xero.
- Useful APIs for custom solutions.
- Linkages with parts suppliers or inventory management tools.
An integrated system means one central hub where all essential functions can be accessed, cutting down redundancy and improving productivity.
Mobile Accessibility
In the fast-paced world of auto repairs, technicians often move from one vehicle to another, tackling issues head-on. Mobile accessibility allows them to check work orders, update statuses, or communicate with customers right from their smartphones. This feature enhances convenience and keeps everyone in the loop regardless of location within the shop.
Mobile software should be responsive and not merely a stripped-down version of the desktop application. It should provide comprehensive features, so technicians do not miss out on critical updates or needed information. The ability to access the software on-the-go dramatically increases responsiveness and customer satisfaction because issues can be resolved more efficiently.
An effective work order system is not just about managing tasks; it's about empowering teams to work smarter, not harder.
By considering these fundamental features—user-friendly interface, integration capabilities, and mobile accessibility—business owners can select the right work order software that aligns with their operational objectives, paving the way for enhanced efficiency in their auto repair services.
Comparative Analysis of Leading Software Solutions
When it comes to selecting the right auto repair work order software, a comparative analysis is not just a task; it's a necessity. Different software solutions cater to various needs, and understanding the nuances of each can save time and money while ensuring that businesses choose the right tool for their specific workflows. Depending on the size of the shop, the types of services offered, and customer expectations, the ideal software can greatly differ.
Evaluating the leading software options involves examining several key aspects, such as core features, pricing structures, and user experiences. By considering these elements, auto repair professionals can make informed decisions that enhance operational efficiency and customer satisfaction.
Core Features Comparison
At the heart of any software solution lies its features. The effectiveness of work order software hinges on its core functionalities. A basic comparison should include:
- User Interface: A clean and intuitive interface can significantly improve user adoption. Some products offer drag-and-drop functionality, while others may necessitate more training.
- Scheduling and Dispatching: The ability to manage multiple jobs simultaneously and assign tasks effectively can streamline repairs. Moreover, tools that sync with calendars make it easier for shops to keep track of appointments.
- Inventory Management: This is critical for ensuring the right parts are available when needed. Differences often lie in the ability to integrate with suppliers for reordering.
- Invoice Generation: The best solutions allow for quick and accurate invoice creation, reducing the time staff spend on billing. Optional add-ons might include customer payment processing capabilities.
- Reporting and Analytics: Some software solutions offer robust reporting tools that assist in tracking performance metrics such as job times, labor costs, and customer satisfaction. Such data can guide decision-making and strategy.
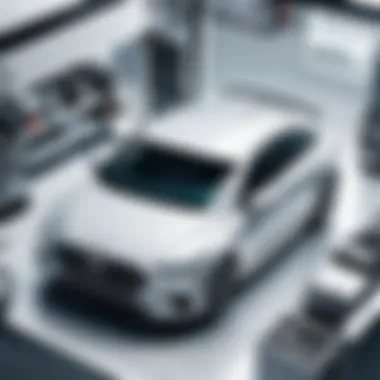
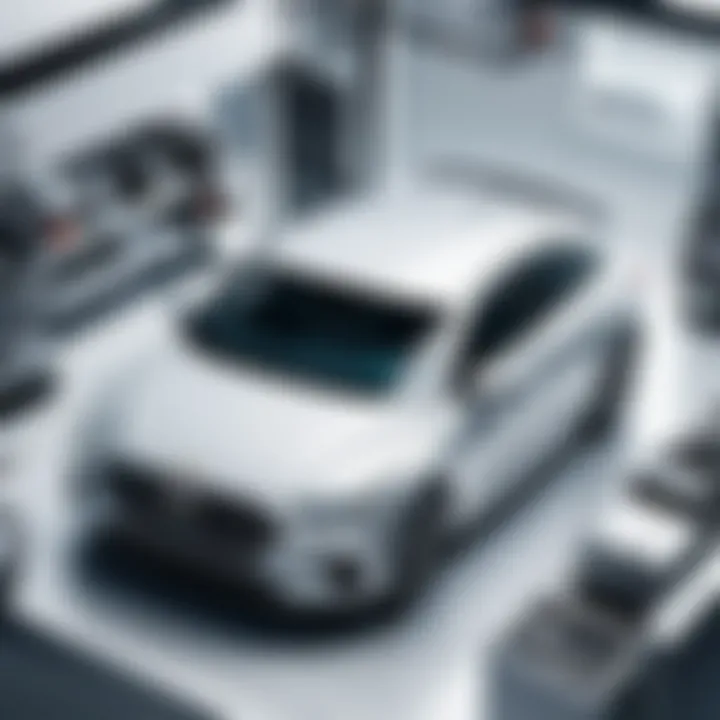
Pricing Structures
While features are paramount, the pricing structure is equally important. Understanding the costs involved can prevent unexpected financial strain. Here are a few common pricing models:
- Flat Fee: Some systems require a one-time payment for ownership. This can be appealing for businesses that prefer to avoid recurring costs.
