Essential Accounting Software for Manufacturers
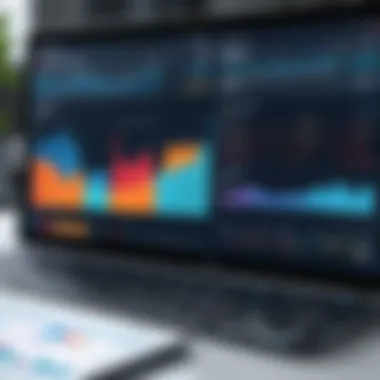
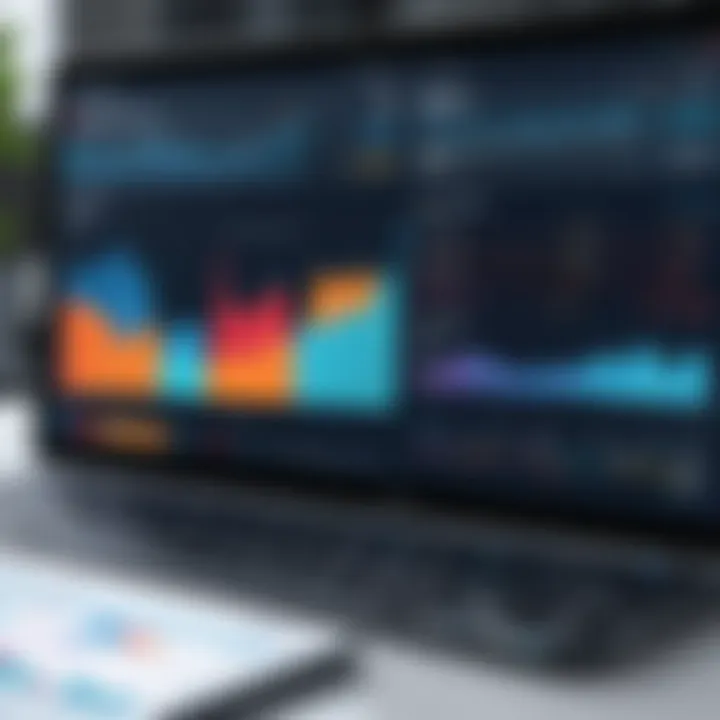
Intro
The realm of manufacturing is defined by complexity and precision. In this environment, managing financial aspects is equally challenging. Accounting software specifically designed for manufacturers addresses these unique challenges. It helps streamline processes, ensuring accurate financial data and operational efficiency. The right software solution not only supports daily accounting tasks but also enhances overall business functions. This article aims to dissect the nuances of accounting software for the manufacturing sector, guiding decision-makers in their selection process.
Software Overview
Software Category and Its Purpose
Accounting software for manufacturers is a unique category tailored to meet the needs of the industry. It encompasses tools specifically designed to handle financial management while accounting for the intricacies of manufacturing processes. Such software solutions are essential for maintaining transparency in financial reporting, managing costs, and ensuring compliance with industry regulations.
By automating financial tasks, these solutions inherently reduce the scope for human error, thereby enhancing accuracy. This is particularly crucial in manufacturing, where supply chain disruptions or mismanaged finances can have significant repercussions.
Key Features and Functionalities
The key features of accounting software for manufacturers are notable. Here are some primary functionalities:
- Inventory Management:
Tracks raw materials, work-in-progress, and finished goods. It helps in monitoring stock levels and avoiding overstocking or stockouts. - Cost Tracking:
Provides detailed insights into production costs, enabling manufacturers to analyze profitability on a per-product basis. - Regulatory Compliance:
Assists in adhering to financial regulations, ensuring the organization stays compliant. - Reporting and Analysis:
Offers extensive reporting options, providing data-driven insights for strategic decision-making. - Integration with Other Systems:
Facilitates seamless data exchange between accounting and other systems, such as ERP (Enterprise Resource Planning) tools.
These features collectively enable manufacturers not only to manage their finances effectively but to drive strategic initiatives based on real-time data.
Comparative Analysis
Comparison with Similar Software Products
When juxtaposing accounting software for manufacturers against general accounting solutions, several differences emerge. Generic software may lack specific features targeting inventory control, cost management, and manufacturing compliance. Commercial software like QuickBooks or Xero, while capable of basic accounting functions, may not provide tailored functionalities for complex manufacturing needs.
