Maximizing Efficiency with MP Software and CMMS Solutions
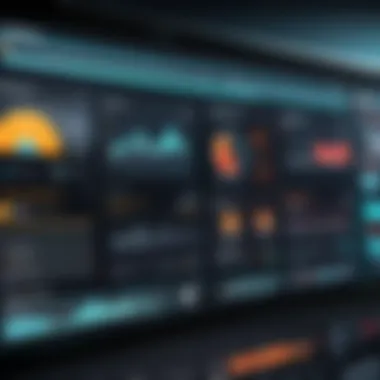

Intro
In today’s fast-paced industrial landscape, no one can afford to lag in efficiency. That’s where Maintenance Planning (MP) software and Computerized Maintenance Management Systems (CMMS) come into play. These digital tools are shaping how organizations manage their maintenance activities, making them more streamlined and effective. The integration of such systems not only changes routine operations but aims at prolonging the life of assets and boosting productivity.
It’s essential to grasp the intricacies of MP software and CMMS, since they offer a lifeline for those seeking to minimize downtime and enhance operational efficiency. This article will dissect the functionalities and benefits of these systems while providing insights into how they line up with varying industry requirements. Let’s delve deeper into what these tools are all about.
Software Overview
Software Category and Its Purpose
MP software and CMMS solutions fit under the broader umbrella of maintenance management technology. Their fundamental aim is straightforward: to keep assets running smoothly. By employing these systems, organizations can effectively schedule maintenance tasks, track work orders, and manage inventory of spare parts—all of which contribute to an optimized maintenance process.
The heart of these systems is the ability to centralize information, reducing the amount of time spent tracking down data across disparate sources. For instance, pulling maintenance records or generating reports can be laborious and prone to human error without a unified system in place.
Key Features and Functionalities
When assessing MP software and CMMS products, there are certain features that are crucial. Notably:
- Work Order Management: This allows users to generate, track, and close work orders efficiently.
- Asset Tracking: Users can monitor asset performance, ensuring timely maintenance and repairs.
- Reporting and Analytics: Users can gather insights on maintenance efficiency, which helps drive informed decision-making.
- Inventory Management: Handling spare parts and supplies effectively to avoid bottlenecks.
- Mobile Access: Increasingly, these systems offer mobile functionality, providing field technicians immediate data at their fingertips.
These features become pivotal in empowering teams to maintain transparency and accountability throughout the maintenance process, ultimately fostering a culture of continuous improvement in organizations.
Comparative Analysis
Comparison with Similar Software Products
In the bustling marketplace of maintenance solutions, the distinction between various software products often comes down to their specific features and usability. For instance, let's look at a common comparison:
- MP Software: Typically focuses on workload balancing and forecasted maintenance schedules.
- CMMS Solutions: These generally offer a more integrated approach, encompassing various functions including inventory and asset management.
While both serve key roles, choosing the right one depends heavily on organizational needs and how complex their maintenance operations are.
Market Positioning and User Demographics
MP software and CMMS solutions position themselves differently depending on their user demographics. Industries such as manufacturing, healthcare, and education are increasingly digitizing their maintenance efforts, paving the way for these tools. Users tend to range from small business owners needing straightforward solutions to large enterprises requiring comprehensive, multifaceted systems. Understanding who the target users are allows organizations to tailor their offerings effectively, ensuring a fit for their clients' needs.
"The adoption of MP software and CMMS is not merely a trend; it's a strategic move towards operational excellence."
By comprehensively navigating the landscape of these systems, organizations can lay a solid foundation for maximizing efficiency and fostering an environment that supports data-driven maintenance practices.
Understanding Maintenance Planning Software
Maintenance Planning (MP) software forms an integral part of any organization's approach to asset management and operational efficiency. It is not merely a tool but a strategic component that ensures maintenance activities are executed with precision and foresight. When you think about it, the lifeblood of any manufacturing or service-based operation is the functionality of its equipment and systems. This is where MP software shines, allowing organizations to maintain high levels of operational readiness while minimizing downtime and costs.