- Subscription: Many companies offer monthly or annual subscription fees. This model often comes with frequent updates.
- Pay-per-Use: This model charges based on the number of work orders processed, which could be beneficial for smaller shops with variable workloads.
Being aware of hidden costs, like setup fees or charges for additional features, is crucial in this analysis.
User Satisfaction and Feedback
To round out the comparative analysis, understanding user satisfaction comes into play. This often involves delving into reviews and feedback from other technicians and shop owners.
- Online Reviews: Websites such as Reddit and Facebook are useful for gathering genuine user comments. Users often discuss software experiences, highlighting both pros and cons that can inform your decision.
- Case Studies: Many software companies release success stories or testimonials from clients. These can demonstrate real-world performance and usability.
- Customer Support: Reviews also frequently mention the quality of customer support. A software solution may function well, but poor customer service can lead to frustration down the line.
"Selecting the right software isn’t just about features and price—it’s about finding a tool that fits into your existing workflow and enhances it."
In wrapping up this section, it's clear that conducting a thorough comparative analysis is a critical step in selecting the right auto repair work order software. With multiple solutions available, scrutinizing each option across these key dimensions will aid in making an informed choice that can significantly benefit the entire operation.
Challenges in Implementing Work Order Software
Implementing work order software in an auto repair setting is no small feat. While the benefits can be enormous—streamlined processes, improved communication, and better financial tracking—there are significant hurdles that businesses must navigate. Understanding these challenges is crucial for making informed decisions and ensuring a successful implementation. Every shop might face its unique set of circumstances, but there are common challenges that tend to crop up considerably.
Initial Setup and Configuration
The initial setup and configuration of work order software can be a daunting task. First off, selecting the right software aligned with the business's goals is crucial. This often involves extensive research, comparing features, and seeking solutions that match specific operational needs. After the software is chosen, the next challenge lies in its setup.
Adapting the software to fit existing workflows can become a tangled web of adjustments. Key decisions around user roles, permissions, and data migration from previous systems must be made. A well-implemented setup often involves a trial and error phase, whereby organizations need to tweak the software to their liking. Minor errors can snowball into big issues down the line, so careful attention to detail is paramount.
Furthermore, integrating new software with existing platforms can create additional headaches. For instance, if a repair shop already uses certain inventory management systems, making them compatible with the new work order software can be akin to fitting a square peg in a round hole.
Staff Training Requirements
Once the software is set up, the real task begins: training the staff to use the system effectively. This can be particularly challenging in an industry known for high turnover rates. Technicians and administrative personnel have varying levels of tech-savviness, making uniform training a delicate balancing act. Some might promptly pick up the new system, while others may struggle, putting a strain on the overall productivity of the shop.
Creating a robust training program that accommodates diverse skill levels becomes vital. Clear manuals, engaging tutorials, and hands-on workshops can help, but they require time and resources to develop. Investing time in continuous training ensures that the team is not just familiar with the software, but truly competent in utilizing its full potential.
Ongoing Maintenance and Support
Even after a successful rollout and staff training, the journey doesn’t end there. Ongoing maintenance and support are critical to keep everything running smoothly. Regular software updates are necessary to keep the system current and secure, but they can also introduce new features that might confuse staff.
Moreover, providing ongoing technical support is essential for resolving issues that crop up during daily operations. Things like system outages or bugs need immediate attention; otherwise, they can lead to significant operational disruptions.
It's also valuable to establish a feedback loop where staff can report on usability and efficiency. Their experiences can guide updates and refinements, making the software wit better aligned with the day-to-day processes of the repair shop.
Key Takeaway: Implementing work order software can present challenges at every stage, from initial setup through to ongoing maintenance. A proactive approach and continuous improvement mindset can turn challenges into pathways for efficiency.
Best Practices for Maximizing Software Value
Maximizing the value of auto repair work order software requires a thoughtful approach. This is not just about selecting the right tool, but also implementing it strategically for optimal benefits. The auto repair industry is competitive, and businesses need every edge they can get. Practicing effective software management can enhance workflows, reduce costs, and even improve customer satisfaction. Here we explore some key principles to ensure that the software truly benefits your operations.
Regular Updates and Upgrades
In the realm of software, staying stagnant is akin to moving backwards. Regularly updating and upgrading your auto repair work order software keeps it aligned with technological advancements and changing industry standards. Failing to do so can leave a business vulnerable, susceptible to security risks, and unable to leverage new functionality that could enhance performance.