A more specialized solution, such as Sage 100cloud or NetSuite Manufacturing Edition, integrates accounting features with manufacturing management, offering a unified platform for users.
Market Positioning and User Demographics
The market for manufacturing accounting software is varied. It caters primarily to mid-sized and large enterprises that require comprehensive support for their financial operations.
Manufacturers in sectors such as automotive, food processing, and electronics often seek these specialized solutions to enhance their operational efficiency. Optimally positioned, these accounting tools serve not only to streamline finances but to provide a competitive edge in increasingly complex industries.
Foreword to Accounting Software for Manufacturers
The adoption of accounting software is increasingly recognized as essential for manufacturing firms aiming to navigate the complexities of financial management. This software serves as a backbone, providing tools that not only streamline financial operations but also enhance overall productivity.
Manufacturers often face unique challenges that traditional accounting software may not adequately address. This software is specially designed to cater to the needs of the manufacturing sector. Key functionalities include real-time inventory tracking, cost management, and detailed financial reporting, tailored to production dynamics.
The primary benefit of implementing accounting software in manufacturing is its ability to improve financial accuracy. Manufacturers can track costs at every stage of production, ensuring that they have a precise understanding of their expenses. This focus on accuracy enables more informed decision-making, directly impacting profitability.
Other significant advantages include better operational efficiencies. By automating various accounting tasks, firms can reduce manual errors and save time. This allows employees to focus on more strategic activities instead of getting bogged down with paperwork.
Organizations should carefully consider their specific needs when selecting accounting software. Factors such as scalability, customization options, and ease of use play a crucial role in ensuring the software aligns with business goals. Financial data's sensitive nature also underscores the importance of data security, making it essential for software solutions to meet regulatory requirements and industry standards.
In summary, the integration of dedicated accounting software into manufacturing processes represents a strategic move toward optimized financial management. By understanding its importance, manufacturers can leverage technology for sustained growth and operational excellence.
Importance of Accounting Software in Manufacturing
Accounting software is not just a tool; it is a critical component in the manufacturing sector. Utilizing such software helps organizations maintain precise financial records and enhances operational efficiency. By integrating various financial processes, manufacturers can gain clearer insights into their financial health. This proves vital for decision making, resource allocation, and overall strategic planning.
Enhancing Financial Accuracy
Financial accuracy is paramount for manufacturers. Traditional accounting practices can lead to discrepancies due to manual entry errors. Accounting software minimizes these risks by automating data entry and calculations. Accurate financial reporting is essential for stakeholders, regulatory authorities, and internal governance. A reliable system ensures that reports reflect actual performance, which is crucial for audits and compliance. Moreover, it enables timely tracking of costs, revenues, and profits, allowing businesses to react swiftly to financial challenges or opportunities.
Streamlining Operations
Manufacturers often face complex operations with various moving parts. Accounting software simplifies numerous processes such as invoicing, payroll, and inventory management. By having everything in one system, companies can achieve cohesion across departments. This streamlining often leads to reduced costs and enhanced productivity. Efficient management of financial data also allows for better forecasting and budgeting, which are essential in a fast-paced industry. Thus, with an effective accounting solution, manufacturers can ensure smoother daily operations, aligning financial and operational goals more closely.
Key Features of Accounting Software for Manufacturers
The landscape of manufacturing is constantly evolving, and so too are the requirements for effective financial management. Accounting software tailored for manufacturers is essential, not just for tracking finances but also for integrating with processes unique to the industry. Understanding these key features can help businesses streamline operations, improve accuracy, and maintain compliance.
Inventory Management Integration
Inventory is often one of the largest costs in manufacturing. Proper management ensures that resources are available when needed without overstocking. Accounting software helps manufacturers track stock levels, manage orders, and anticipate demand changes. For instance, systems like Fishbowl whcih work with QuickBooks can automate inventory control, providing real-time data. This integration helps in minimizing waste and enhances the overall efficiency of supply chain operations.
Moreover, having real-time visibility into inventory levels allows manufacturers to make informed decisions. Quick access to information related to raw materials and finished goods ensures smooth production schedules. Furthermore, accounting software can automate reordering processes, reducing the risk of production halts due to lack of materials. Therefore, the integration of inventory management into accounting software is not merely a feature but a fundamental requirement for success in the manufacturing sector.