Defining Maintenance Planning Software
At its core, maintenance planning software helps organizations plan, schedule, and track maintenance activities. This software serves as a centralized hub for information related to maintenance tasks, resources, and operational workflows. It allows maintenance teams to move beyond reactive maintenance, which often leads to unexpected equipment failures and costly repairs, and adopt a proactive approach.
In clearer terms, think of it as a map that guides your journey toward more reliable operations. By defining what needs to be done, who will do it, and when, MP software streamlines the entire maintenance process.
Key Features of MP Software
When considering the implementation of MP software, a few critical features should stand out:
- Scheduling capabilities: This allows users to create maintenance schedules based on equipment usage and manufacturers' recommendations.
- Inventory management: This component tracks spare parts, ensuring that essential components are on hand when needed, preventing unnecessary delays.
- Reporting and analytics: It collects data on maintenance activities, helping identify patterns and forecast future maintenance needs.
These features empower organizations to adapt to changing maintenance requirements seamlessly. They act as the evolution of traditional spreadsheets and paper logs that are often fraught with errors and inefficiencies.
Benefits of Implementing MP Software
The benefits of implementing MP software are not just theoretical; they can significantly impact an organization’s bottom line. For instance:
- Increased equipment uptime: By planning maintenance tasks more effectively, organizations can reduce equipment failures, leading to higher productivity.
- Reduction in labor costs: With optimized scheduling, labor resources can be used more efficiently, reducing overtime and unnecessary staff expenditure.
- Improved decision-making: The data collected provides insights that inform strategic decisions regarding equipment upgrades, replacements, or service contracts.
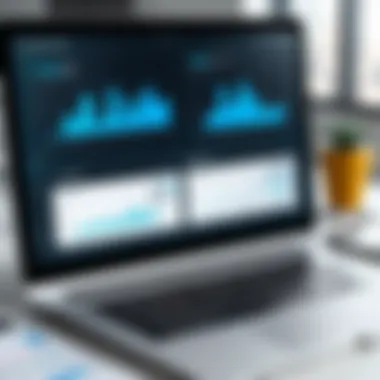

In essence, as organizations delve deeper into the world of MP software, they unlock a treasure trove of possibilities that ultimately guide them toward operational excellence.
"The adoption of Maintenance Planning software is not just an operational upgrade, it's a mindset shift toward strategic asset management and efficiency."
Employing MP software is akin to laying a sturdy foundation before constructing a building. It sets the stage for smoother operations and a more resilient and adaptable organization.
Exploring CMMS Functionality
When considering how to streamline maintenance processes, delving into the functionality of Computerized Maintenance Management Systems (CMMS) is crucial. CMMS not only helps in managing the nitty-gritty of maintenance tasks but also plays a pivotal role in enhancing overall operational efficiency. By understanding how these systems work and the specific benefits they bring, organizations can cultivate a more organized and proactive maintenance strategy.
What is a CMMS?
A Computerized Maintenance Management System (CMMS) is a software solution designed to simplify the maintenance of equipment and facilities. At its core, CMMS provides the tools needed for tracking the maintenance data required to keep operations running smoothly. This software allows businesses to schedule maintenance tasks, record work orders, and manage inventory—all essential components for any organization aiming to optimize its resources.
In a typical setting, CMMS acts as the central hub where all maintenance activities converge. Instead of relying on disparate spreadsheets or fragmented systems, CMMS centralizes information, making it easily accessible to all relevant parties, from technicians to management.
Core Components of CMMS
Understanding the core components of CMMS can illuminate how this software maximizes efficiency. Here are some key elements to consider:
- Work Order Management: One of the principal features, this allows for the creation, assignment, and tracking of work orders. Having everything in one place helps eliminate confusion and delays.
- Preventive Maintenance Scheduling: This function automates the scheduling of routine tasks, ensuring that maintenance is carried out at the right intervals, which helps prevent costly downtime.
- Asset Management: This aspect involves tracking asset history, maintenance schedules, and performance metrics. It's essential for understanding the total cost of ownership and making informed decisions about asset lifecycle management.
- Inventory Management: A robust CMMS allows for tracking spare parts and inventory levels, helping to ensure that all necessary materials are on hand when maintenance work is needed.
