Top Manufacturing Inventory Management Software Reviewed
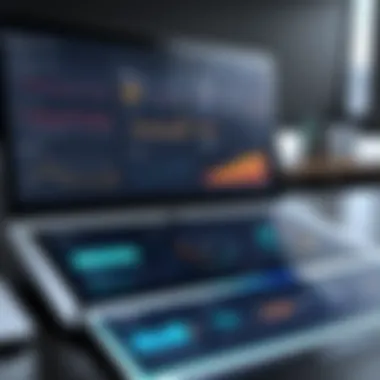
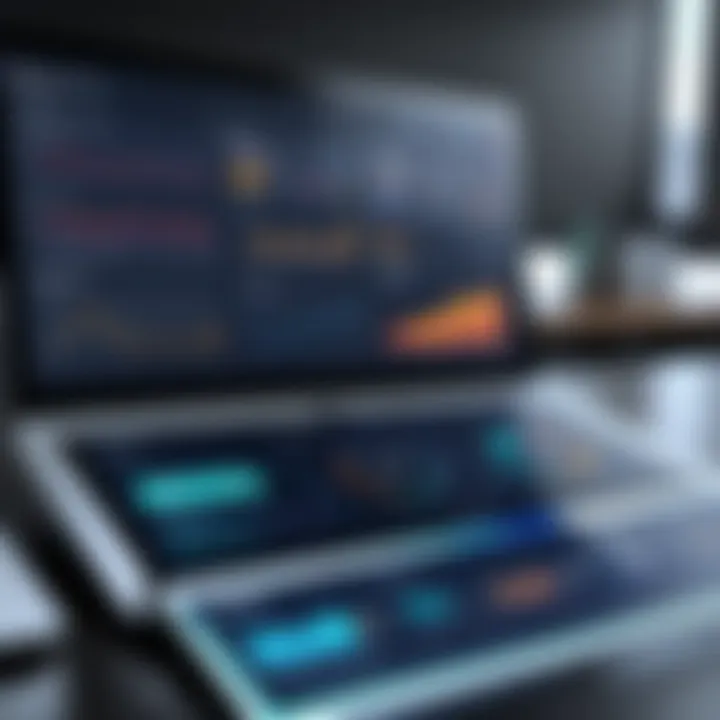
Intro
In today's competitive manufacturing environment, effective inventory management is not merely a function of tracking stock levels. Rather, it plays a critical role in operational efficiency and overall business success. Manufacturing companies face unique challenges, including fluctuating demands, supply chain disruptions, and the need for real-time data accessibility. Therefore, utilizing specialized inventory management software becomes imperative. It allows manufacturers to streamline their processes, minimize waste, and optimize resource allocation.
By integrating data-driven insights into the software evaluation process, businesses can better tackle their unique inventory challenges. This comprehensive examination is intended for tech-savvy decision-makers who are determined to leverage technology to increase their operational effectiveness.
As we delve deeper into this topic, we will explore the core functionalities that define leading inventory management software solutions, assess how they compare within the industry, and discuss user experiences that underline their effectiveness.
Foreword to Manufacturing Inventory Management Software
In the ever-evolving world of manufacturing, managing inventory is a crucial aspect that can determine the overall efficiency and productivity of operations. Manufacturing inventory management software serves as a vital tool for businesses to oversee their inventory processes effectively. The essence of such software lies not just in tracking stock levels, but in optimizing the entire supply chain. Proper management allows for timely procurement, reduces overhead costs, and enhances the ability to meet customer demands.
Definition and Importance
Manufacturing inventory management software refers to the automated systems designed to track inventory levels, manage orders, and streamline workflows within the manufacturing sector. It enables organizations to maintain accurate records of stock on hand, forecast demand, and prevent overstock situations. Its importance cannot be overstated, as it plays a significant role in sustaining business operations and ensuring customer satisfaction. Effective use of such software improves decision-making and facilitates precise inventory control, leading to enhanced service delivery and reduced wastage.