Cost Tracking and Analysis
Understanding costs in manufacturing is crucial. Each stage of production has associated expenses, and tracking these accurately is vital for profitability. Accounting software can provide detailed cost analysis reports. These reports help manufacturers identify where money is being spent and where savings can be made. For example, software like Sage can help analyze costs associated with labor, materials, and overhead, enabling manufacturers to optimize their operations.
Cost tracking capabilities also allow businesses to establish accurate pricing models. This leads to better margins and improved financial forecasting. In turn, having clarity on costs helps in budgeting and financial planning. Accurate cost data feeds into strategic decision-making, providing a clear picture of what is financially viable for future projects.
Regulatory Compliance Tools
The manufacturing sector is heavily regulated, requiring compliance with various standards and laws. Accounting software is designed to assist with these compliance burdens. Tools for regulatory compliance often include built-in features that facilitate adherence to tax regulations, safety standards, and environmental practices. Systems like NetSuite provide detailed audit trails and reporting functionalities that are essential for compliance.
These tools not only ensure that manufacturers meet legal obligations but also reduce the risk of costly penalties. Non-compliance can lead to significant financial repercussions, hence the importance of selecting software that offers robust regulatory compliance features. Additionally, having accurate documentation and reporting capabilities helps in audits, allowing businesses to demonstrate compliance easily.
"Effective accounting software does not just track financials; it also empowers manufacturers to navigate the complexities of the regulatory landscape."
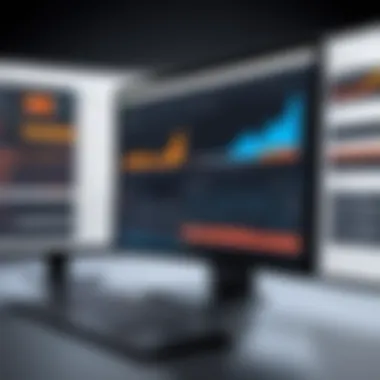
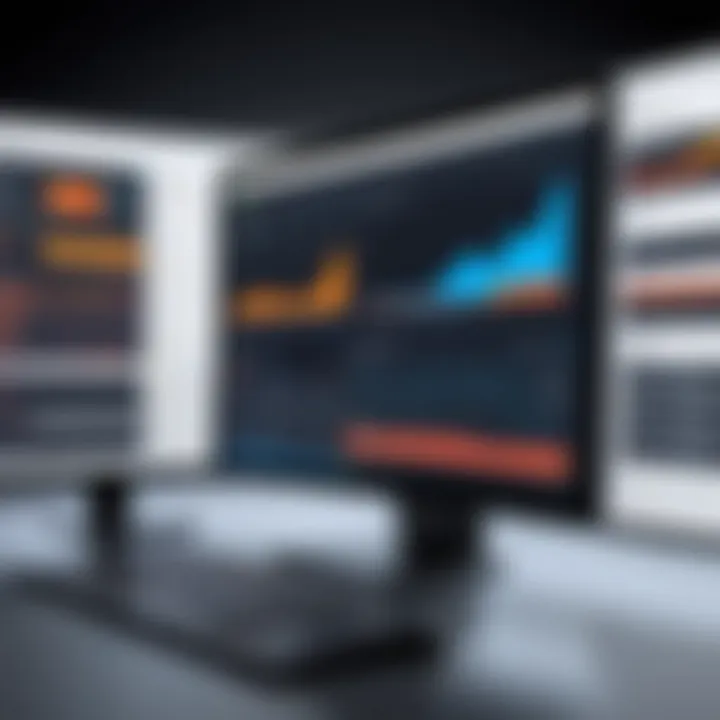
Types of Accounting Software Suitable for Manufacturers
In the fast-paced world of manufacturing, choosing the right accounting software is crucial. The type of software you select can profoundly affect not just your financial reporting but also your overall operational efficiency. Manufacturers need solutions that can handle unique processes their businesses face. This section discusses three main types of accounting software: Cloud-Based Solutions, On-Premise Software, and Hybrid Systems, providing clarity on their importance, benefits, and considerations.
Cloud-Based Solutions
Cloud-based accounting software offers manufacturers flexibility and accessibility. This type of solution enables users to access data from anywhere, supporting remote work and multi-site operations. It provides automatic updates, reducing the burden of manual upgrades and maintenance.
Benefits of Cloud-Based Solutions include:
- Reduced upfront costs due to pay-as-you-go models.
- Scalable features that grow with the company.
- Enhanced collaboration among teams through data sharing, ensuring everyone works with the most current information.