"In today's fast-paced operations, a well-implemented CMMS can be the difference between seamless maintenance and a costly breakdown."
How CMMS Enhances Maintenance Efficiency
There is no doubt that CMMS enhances maintenance efficiency, but how exactly does it achieve this? For starters, CMMS provides real-time data and analytics, allowing decision-makers to make informed choices based on actual performance metrics.
By streamlining work order management, technicians spend less time searching for tasks or approvals, which translates to faster response times. The software also minimizes human error by automating many maintenance tasks. This gets rid of the guesswork involved in scheduling and improves compliance with maintenance protocols.
Another area where CMMS excels is in preventative maintenance. The proactive approach of scheduling regular maintenance checks through the system drastically reduces the likelihood of equipment failure, thus inches businesses toward uninterrupted productivity.
In a nutshell, CMMS combines flexibility with data-driven insights, offering organizations a comprehensive view of their maintenance operations, making it easier to identify areas needing improvement and ensuring that every asset is functioning at its best.
The Intersection of MP and CMMS
The synergy between Maintenance Planning (MP) software and Computerized Maintenance Management Systems (CMMS) is not just a convenient coupling; it’s a pivotal alliance that can redefine an organization’s approach to maintenance. Understanding this intersection allows businesses to maximize their operational efficiency by streamlining processes and improving asset management. When both systems work together, they create a more comprehensive maintenance solution that can tackle complex challenges in today’s fast-paced business environment.
Integrating MP Software with CMMS
Integrating MP software with CMMS is where the real magic happens. This partnership means you’re not just using separate tools, but rather creating a cohesive environment for data management. Think of it like a well-oiled machine—every cog turns smoothly with minimal friction.
When MP software seamlessly integrates with CMMS, organizations can automate scheduling based on predictive analytics. The system can pull up maintenance histories, inventory levels, and even provider availability, allowing managers to generate timely work orders. The operation becomes synchronized. This translates into less downtime, as teams can anticipate and act on maintenance needs rather than reacting to breakdowns.
Key points to consider when integrating MP with CMMS include:
- Data compatibility ensures that both systems can share data without loss or corruption.
- User access levels help maintain security while also allowing relevant teams to access necessary information.
- Training requirements for staff to ensure they understand how to utilize both systems effectively.
Synergistic Benefits of Integration
The benefits of integrating MP software and CMMS are multifaceted and significant. Perhaps one of the most compelling advantages is the enhanced decision-making process. When an organization has access to a wealth of reliable data drawn from both systems, it becomes easier to forecast maintenance needs and allocate resources efficiently. This results in optimized workflows and improved asset longevity.
Moreover, the integration fosters a culture of data-driven maintenance practices, where insights gleaned from analytics can lead to more proactive maintenance, thus reducing unexpected failures. This foresight can save considerable costs that arise from emergency repairs and asset replacements.
"By harnessing the combined power of MP software and CMMS, companies can build a robust framework that not only increases efficiency but also paves the way for sustainable maintenance cultures."
Other synergistic benefits can include:
- Increased collaboration across departments, encouraging a shared responsibility for maintenance outcomes.
- Streamlined reporting, allowing organizations to visualize performance metrics, identify trends, and make timely adjustments.
- Resource optimization, as integrated systems allow for better planning and reduction of redundant tasks.
In the realm of maintenance management, ignoring the integration of MP software with CMMS may hold organizations back from achieving their full potential. The alignment of these two systems isn’t just a technical upgrade; it’s a necessity for businesses aiming to thrive in a competitive landscape.