Market Overview
The market for manufacturing inventory management software is expanding rapidly. Advances in technology, including cloud computing and data analytics, have revolutionized the way businesses approach inventory management. Organizations are increasingly adopting solutions that offer integration with other enterprise systems, ensuring a seamless flow of information across departments. According to recent data, the global market for inventory management software is expected to grow significantly, driven by the rising need for efficiency and the need to adapt to the digital landscape. Manufacturers of all sizes are recognizing the value of sophisticated inventory solutions as they provide insights that aid in strategic planning and operational improvements.
According to TechCrunch, effective inventory management is not just about minimizing costs; it's also about enhancing the quality of service provided to customers, which ultimately drives business success.
Key Features of Manufacturing Inventory Management Software
In today’s competitive landscape, the right manufacturing inventory management software can significantly enhance operational capabilities. Understanding key features is imperative for organizations aiming for efficiency and effectiveness in managing their inventory. Each feature contributes to optimizing tasks, improving data management, and enabling strategic decision-making.
Real-Time Inventory Tracking
Real-time inventory tracking is a core feature. It allows organizations to monitor stock levels and movements instantaneously. This immediacy helps manufacturers reduce stockouts and overstock situations. Accurate visibility of inventory can minimize costs associated with excess production and storage. More importantly, it ensures that manufacturers can meet customer demands promptly, leading to improved satisfaction.
With tools like barcoding and RFID technology integrated into real-time tracking systems, businesses can achieve precise inventory counts. However, the software must also have user-friendly interfaces to allow for seamless updates and data retrieval. This adaptability to quickly changing environments is key.
Automated Reorder Processes
Automated reorder processes take inventory management to another level. By setting predetermined thresholds, businesses can automate the reordering of supplies before they run low. This not only saves time but also ensures a continuous production cycle. Organizations can avoid production delays that may arise due to inventory shortages, providing a reliable supply chain.
Furthermore, automation reduces human errors compared to manual tracking systems. Enhanced accuracy means fewer mistakes in orders, leading to a more streamlined procurement process. Many of the leading solutions offer flexibility in setting these thresholds, ensuring that companies can tailor their inventory processes based on actual consumption rates.
Reporting and Analytics Capabilities
Reporting and analytics capabilities are an essential aspect of inventory management software. These tools enable businesses to analyze their inventory performance over time. Utilizing metrics such as turnover rates and carrying costs can identify trends and patterns vital for strategic planning.
Decisions based on thorough analysis can lead to improved efficiency and cost savings. Real-time analytics allow for immediate adjustments to inventory practices, finding a balance between demand and supply. Organizations can also generate reports that assist in compliance with industry standards and regulations. This comprehensive ability to analyze leads to informed, data-driven decisions.
Integration with Other Systems
The ability to integrate with existing systems is another crucial feature of manufacturing inventory management software. Today’s organizational culture relies heavily on interconnected technology. A solution that works harmoniously with other tools like ERP, CRM, and accounting software fosters a more cohesive operational environment.
Such integration ensures continuity of information flow across departments. For instance, sales data from a CRM system can help inform inventory needs. This cross-referencing can facilitate optimized purchasing decisions. When selecting a software solution, businesses should assess how easily it can integrate with their existing operations to avoid dissociation and inefficiency.
Benefits of Effective Inventory Management
Effective inventory management is a cornerstone for successful manufacturing operations. It can significantly influence several aspects of business performance, leading to improved profitability and sustainability. This section dives into three primary benefits of effective inventory management: cost reduction, improved customer satisfaction, and enhanced operational efficiency. By understanding these benefits, businesses can make informed decisions about the right inventory management software.