However, some manufacturers may have concerns over data security and compliance. Ensuring the provider meets industry standards is essential. The ease of integration with existing systems is another aspect worth considering.
On-Premise Software
On-premise accounting software involves installing the system directly on a companyโs hardware. This traditional approach allows for greater control over data and systems. Manufacturers who handle sensitive information may prefer this option for its potential to provide enhanced security features.
Advantages of On-Premise Software include:
- Full control over the data and infrastructure.
- Customization options tailored to specific manufacturing processes.
- No dependency on internet connectivity, ensuring access even during outages.
Yet, this type of solution often comes with higher up-front costs and significant ongoing maintenance responsibilities. Training staff on the software can pose challenges as well. Administrating updates and ensuring compatibility with newer technologies can also be a drawback.
Hybrid Systems
Hybrid systems combine benefits from both cloud-based and on-premise solutions. This flexibility allows manufacturers to store sensitive data locally while utilizing cloud features for certain functions. It caters to organizations that require a mixed approach depending on operational needs.
Key features of Hybrid Systems include:
- The ability to work with both local and remote data, maximizing efficiency based on immediate needs.
- Better disaster recovery options, leveraging cloud storage while keeping critical data secured on-premises.
- Enhanced customization, allowing manufacturers to choose the best components from both worlds to suit their unique requirements.
Choosing the right accounting software type involves assessing the specific needs of the manufacturer. Each solution offers distinct advantages, suited for various operational contexts. A deep understanding of these options can lead to informed decisions, ensuring that manufacturers adopt solutions that enhance their financial management and operational efficiency.
Factors to Consider When Selecting Accounting Software
Choosing the right accounting software can substantially influence a manufacturerโs operational success. With numerous options available, understanding critical factors becomes essential. Each element affects not just the immediate functionality but also long-term scalability and adaptation. This section will unpack vital considerations such as scalability, customization, and user-friendliness, providing clarity for decision-makers.
Scalability
Scalability refers to the software's ability to grow alongside your business. As manufacturers expand, they face increased transaction volumes and more complex operations. A scalable accounting software can handle these changes without requiring a significant overhaul. When evaluating options, consider the following:
- Future Growth: Will the software support additional users, transactions, or locations as your business grows?
- Performance Maintenance: Ensure that the software maintains performance levels despite increased workload.
- Cost Implications: Understand if scaling up adds significant costs, which can impact profit margins.
Ultimately, selecting a scalable solution ensures that your accounting processes can evolve with your business needs, preventing disruptions down the line.
Customization Options
Not all manufacturers operate in the same way. Therefore, customization is key to ensure that the software meets unique operational needs. Some critical aspects to assess include:
- Flexible Features: Does the software allow adjustments to accommodate specific manufacturing processes?
- Integration Capabilities: Can it be integrated with existing systems, such as ERP or CRM tools?
- User-defined Reports: Can you create custom reports that reflect the specific metrics that matter most to your business?
By choosing software that allows for strong customization, manufacturers can tailor functionalities to suit distinct workflows, providing a more efficient setup that aligns well with business objectives.
User-Friendliness
User-friendliness directly impacts how effectively staff can utilize the accounting software. If a system is complicated, it may lead to errors and inefficiencies. Important considerations here include:
- Intuitive Interface: The software should have a clear, logical interface that facilitates easy navigation.
- Training Support: Availability of resources for training staff, such as tutorials or customer support.
- Accessibility: Consider if the software is accessible remotely, allowing users to manage tasks from various locations.
A user-friendly solution will result in higher productivity, faster adoption rates, and reduced training time. This aspect is essential for maximizing the potential benefits of the chosen software, leading to minimal disruptions to operational flow.
In todayโs competitive manufacturing landscape, selecting the right accounting software is not merely operational but strategic. Choosing wisely can lead to enhanced efficiency and improved financial outcomes.
Integrating Accounting Software with Existing Systems
Integrating accounting software with existing systems is crucial for manufacturers aiming to streamline operations and enhance efficiency. Manufacturers often operate several systems to manage various functions such as production, supply chain, and sales. When these systems work independently, it can lead to data silos and inefficient workflows. By integrating accounting software with essential systems, manufacturers can achieve a seamless flow of information, aiding in decision-making and improving overall performance.
Integration helps in several ways. First, it minimizes data entry errors. Instead of manually inputting data from one system to another, integration ensures that information is automatically updated across systems. This accuracy is vital for financial reporting and inventory management. Secondly, it enhances real-time visibility into financial and operational metrics, allowing decision-makers to respond quickly to changing conditions.