Selecting the Right Software Solution
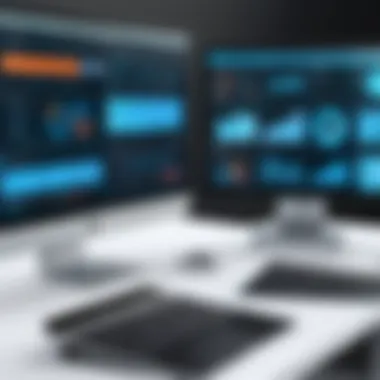

Choosing the right software solution for Maintenance Planning (MP) and Computerized Maintenance Management Systems (CMMS) is an instrumental step for organizations aiming to boost their operational efficiency. Given the breadth of choices available, it’s not just about picking any software; it’s about finding a system that amalgamates seamlessly with the organization’s unique processes and needs. This section simplifies the selection process by breaking it down into three critical components:
Identifying Organizational Needs
Before you dive into the software market, the first order of business is understanding what your organization specifically requires. Every company is a snowflake; different sizes and shapes lead to distinct needs.
- Assess Current Processes: Take stock of existing practices. What’s working? What isn’t? By understanding the bottlenecks in your current system, you can pinpoint features that a new software ideally should have.
- Consult Stakeholders: Engage with team members from various departments. Maintenance, operations, management—everyone may have a different perspective on what a solution should offer. It can pay to take a democratic approach rather than just leaning on upper management's view.
- Define Key Objectives: What do you want to accomplish with MP or CMMS software? Is it reducing downtime, extending asset lifespan, or perhaps optimizing spare parts inventory? Clearly outlined objectives will guide your search, ensuring that any potential purchase aligns with these aims.
Comparing Software Options
After pinpointing your organizational needs, it's time to hit the catalog. This is where the rubber meets the road. When evaluating different software options, don’t just stick to surface-level features; dig deeper:
- Feature Evaluation: Different software solutions might boast unique features like predictive maintenance functionality or mobile accessibility. Prioritize the features that align closely with your established needs.
- Usability: Simplicity goes a long way. If the interface is more complicated than rocket science, your team may resist using it despite its functionalities. Consider systems with intuitive designs.
- Integration Capabilities: Compatibility with existing systems is crucial. Look for software that can harmoniously integrate with your current IT infrastructure without requiring a complete overhaul.
- Vendor Reputation: Research the vendors. What’s their track record? Read user reviews to gauge how reliable their support is. You can check platforms like Reddit for candid opinions from real users.
Evaluating Cost vs. Value
Now comes the money talk. When examining costs, keep in mind the phrase, "you get what you pay for" is often true in software.
- Initial Investment: Beyond the sticker price, consider implementation costs, which can sometimes be astronomical. Check to see if the vendor offers hidden features that could rathere go unnoticed until it's too late.
- Ongoing Costs: Subscriptions, updates, and support can all pile up over time. Evaluate how these fit into your budget in the long haul.
- ROI: Analyze the return on investment. Will this software save time and resources? What about potential revenue increase due to improved efficiencies? Calculating tangible benefits against costs will offer a clearer picture.
"An intelligent choice today can save mountains of resources tomorrow."
Pondering on these considerations will not only help in selecting the software most fit for your organizational puzzle but can also act as a litmus test for future software purchases. Because the end goal is to find a solution that not only looks good on paper but also works like a charm in practice.
Implementation Challenges
Implementing Maintenance Planning (MP) software and Computerized Maintenance Management Systems (CMMS) can be a double-edged sword. On one hand, these tools have transformative potential, capable of streamlining operations and increasing efficiency. However, the path to successful implementation is often riddled with challenges that can derail even the most well-intentioned plans. Understanding these hurdles is crucial. It enables organizations to recognize potential risks early and take proactive measures to mitigate them. Striking a balance between embracing technological enhancements and navigating the intricacies of implementation is essential to maximizing the benefits of these systems.
Common Pitfalls in Implementation
Several snags can hinder the smooth integration of MP software and CMMS into existing workflows. Here are some common pitfalls:
- Lack of Clear Objectives: Entering an implementation without defined goals is like setting sail without a compass. Organizations need to have clarity on what they aim to achieve with the new systems.
- Underestimating Training Needs: Training isn't merely an afterthought; it's a cornerstone of successful implementation. Not providing adequate training can lead to user frustration and under-utilization of the software.
- Data Migration Issues: Transferring existing data to the new system can be fraught with challenges. Inconsistent data formats and incomplete information can undermine the system's effectiveness from the get-go.