Cost Reduction
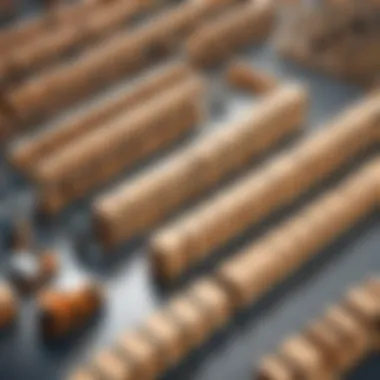
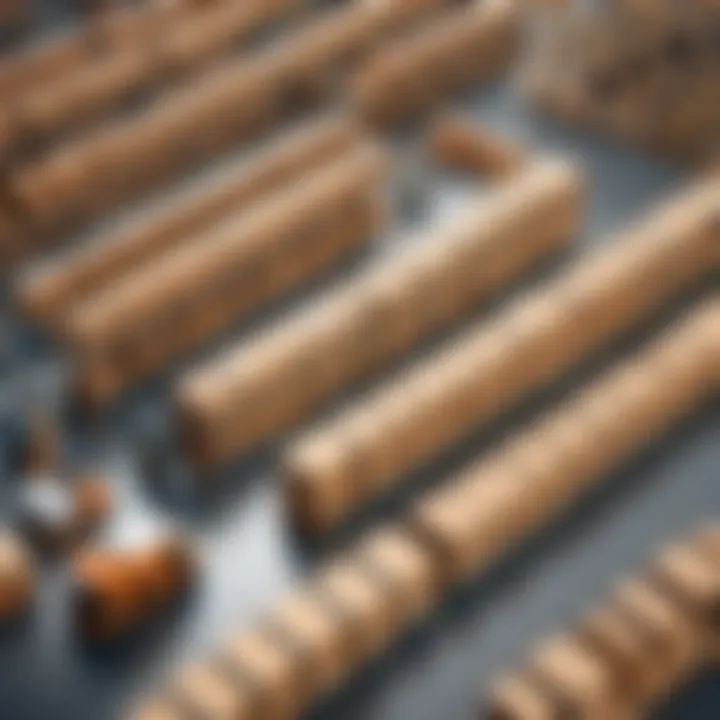
Cost reduction is often the most compelling reason for businesses to invest in inventory management software. Keeping track of inventory effectively decreases holding costs, minimizing waste from spoilage or obsolescence. Inaccurate inventory levels can lead to overstocking or stockouts, both of which incur additional costs.
- Reduced Holding Costs: By optimizing stock levels, companies can lower rent and storage fees associated with warehouse space.
- Minimized Waste: Efficient tracking can identify slow-moving items, allowing companies to adjust orders and prevent excess.
- Streamlined Supply Chain: Better planning from real-time tracking can lower costs through enhanced supplier negotiations.
Effective inventory management leads directly to improved profit margins. As businesses reduce unnecessary costs, they can allocate more resources to areas that drive growth.
Improved Customer Satisfaction
Customer satisfaction hinges heavily on a company's ability to meet demand promptly. By utilizing robust inventory management software, manufacturers can ensure that they have the right products available at the right time.
- Increased Order Fulfillment Rates: With real-time data, businesses can avoid scenarios where orders cannot be met due to stockouts.
- Timely Deliveries: Efficient inventory processes can ensure that products are readily available, leading to shorter lead times.
- Better Customer Insights: Gathered data can help companies understand customer preferences, allowing them to stock their inventory more effectively.
An increase in customer satisfaction often translates to repeat business, which is essential for sustainable growth. Happy customers are likely to return and recommend the company to others, enhancing market reputation.
Enhanced Operational Efficiency
Operational efficiency is critical for businesses to remain competitive in the fast-paced manufacturing environment. Effective inventory management software contributes significantly by automating various processes.
- Automation of Reordering Processes: Automatic alerts for low stock reduce the burden on staff.
- Tracking Capabilities: Real-time updates improve visibility across the supply chain, encouraging collaboration among teams.
- Reduced Errors: Software reduces human error compared to manual processes, increasing overall accuracy in order fulfillment.
"The right inventory management system is not just a software tool; it's a gateway to enhanced business performance."
By understanding and leveraging these advantages, companies can make strategic decisions that enhance their market position and ensure continued success.
Criteria for Selecting Inventory Management Software
Selecting the right inventory management software is a crucial step for any manufacturing organization. This decision directly impacts efficiency, productivity, and ultimately, profitability. Given the complexities of inventory processes, it is important to evaluate software solutions based on specific criteria that align with the unique needs of your operation. In this section, we will explore the essential elements of selecting inventory management software, focusing on scalability and flexibility, user-friendliness, and pricing models.
Scalability and Flexibility
Scalability refers to the software's ability to grow alongside your business. As manufacturing companies expand or shift their operations, their inventory management needs change. A scalable solution can accommodate increased product lines and greater inventory levels without substantial alterations or upgrades.