Additionally, integrating accounting software can improve compliance with regulatory requirements. When all data is centralized, it becomes easier to audit and ensure adherence to financial guidelines. This not only saves time but also reduces risks associated with compliance issues.
ERP Integration
Enterprise Resource Planning (ERP) systems are foundational to manufacturing operations. They encompass a range of functionalities including inventory management, order processing, and human resources. Integrating accounting software with ERP systems provides a comprehensive view of an organizationโs performance.
With this integration, financial data can be linked directly to production and inventory levels. For instance, when raw materials are ordered through the ERP system, the accounting software can automatically update inventory records and adjust accounts payable. This minimizes delays and discrepancies in accounting, ensuring that financial reports reflect current operational status.
Moreover, ERP integration can facilitate better cash flow management. Manufacturers often face irregular cash flows due to project-based work or seasonal demand. By syncing the accounting software with the ERP, businesses can forecast cash requirements more accurately, paving the way for informed financial planning.
CRM Integration
Customer Relationship Management (CRM) systems handle customer interactions and sales data. When integrated with accounting software, this connection can yield significant advantages. For example, sales data from the CRM can flow directly into the accounting system, providing real-time revenue tracking. This is essential for assessing the financial impact of marketing campaigns and sales initiatives.
The integration also enables better customer service and satisfaction. When accounting software has access to customer payment histories, teams can manage collections more effectively. If a customer defaults on payment, the system can alert the sales team to adjust future terms or prioritize follow-ups accordingly.
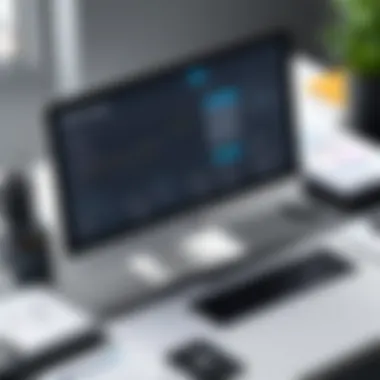
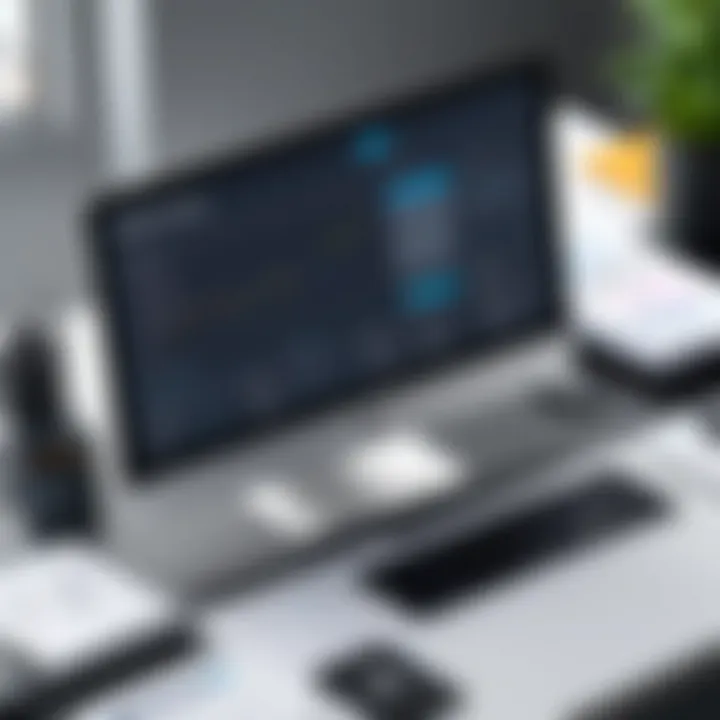
Benefits of Specialized Accounting Software for Manufacturers
The adoption of specialized accounting software brings numerous advantages to manufacturing enterprises, a sector often riddled with complexities. These tools cater to specific needs inherent to manufacturing processes, ensuring that users can manage financial operations efficiently. This section will cover key benefits such as improved decision support and enhanced reporting capabilities, which are crucial for maintaining competitiveness in an increasingly data-driven market.
Improved Decision Support
Specialized accounting software enhances decision-making processes by providing accurate and timely financial data. Unlike generic software, which may lack relevant features, tailored solutions focus on the unique aspects of manufacturing. Many systems offer real-time data analysis, allowing managers to make informed choices quickly.