- Ignoring User Buy-In: If the staff doesn't see the value in the new tools, resistance may arise. Employees play a pivotal role in the success of any software. Without their support, even the best-laid plans can go awry.
"Failing to prepare is preparing to fail."
- Overlooking System Customization: Every organization is unique. Overlooking the need for customization can lead to workflows that are misaligned with actual business processes, thus negating the benefits.
Strategies for Overcoming Challenges
Addressing these pitfalls requires deliberate planning and execution. Here are strategies that can help navigate the complexities:
- Define Clear Goals: Setting specific, measurable goals for what you want to achieve with MP software and CMMS lays a strong foundation. This helps in aligning the software functionalities with business needs.
- Invest in Comprehensive Training: Allot sufficient time and resources for training. Ongoing support and resources can ensure that users are confident and competent in utilizing the software.
- Plan for Data Migration: Before implementation, evaluate the data that needs to be migrated. Define standards for acceptable data, and consider running pilot programs with smaller datasets first to identify issues early on.
- Engage Users Early: Involve key staff members in the planning and selection process to foster ownership and acceptance. Gathering their insights can also lead to better tools tailored to real-world needs.
- Customize Thoughtfully: While it's tempting to stick to standardized versions of software, customized configurations can often meet unique challenges better. Work with vendors to tailor solutions to fit organizational workflows seamlessly.
By proactively addressing these considerations, organizations can pave the way for smoother implementation of MP software and CMMS, ultimately reaping the rewards in improved efficiency and operational success.
Impact on Operational Efficiency
In the realm of industrial operations, the importance of enhancing operational efficiency cannot be overstated. As businesses grow and evolve, the integration of Maintenance Planning (MP) software and Computerized Maintenance Management Systems (CMMS) has become critical in ensuring that organizations not only meet their maintenance needs but also optimize their overall performance. The impact these tools have is far-reaching, directly influencing productivity, cost management, and asset longevity.
One of the standout elements of operational efficiency is the significant reduction in downtime. When machines and equipment are well-maintained, the likelihood of unexpected failures decreases, allowing organizations to carry on with their production schedules uninterrupted. It's not just about fixing what’s broken; it’s about implementing a proactive maintenance strategy that anticipates issues before they arise.
The final analysis of performance metrics serves as a backbone for this strategy. By establishing clear KPIs and consistently analyzing data, companies can track their progress and adapt their methods based on real-time performance. This not only fosters a culture of continuous improvement but also aligns operational practices with higher-level business goals.
Analyzing Performance Metrics
Diving into performance metrics is like taking the pulse of an organization’s maintenance efforts. Effective metrics are not just numbers on a report; they tell a story about how the maintenance program is functioning A well-structured MP software paired with a robust CMMS can provide insights that drive informed decision-making.
Here are some key performance metrics that organizations frequently evaluate:
- Mean Time Between Failures (MTBF): This metric helps gauge how often failures occur. A lower MTBF indicates a problematic asset requiring immediate attention, while a higher MTBF signals effective maintenance efforts.
- Mean Time to Repair (MTTR): This measures the average time necessary to repair a failed asset. Keeping this number low translates to less downtime and improved productivity.
- Asset Utilization Rate: This indicates how effectively an asset is being used in comparison to its capacity. A high utilization rate suggests a well-planned maintenance strategy that keeps equipment running efficiently.
The importance of regularly updated performance metrics cannot be underestimated. They ensure timely interventions, ultimately prolonging asset life and optimizing resource allocation.
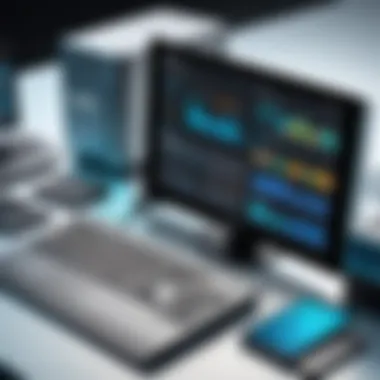

Case Studies of Successful Implementations
To truly understand the impact of MP software and CMMS solutions on operational efficiency, one must look at real-world successes. Examining case studies demonstrates how various organizations have leveraged these tools to drive notable improvements in maintenance processes.