Updates often come packed with features designed to improve user experience and efficiency. For instance, a simple interface redesign might streamline the data entry process, saving valuable time. Upgrades may also introduce necessary compliance tools that aid in meeting evolving regulatory requirements.
- Routine check-ups: Schedule periodic reviews of the software vendor's update offerings.
- Adopt a proactive stance: Rather than waiting until there's a glaring issue, make updating a scheduled practice. This helps maintain system integrity and user confidence.
- Educate your team: Ensure everyone understands the advantages of updates to increase their willingness to adapt.
Being on the cutting edge is not just about functionalities; it is about fostering a culture of improvement.
Integrating Feedback Loops
The importance of feedback loops cannot be overstated. This practice involves regularly soliciting input from users about their experiences with the software. By integrating these loops into your operation, auto repair businesses can achieve remarkable insights into how the software functions in real-world situations.
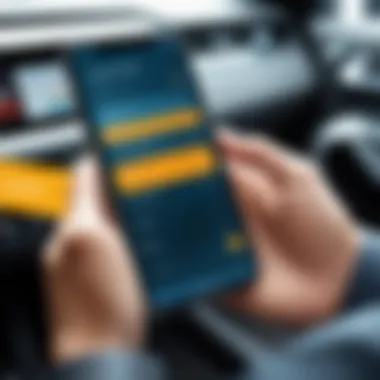
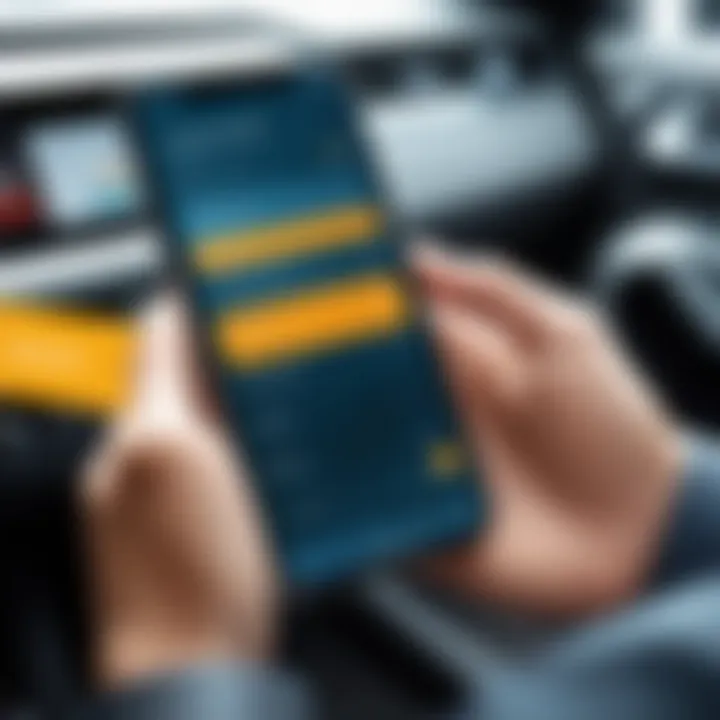
A robust feedback system serves multiple benefits:
- User-centered improvements: Your employees are the frontline users. Understanding their challenges allows for timely adaptations.
- Customer insight: Feedback can also come from customer interactions. This can inform adjustments that enhance the client’s journey.
- Adjusting training programs: Modify staff training based on gathered insights to ensure smoother software adoption across the organization.
- Establish channels: Platforms like an internal forum or dedicated email can facilitate open communication.
Establishing and maintaining effective feedback loops can transform operational bottlenecks into streamlined processes, enhancing both service delivery and employee engagement.
Performance Monitoring
Performance monitoring is a cornerstone practice that enables auto repair businesses to assess the efficacy of their work order software continuously. By keeping an eye on key performance indicators (KPIs), decision-makers can determine if the software meets its intended purposes and where further optimization may be necessary.
Utilizing tools that track usage, downtime, and error frequency helps visualize software impact in real-time.
- Choose specific KPIs: Consider metrics such as turnaround time for repairs, customer satisfaction scores, or employee productivity levels.
- Analyze trends: Regularly assess reports to spot patterns that could indicate issues or opportunities.
- Act swiftly: When data shows underperformance, mobilize resources to address root causes without delay.
As a constant compass to guide decisions, performance monitoring ensures that businesses are not just running but are operating as effectively as they possibly can.
Keeping your software on its toes is as crucial as the initial implementation. By integrating updates, feedback, and performance assessments into your routine, you not only protect your investment but also foster a culture of agility and responsiveness.
Future Trends in Auto Repair Software
Staying ahead in the auto repair industry often hinges on embracing future trends in work order software. The landscape is rapidly shifting due to technological advancements and changing customer expectations. It’s essential for business professionals to understand these trends not only for maintaining competitiveness but also for improving operational efficiencies and customer satisfaction. Adopting modern trends can save time, reduce errors, and ultimately boost profitability.