Flexibility is equally critical. This aspect allows the software to adapt to various types of products, processes, and workflows. For instance, a company that diversifies its manufacturing processes would benefit from software that can handle both assembly and production line requirements simultaneously. Being able to configure the software for specific demands fosters a smoother transition as market conditions fluctuate.
In evaluating scalability and flexibility, decision-makers should consider:
- Current and projected inventory requirements. Will the software maintain performance as volumes increase?
- Customization options. Can users tailor features to meet unique business processes?
- Integration capabilities. How easily can the software connect with existing systems?
User-Friendliness
User-friendliness is another vital criterion when selecting inventory management software. A system that is difficult to navigate leads to user frustration and mistakes, ultimately hindering your operational efficiency. The ideal software should have an intuitive interface that allows users to quickly access and manage inventory data.
Key aspects to examine include:
- Training resources. Does the software offer comprehensive support during initial implementation and beyond?
- Accessibility. Can users access the software from different devices and platforms?
- Documentation and support. Are manuals, tutorials, and customer service readily available?
A user-friendly system enhances productivity by reducing the time needed for employees to become proficient with the software.
Pricing Models
The pricing structure of inventory management software can significantly affect your overall budget. Understanding the models available—such as subscription-based or one-time purchase—allows businesses to make informed financial decisions.
When evaluating pricing models, consider the following:
- Total cost of ownership. Include implementation costs, support, and any potential upgrade fees.
- Flexibility of pricing plans. Are there options to scale pricing as your needs change?
- Comparison of features against cost. Ensure you receive value proportional to the cost spent on the software.
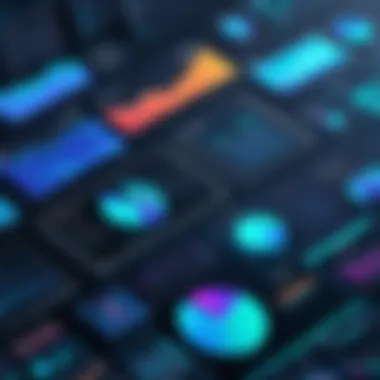
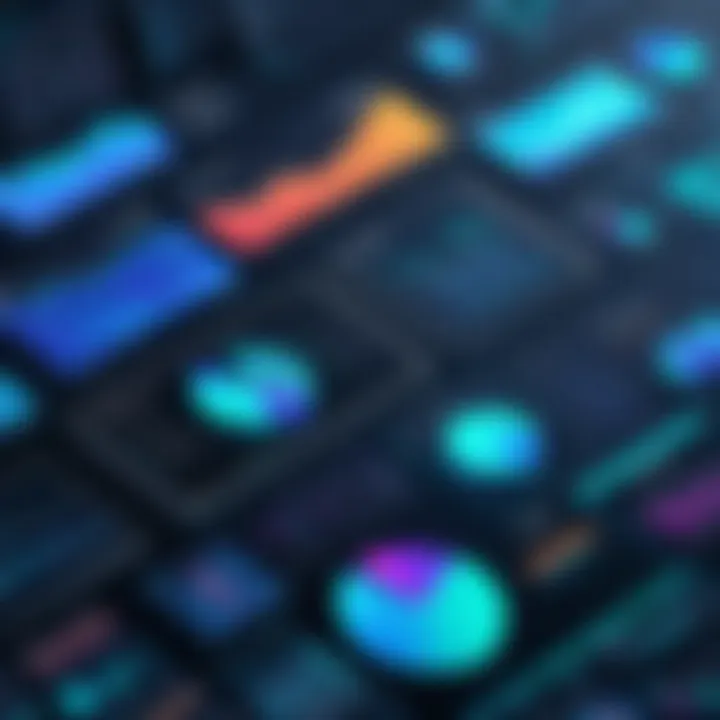
Top Manufacturing Inventory Management Solutions
In a rapidly evolving manufacturing landscape, selecting the appropriate inventory management solution holds significant repercussions for operational success. These systems facilitate crucial tasks, from tracking stock levels to managing orders and ensuring timely deliveries. Failure to choose the right solution may lead to inefficiencies, increased costs, and ultimately, diminished customer satisfaction. Therefore, understanding the leading software solutions in the market becomes essential in making well-informed decisions.