- A Manufacturing Plant: A large appliance manufacturer implemented a CMMS alongside MP software. This combination resulted in enhanced scheduling capabilities, decreasing unplanned downtime by 30%. By switching to a proactive maintenance approach, the plant reported not only less disruption but also improved product output, translating to increased revenues.
- Healthcare Facility: A regional hospital adopted a CMMS for tracking and managing their medical equipment maintenance. This shift allowed them to maintain compliance with health regulations efficiently. Furthermore, they reduced repair costs by 20% while improving patient safety through timely interventions.
- Transportation Company: In the logistics sector, a prominent transportation firm integrated MP software that provided real-time tracking of fleet maintenance. As a result, they saw a drop in service interruptions and fuel costs, boosting operational efficiency drastically.
Emerging Trends in MP and CMMS
As organizations increasingly prioritize efficiency in maintenance management, it's vital to keep an eye on emerging trends in Maintenance Planning (MP) software and Computerized Maintenance Management Systems (CMMS). With technology continuously evolving, understanding these trends can enable businesses to enhance operational effectiveness, better adapt to changing environments, and make the most out of their resources.
Innovations Shaping the Future
The technological advancements in maintenance software are quite astounding. Business leaders now have access to cloud-based solutions, allowing for real-time data access and collaboration across teams. Imagine being able to view maintenance schedules, equipment history, and inventory instantly—no matter where you are. This kind of accessibility not only boosts communication but also streamlines decision-making processes.
- IoT Integration: The Internet of Things (IoT) is one of the most significant innovations impacting MP and CMMS solutions. By linking equipment with sensors, organizations can gather crucial data about machinery health. This real-time data provides insights that help in predicting when a piece of equipment may malfunction, leading to timely maintenance and reduced downtime.
- Mobile Accessibility: More and more MP software and CMMS are being optimized for mobile devices. Service technicians can check work orders, log repairs, and update inventory from their smartphones. This means they spend less time in front of a computer screen and more time addressing maintenance needs directly at the site.
- Enhanced User Experience: Software developers are focusing on creating user-friendly interfaces. Intuitive dashboards that visualize key performance metrics make it easier for non-technical users to navigate and utilize these complex systems effectively.
"Staying abreast of software trends isn't just about keeping up; it's about future-proofing your organization."
The Role of AI and Machine Learning
Artificial Intelligence (AI) and machine learning are game-changers in the maintenance sector. These technologies not only simplify processes but also provide deeper insights into how assets perform over time.
- Predictive Maintenance: Businesses can use AI algorithms to analyze historical maintenance data combined with real-time input. This allows for statistical models to predict potential failures before they occur, reducing costs tied to unplanned downtime.
- Automated Alerts and Reporting: Machine learning can learn from past incidents and generate alerts when certain conditions or patterns surface, allowing preventive actions to be taken automatically. This relieves staff from manually monitoring systems, thus allowing them to focus on more complex tasks.
- Resource Optimization: AI analyzes usage patterns and suggests optimal resource allocation, ensuring that the right tools and personnel are available when needed. Such targeted resource management can lead to significant cost savings.
Best Practices for Maintenance Management
Effective maintenance management is the backbone of operational efficiency, underpinning the success of both small enterprises and large corporations alike. Best practices in this field guide organizations towards creating strategies that not only ensure the longevity of their assets but also optimize resources and reduce downtime. Applying these principles can lead to profound benefits, such as increased productivity, lower maintenance costs, and improved safety standards.
Establishing Maintenance KPIs
Key Performance Indicators (KPIs) are essential metrics that help organizations gauge their maintenance effectiveness. Establishing KPIs can transform the general approach to maintenance into a data-driven system. Selecting appropriate KPIs involves understanding what really matters in the context of your specific organization.
Some common KPIs to consider include:
- Mean Time Between Failures (MTBF): This metric measures the average time between equipment failures, helping to assess reliability.
- Mean Time To Repair (MTTR): This indicates how long it takes to repair equipment after a failure, reflecting responsiveness.