Incorporation of AI and Automation
Artificial Intelligence (AI) is no longer a concept limited to science fiction. In the realm of auto repair software, AI plays a pivotal role in optimizing processes. Imagine software that learns from past work orders and suggests solutions based on previous successes. This technology can significantly reduce the time it takes to diagnose issues. Automation goes hand-in-hand, enabling routine tasks such as inventory management and appointment scheduling without human intervention. For instance, when a part is low in stock, the software can automatically reorder it. Such features not only save time but also decrease the likelihood of errors that might occur with manual processes.
"AI is transforming the auto repair industry, making operations leaner and smarter. Embracing this technology isn't just a trend; it's a necessity."
Remote Diagnostics Capabilities
Remote diagnostics represents a game-changer in auto repair services. With these capabilities, technicians can assess vehicle issues without being physically present. Think about the convenience for your customers when they don’t have to tow their car to the shop for simple diagnostics. This technology allows mechanics to run initial checks and provide instant feedback, enabling quicker resolutions and enhancing customer experience. Moreover, businesses can tap into remote diagnostics as a selling point, promoting the ability to troubleshoot concerns swiftly from their customers’ driveways.
Cloud-Based Solutions
Cloud technology has become the backbone of many modern business operations. For auto repair shops, cloud-based software provides unparalleled advantages. Such platforms offer flexibility and scalability that remain unrivaled. A cloud solution allows technicians to access work orders from anywhere, whether they are on-site or in the field. Since data is stored offsite, it is also safer from local hardware failures. Additionally, backup and updates are simplified with cloud services, freeing staff to focus on providing quality services rather than managing IT issues. The cost-effectiveness of subscription models also means that shops can invest back into their operations without heavy upfront costs.
Selecting the Right Work Order Software
Choosing the appropriate work order software is a critical juncture for any auto repair business. After all, this tool will not only impact operational efficiency but also customer satisfaction and overall profitability. In a world where technology evolves swiftly, aligning software capabilities with specific business objectives can save time and money, and ultimately, strengthen service delivery.
Identifying Specific Business Needs
Before diving headfirst into selecting a software solution, it’s imperative to take stock of the unique needs within your repair shop. Think of business needs as fingerprints; no two shops are alike. Factors like size, type of services offered, and even customer demographics will greatly influence the kind of software best suited for your establishment.
Consider an auto shop that specializes in luxury vehicles. Its service order software must have features that accommodate detailed records of premium vehicle specifications and a user interface that conveys professionalism. In contrast, a high-volume, quick-service shop might prioritize speed and efficiency above all else. Thus, their choice will lean towards software with fast operations, easy access to work orders, and seamless integration with payment systems.
Additionally, engaging with team members who directly handle these systems can uncover insights that may not be immediately apparent. Their daily interactions with existing systems and workflow processes can provide valuable perspectives on what features are most necessary. In some cases, a simple conversation can reveal glaring gaps that need to be filled.
Comparative Demos and Trials
Once you’re armed with a clear understanding of your needs, it’s time to roll up your sleeves and explore the options available on the market. Most reputable software providers offer demo versions or trials. Taking advantage of these is essential. It’s one thing to read about features, but experiencing them firsthand can either validate or entirely rethink your selection.
During a demo, pay attention not just to the software’s capabilities but also to its user experience.
- How intuitive is the interface?
- Are tasks easily navigable?
- Can your technicians quickly generate work orders without feeling like they need a degree in computer science?
It's also wise to conduct trials across different teams within your shop if possible. This approach can provide a multi-faceted view of how well the software integrates into your diverse workflows.
Budget Considerations
Budget might feel like a limiting factor in your selection process, but it doesn’t have to be. Approaching this aspect with a mindset of value rather than expense can shift your perspective. When calculating the budget for work order software, consider not only the upfront costs but also ongoing expenses such as monthly fees, training, and potential upgrade costs.
While it might be tempting to go for the cheapest option, weigh it against the features provided. A software that facilitates quicker service turnaround due to its efficient work order processing can save time that translates into money. For instance, investing in a slightly pricier solution with robust analytics capabilities can help in understanding customer behavior and business trends, ultimately leading to better-informed strategic decisions.
Establishing a detailed budget that clearly weighs initial investments against long-term gains can open up possibilities that fit your financial plans. The goal is to find a balance that doesn’t leave your bank account feeling lighter while also not compromising on service delivery.
"Choosing the right tools can set the pace for your operational success, creating pathways to streamline your workflow and boost overall productivity.”
In sum, the process of selecting work order software entails a careful assessment of your repair shop's distinct needs, thorough testing of potential software solutions, and a strategic approach to budgeting. By taking these steps, you'll be well on your way to enhancing your auto repair operations and cementing customer trust.