Real-time data provides insight into various operational areas, including production costs, cash flow, and inventory levels. With a clear view of current financial states, manufacturers can address potential bottlenecks and seize new opportunities.
Additionally, robust forecasting tools are often integrated within specialized software. These tools use historical data to project future financial trends. By understanding what to expect in the coming quarters, manufacturers can plan budgets and allocate resources more effectively.
"In the manufacturing sector, timely information is critical. Investing in specialized software can mitigate risks and seize opportunities."
Enhanced Reporting Capabilities
Another significant benefit of specialized accounting software is its enhanced reporting capabilities. Reports generated by these systems can be customized to meet the specific needs of manufacturers, ensuring that they contain relevant data and insights.
Manufacturers can create detailed financial statements that capture information on cost variances, profit margins, and production efficiency. Such reports are essential for internal evaluations and strategic planning.
Moreover, compliance with industry standards is often a requirement. Specialized software includes compliance reporting features that streamline the process of meeting regulations. This not only saves time but also reduces the risk of errors that could lead to penalties.
In summary, the benefits of specialized accounting software for manufacturers are multifaceted. Improved decision support offers manufacturers the ability to adapt quickly to changes, while enhanced reporting capabilities provide insights necessary for long-term planning and compliance.
Challenges Faced by Manufacturers in Adopting Accounting Software
The adoption of accounting software in manufacturing, though beneficial, comes with its fair share of challenges. Understanding these challenges is crucial for manufacturers seeking to optimize their operational processes. The significance lies in knowing potential pitfalls, allowing firms to prepare accordingly and implement effective strategies to mitigate them. This section examines two primary hurdles: data migration issues and training and adoption hurdles.
Data Migration Issues
Data migration is often the first stumbling block when manufacturers decide to integrate new accounting software. Moving existing data from legacy systems to the new platform requires careful planning. A seamless transition is essential to maintain data integrity and to avoid disruptions in financial reporting.
Key aspects to consider include:
- Data Quality: Older systems might contain inaccurate or duplicate data. Manufacturers must perform extensive data cleansing before migration. Failing to do so can result in erroneous financial records or reporting mistakes.
- Compatibility: Compatibility of formats is often unaddressed. Different systems may store data differently, leading to complications during migration. Manufacturers should assess data formats and ensure the new software can accommodate them.
- Downtime: There is always a risk of downtime during migration. This can affect operations, as financial data may not be available when needed.
To alleviate these issues, manufacturers can implement a phased data migration strategy. This involves transferring smaller data sets at a time, enabling easier management and reducing the risk of data loss.
Training and Adoption Hurdles
Even after a successful data migration, challenges persist in getting staff to fully leverage the new system. Resistance to change is common in organizations. Employees may be accustomed to existing processes and hesitant to embrace new workflows.
Training is crucial. Here are some aspects to think about:
- Training Effectiveness: Training programs should not be generic. Tailoring instances and hands-on sessions for specific roles is more effective. Users must understand how to perform their jobs with the new software to maximize its potential.
- Ongoing Support: Post-training support is vital. Employees may require continual guidance as they navigate the new system. Having an internal support team or a dedicated vendor resource can help.
- Culture of Adaptation: Fostering a culture that embraces change within the organization promotes faster adoption. Management should lead by example, demonstrating the benefits of the new system and encouraging a positive outlook toward the new processes.
Market Overview of Accounting Software for Manufacturers
The significance of the market overview of accounting software for manufacturers lies in its ability to provide insights into current options, trends, and future directions. Understanding the landscape of accounting tools tailored for manufacturing can help businesses make informed choices that align with their specific operational demands. In a sector where efficiency and accuracy are paramount, having access to the right software solutions becomes critical. This section will delve into the leading software solutions available today and examine emerging trends that are shaping the industry.
Current Leading Solutions
The marketplace for accounting software specifically designed for manufacturers includes notable platforms that have garnered attention for their efficiency and features. Key players in this space include:
- Sage 300cloud: Known for extensive functionality, this software provides integrated modules for project accounting and financial management.
- NetSuite by Oracle: A cloud-based ERP that combines accounting with various other critical business functions, enhancing overall visibility and control.
- QuickBooks Manufacturing and Wholesale Edition: Popular for its user-friendly interface, it is well-suited for small to medium manufacturers looking for essential features at a reasonable cost.