- Overall Equipment Effectiveness (OEE): This KPI combines the availability, performance, and quality of production, providing a comprehensive view of operational efficiency.
It's critical to choose KPIs that align with organizational goals. Initial discussions can help pinpoint the KPIs that matter most. For instance, a manufacturing plant might focus on MTBF and MTTR, while a service provider may look at customer satisfaction or service response times. By revisiting these metrics regularly, companies can identify areas for improvement and adjustments in their maintenance strategies.
Creating a Maintenance Culture
Building a proactive maintenance culture requires a shift in how employees and management perceive maintenance work. Rather than viewing maintenance as a necessary evil, it should be positioned as a vital element of operational excellence. A maintenance culture thrives on communication, collaboration, and a shared understanding of strategic goals.
To foster such a culture:
- Educate Employees: Regular training sessions can help everyone understand the crucial role maintenance plays within the organization.
- Encourage Feedback: A two-way feedback mechanism allows staff to provide insights on equipment issues or maintenance processes, which can lead to significant improvements.
- Acknowledge Contributions: Recognizing employees' efforts in maintaining equipment encourages them to take ownership, fostering pride in their work.
The establishment of a maintenance culture boosts morale and promotes accountability, making it easier for teams to work together towards shared objectives.
These efforts combined can lead to a more engaged workforce that prioritizes maintenance initiatives, ultimately resulting in lowered operational costs and a smoother workflow. Understanding and implementing these best practices will enhance maintenance management and maximize the efficiency of both MP software and CMMS solutions.
End
In the fast-paced world of maintenance and operations, the importance of effectively managing and integrating Maintenance Planning (MP) software with Computerized Maintenance Management Systems (CMMS) cannot be overstated. These tools serve as the backbone of an organization's maintenance strategy, streamlining processes and enhancing efficiency. The insights garnered throughout this article underline how vital it is for companies to understand the full scope of these technologies.
Delving into this topic reveals several key elements:
- Operational Efficiency: One of the most significant benefits of utilizing MP software and CMMS is a notable increase in operational efficiency. These systems enable organizations to plan, track, and execute maintenance tasks with precision, reducing downtime and prolonging asset life.
- Data-Driven Decisions: Implementing these solutions fosters a culture of data-driven decision-making. Decision-makers will have access to accurate data analytics from maintenance activities, empowering them to make informed choices that align with business objectives.
- Cost Management: The right combination of MP and CMMS can lead to substantial cost savings. By predicting and preventing equipment failures, organizations can avoid unexpected repairs and optimize resource allocation, translating to better financial health.
- Adaptability and Scalability: In a landscape where change is the only constant, these software solutions provide the flexibility businesses need to adapt. Whether it's adapting to new technologies or scaling operations, MP and CMMS enable seamless transitions.
"Success in maintenance management hinges on leveraging the right tools to enhance productivity and minimize waste."
In summary, the culmination of the information presented illustrates not just the functionality of MP software and CMMS but also their strategic significance. Organizations must consider these solutions as integral components of their maintenance strategies, as they pave the way for achieving long-term success in operational excellence. With the right tools at their disposal, businesses can navigate the challenges of maintaining assets while projecting a forward-thinking image in a competitive market.
Summarizing Key Takeaways
To wrap things up, several takeaways emerge that encapsulate the importance of MP software and CMMS:
- Integration is Key: The interconnectivity of MP software and CMMS leads to a more robust maintenance framework. By ensuring these systems work together, organizations can maximize their full potential.
- Data-Driven Culture: Embracing a data-centric approach fosters smarter operations and decisions based on analytical insights rather than intuition.
- Cost Efficiency: Investing in integrated software may seem daunting, but the long-term savings on repairs and improved productivity justify the investment.
- Continuous Improvement: Leveraging feedback from maintenance activities can propel organizations toward continuous improvement and better practices.
- Stay Ahead of Trends: Keeping an eye on emerging trends and innovations ensures that companies remain agile and can take advantage of new opportunities for improvement.
By absorbing these core concepts, businesses are better equipped to optimize their maintenance management strategies and harness the power of MP and CMMS solutions.