Solution Overview
The leading manufacturing inventory management solutions offer a variety of features aimed at addressing the unique challenges faced by manufacturers. Each solution has its strengths and weaknesses, but generally, they focus on key functionalities such as real-time tracking, automated reordering, and comprehensive reporting capabilities. This overview will highlight well-regarded solutions, outlining their core functionalities without bias. Software like Fishbowl, NetSuite, and TradeGecko stand out for their adaptability and industry-specific tools.
Comparative Analysis of Leading Software
A thorough comparative analysis allows decision-makers to investigate how various solutions stack up against each other. It offers insights into their features, user feedback, and pricing models, equipping businesses to select a solution that aligns with their requirements.
Feature Comparison
Evaluating the features of different inventory management software offers a glimpse into their capability to fulfill specific business needs. Many solutions, including SAP Business One, excel in real-time inventory tracking. This feature provides visibility into stock levels across multiple locations. On the other hand, systems like Zoho Inventory prioritize automated reordering processes, reducing the risk of stockouts. Importantly, a solution's ability to integrate with existing enterprise systems should not be overlooked, as this enhances operational fluidity.
User Reviews
User reviews serve as a vital source of insight when gauging the effectiveness of inventory management solutions. For instance, reviews on platforms like G2 and Capterra reveal common sentiments regarding usability and support. Users often appreciate systems that provide intuitive interfaces and responsive customer service. However, some may encounter issues related to software reliability, highlighting a potential drawback. Gathering diverse user perspectives is essential for providing a balanced view of each solution's actual performance in the field.
Pricing
Pricing models vary significantly among manufacturing inventory management systems. Solutions often offer tiered pricing based on functionality, making it crucial to assess them according to specific business needs and budgets. Take Shopify, for example; it combines eCommerce capabilities with inventory management at a competitive price point. However, hidden costs may arise that necessitate careful scrutiny during the evaluation process. The total cost of ownership should be a consideration that encompasses all aspects of the chosen software.
"Selecting the right inventory management software is not just about features; it’s about how these features align with business goals and needs."
In summary, it is essential to analyze leading manufacturing inventory management solutions. By doing so, businesses can equip themselves with the right tools to enhance efficiency while navigating complex inventory challenges.
Implementation Strategies for Inventory Management Software
Implementing inventory management software is a crucial step for manufacturing companies aiming to enhance their operational efficiency. A well-planned implementation strategy is key to ensuring the software meets the specific needs of the organization. This section will outline essential elements, benefits, and considerations involved in effectively implementing inventory management software.
Assessment of Current Inventory Practices
Before selecting new inventory software, companies must assess their current inventory practices. This assessment serves as a foundation for identifying gaps and areas for improvement. Key elements include:
- Inventory Accuracy: Evaluate how often inventory counts match actual stock levels. Discrepancies can signal problems that need addressing.
- Stock Levels: Review how well current practices manage stock levels. Are there frequent stockouts or overstock situations?
- Workflow Efficiency: Analyze the processes involved in inventory management, from ordering to returns. Streamlining these workflows is essential to improve productivity.
Identifying specific pain points helps tailor the software selection process. A detailed assessment will aid in selecting features that directly address existing issues, ensuring a better fit with company operations.
Training and Support Requirements
The successful implementation of inventory management software also relies heavily on user training and ongoing support. Companies must consider the following factors:
- User Training: Ensure that staff receive comprehensive training on how to use the new software. This training should cover operational use, troubleshooting, and how to utilize features effectively.
- Documentation: Provide easy access to written guides or video tutorials that clarify software functions. Clear documentation acts as a valuable reference post-training.
- Ongoing Support: Establish a system for ongoing technical support. This can include access to a customer service team or a dedicated internal support person. Employees should feel confident they can get help as needed.
"Effective training and support can dramatically reduce user resistance and improve adoption rates of new software."
Investing in both training and support leads to a smoother transition and minimizes disruptions in the workflow. Fostering an environment of continuous learning ensures that the software is used to its fullest potential.