- Acumatica: This cloud-based accounting software is recognized for its flexibility and scalability, catering to the dynamic needs of manufacturers.
- Microsoft Dynamics 365: Offers robust ERP capabilities that combine financial, manufacturing, and supply chain management, suitable for large enterprises.
These solutions focus on essential functions such as inventory management, cost analysis, and regulatory compliance. By leveraging these tools, many manufacturers have improved their financial accuracy and overall operational efficiency.
Emerging Trends
Several trends are emerging in accounting software for manufacturers, driven by technological advancements and market demands. These include:
- Cloud Computing: The shift towards cloud-based solutions is notable, as many manufacturers seek flexibility and real-time data access without the burden of on-premise installations.
- Artificial Intelligence (AI): Incorporating AI tools helps in predictive analytics, aiding manufacturers in forecasting future trends and optimizing operations based on data-driven insights.
- Integration Capabilities: There is a growing emphasis on the ability to integrate accounting systems with existing ERP and CRM platforms, facilitating smoother workflows and data sharing.
- User Experience Focus: Software developers are prioritizing user-friendly designs to ensure that even non-technical staff can navigate these systems efficiently and with minimal training.
- Mobile Accessibility: Manufacturers are increasingly looking for solutions that offer mobile access, allowing decision-makers to keep track of financials and key performance indicators on the go, fostering quicker decision-making.
The landscape of accounting software for manufacturers is shifting continuously. Staying informed about both leading solutions and emerging trends is essential for manufacturers to maintain a competitive edge in their operations.
By understanding these key market elements, manufacturers can better equip themselves with the right tools, ultimately enhancing their efficiency and supporting their growth in an increasingly complex environment.
Case Studies: Successful Implementation
Case studies play a pivotal role in understanding the real-world application of accounting software within the manufacturing sector. They offer valuable insights into how businesses implement these solutions, the specific challenges they face, and the benefits they achieve. Studying these examples can guide manufacturers in assessing different software options, allowing them to make informed decisions tailored to their unique operational needs.
The significance of examining successful implementations is underscored by the tangible results these case studies reveal. They serve not only to validate the capabilities of accounting software but also to highlight best practices in both software selection and deployment. Decision-makers can identify potential pitfalls and understand the requisite steps that lead to effective integration. Furthermore, these studies can inspire confidence among stakeholders, showing them that substantial operational improvements are attainable.
Example of a Medium-Sized Manufacturer
In this case study, a medium-sized manufacturing company that specializes in automotive components faced significant hurdles with outdated manual accounting processes. The inability to properly track inventory and calculate costs prompted management to explore accounting software tailored for manufacturers. The selected solution, Sage 100cloud, integrated seamlessly with their existing tools, offering advanced features such as real-time inventory tracking and automated cost analysis.
After implementation, the manufacturer reported a 30% decrease in accounting-related errors, significantly improving financial accuracy. The integration of easy-to-use dashboards enabled managers to generate reports quickly, fostering better decision-making regarding production schedules and resource allocation. Staff training was crucial in this transition. The company opted for courses directly provided by Sage, ensuring users could fully utilize the software's capabilities. In the long term, the investment in this solution not only optimized their accounting procedures but also offered a scalable platform as the business grew.
Example of a Large Enterprise
For a large enterprise, consider a multinational manufacturer of consumer electronics. This organization operated across multiple countries and faced complexities regarding compliance with varying regulations. The selected accounting software, NetSuite, provided a comprehensive solution that included multi-currency functionality and enhanced regulatory compliance tools.
The implementation process involved detailed planning and multi-department collaboration. The finance team worked closely with IT to customize the software and integrate it with the company's existing ERP system. A phased rollout allowed for testing and adjustment based on real-time user feedback. Reports indicate a remarkable 50% reduction in time spent on financial closing processes and improved accuracy in financial forecasting across global operations.