Ultimately, the strategies implemented during the adoption of inventory management software significantly influence its effectiveness and usability. By thoroughly assessing current practices and investing in solid training and support, companies can realize substantial gains in efficiency and resource management.
Challenges in Inventory Management Software Adoption
Adopting new inventory management software in manufacturing can be a daunting process. The integration of such systems is crucial for enhancing operational efficiency but comes with its own set of challenges. Organizations need to be aware that successful implementation is not just about choosing the right software. It also involves navigating various hurdles that can impede the effectiveness of the system.
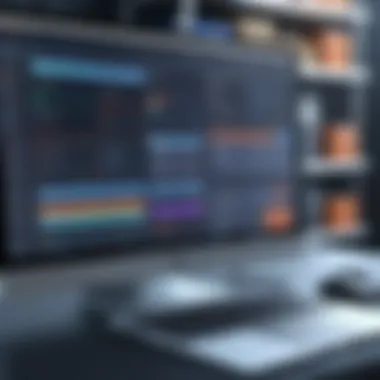
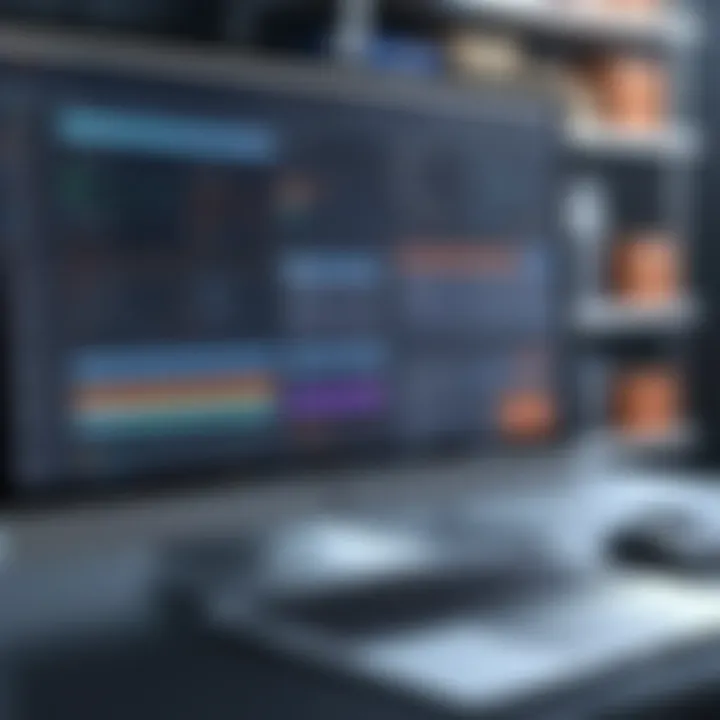
Understanding and overcoming these challenges allow companies to make informed decisions regarding their inventory management solutions. The first step is recognizing the factors that can lead to resistance from employees and complications during integration.
Overcoming Resistance to Change
One of the most significant barriers to successfully implementing inventory management software is resistance from employees. Many individuals feel comfortable with existing processes, and changing them can lead to anxiety and pushback. This resistance can stem from fear of the unknown or concerns over job security.
To minimize these feelings, companies should take a proactive approach. Thoroughly communicating the reasons behind the software adoption plays a critical role in easing fears. It is beneficial to involve the team early in the decision-making process. For instance, gathering input from those who will use the software can help them feel valued and included. When employees understand how the software can improve their workflows, their willingness to adapt increases.
Organizations should also invest in adequate training sessions. A comprehensive training program ensures that employees feel confident in using the new system. Continuous support after implementation is equally important. Providing resources, such as user manuals and responsive help desks, can address issues before they escalate into significant challenges.
Integration Issues with Existing Systems
Another notable challenge organizations face is integrating new inventory management software with existing systems. Many businesses utilize multiple software platforms for logistics, sales, and supply chain management, creating a complex network that can be hard to synchronize.
Before selecting any new software, a thorough assessment of current technologies is vital. Companies should identify compatibility issues that might arise. This helps in selecting software that can easily integrate or ensures that the necessary adaptations can be made.
During implementation, it is essential to have a well-defined strategy. Engaging IT professionals who understand both old and new systems can ease the transition. Gradual integration may also reduce system disruptions. It allows for testing and resolving issues as they occur, rather than waiting for a full roll-out.
"Proper planning and execution can transform potential integration pitfalls into smooth transitions."
Future Trends in Manufacturing Inventory Management
Understanding the future trends in manufacturing inventory management is crucial for organizations that aim to stay competitive in a rapidly evolving market. As technology advances, new tools and methodologies are emerging to enhance inventory efficiency. Organizations must look at specific elements that can lead to improved operations and better customer satisfaction. The integration of advanced technologies will help streamline processes, reduce costs, and support data-driven decision-making.
AI and Machine Learning Enhancements
Artificial Intelligence (AI) and machine learning are transforming inventory management. Their predictive capabilities allow companies to anticipate demand fluctuations and adjust inventory levels accordingly. This helps in minimizing excess stock while ensuring inventory lacks can be avoided. AI algorithms analyze historical data to identify patterns, making forecasting more accurate.
- Improved Demand Forecasting: With the integration of AI, manufacturers can predict future sales more accurately. The software analyzes customer behavior and market trends.
- Automated Processes: Machine learning can automate routine inventory tasks, freeing up staff to focus on more strategic activities.
- Reduced Human Error: Insights from AI analysis can minimize the risk of errors affecting inventory counts or order management.
"The adoption of AI in inventory management leads to better alignment of supply with demand, which is critical for operational excellence."
The Role of IoT in Inventory Management
The Internet of Things (IoT) is introducing significant changes in how manufacturers manage their inventory. Smart devices equipped with sensors can provide real-time data on stock levels, locations, and conditions of inventory items. This connectivity enables organizations to respond swiftly and effectively to changes in inventory status.
- Real-Time Insights: IoT devices provide instantaneous updates, allowing for immediate decision-making. This leads to reduced waste and timely reorder processes.
- Enhanced Asset Tracking: Companies can track inventory throughout the supply chain. Knowing where items are at all times enhances accountability and reduces loss.
- Informed Decision-Making: IoT-supported data allows for informed decisions to be made rapidly, improving overall supply chain agility.
The trends highlighted demonstrate how technology radically reshapes manufacturing inventory management. Companies investing in AI and IoT will have a significant competitive advantage, driving efficiency, sustainability, and customer satisfaction.
Closure and Recommendations
In summary, the conclusion and recommendations section plays a vital role in synthesizing the findings of this article concerning manufacturing inventory management software. This part is essential for readers to grasp the overarching insights presented and to serve as a guideline for making informed decisions moving forward. With details gathered throughout the article, it highlights key factors that can significantly influence investment choices and long-term operational success.
Summary of Key Points
The analysis conducted throughout the article identifies several pivotal points:
- Understanding Software Features: Each feature of inventory management software plays a critical role in streamlining operations, hence understanding these features is crucial.
- Implementation Challenges: The challenges organizations may face when adopting new systems should not be underestimated, as resistance to change can hinder progress.
- Future Trends: Emerging technologies, such as AI and IoT, are shaping the future of inventory management, and staying ahead is essential for competitive advantage.
- Selecting the Right Software: Proper criteria for selecting software, focusing on scalability, user-friendliness, and pricing models, ensures that organizations choose a system that aligns with their needs.
These points pull together a comprehensive narrative that serves as a roadmap for managers and decision-makers in the manufacturing sector.
Final Thoughts on Software Selection
Choosing the right manufacturing inventory management software is not a decision to make lightly. It demands thorough evaluation and understanding of both immediate needs and future aspirations. Software that might seem perfect today could quickly become a burden if it lacks flexibility or scalability.
Therefore, engaging with user reviews and exploring comparative analytics can offer forward-looking perspectives on software performance and reliability. In this ever-evolving landscape, the capacity of a system to adapt is essential.
Moreover, organizations must consider their own organizational culture and how ready their teams are to embrace changes. Facilitating proper training and a gradual implementation approach can ensure smoother transitions and enhance overall acceptance of new software.
Ultimately, every organization must weigh the long-term benefits against the costs. Taking a strategic approach to software selection not only aids in addressing current challenges but also positions firms to capitalize on future innovations effectively.