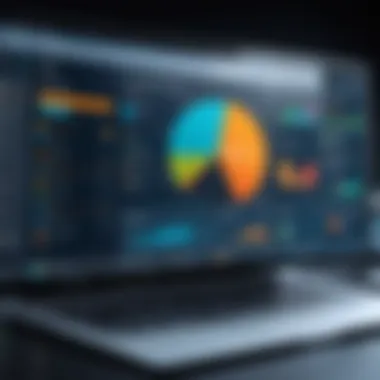
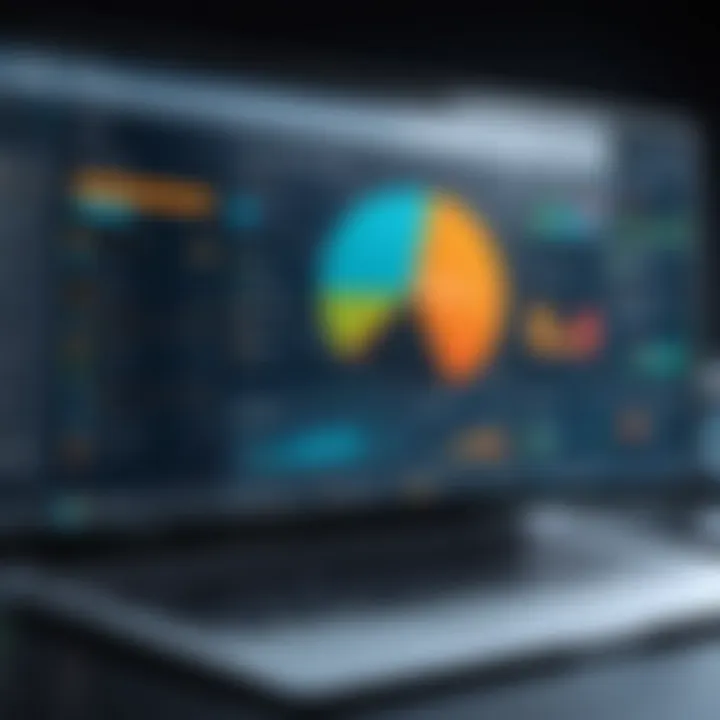
Moreover, the adoption of robust analytical tools provided by NetSuite enabled the leadership team to gain critical insights into operational costs and profitability by region. This strategic advantage allowed them to penetrate new markets more effectively while optimizing manufacturing output in existing ones.
These examples from both medium-sized and large manufacturers illustrate that successful implementation of accounting software is achievable and can lead to significant operational advancements. By assessing specific challenges and actively engaging in the selection and deployment process, manufacturers can tailor software solutions that fit their needs and drive long-term growth.
Future of Accounting Software in Manufacturing
The landscape for accounting software in manufacturing is ever-evolving. As technological advancements accelerate, manufacturers must adapt to maintain operational efficiency and financial integrity. The future of accounting software is not just limited to basic accounting functions; it encompasses advanced technologies such as artificial intelligence and data analytics. These developments promise to redefine how financial data is managed, enhancing accuracy and decision-making.
Incorporating modern features into accounting software helps industries stay competitive. Understanding the future outcomes of these technologies and their implementation is essential for manufacturers looking to streamline processes and make informed financial decisions. This not only involves direct fiscal outcomes but also considers the broader impact on production, inventory management, and compliance with regulatory standards.
Impact of Artificial Intelligence
Artificial intelligence (AI) plays a crucial role in shaping future accounting solutions. By integrating AI, manufacturers can automate various tasks, thus improving efficiency. For instance, AI can process voluminous data quickly, enabling real-time reporting and analytics. This leads to enhanced decision-making based on data-driven insights.
Manufacturers can benefit from predictive analytics, where AI analyzes historical data to forecast future trends. This capability can significantly aid in budgeting and financial planning. Furthermore, the incorporation of machine learning algorithms can enhance risk assessment, helping organizations to identify potential financial issues before they escalate.
Some potential applications of AI in accounting software include:
- Automated Invoice Processing: Reducing manual errors in data entry.
- Fraud Detection: Identifying patterns that may indicate fraudulent activities.
- Customized Reporting: Tailoring reports based on relevant metrics specific to manufacturing operations.
Forecasting Trends and Growth
The trends in accounting software indicate a movement towards greater integration with other business systems, particularly within manufacturing. The use of cloud-based platforms continues to rise, allowing for flexible access to financial data from anywhere. This is particularly relevant as remote work becomes more commonplace.
Moreover, manufacturers are investing in integrated software solutions that connect accounting with supply chain management and other operational systems. This approach provides a holistic view of business performance, making it easier to track financial outcomes in real-time.
Key trends to watch include:
- Increased Use of Automation: Streamlining data entry and reporting processes.
- Focus on Mobile Solutions: Mobile access to accounting functions enables agility and responsiveness across teams.
- Data Security Enhancements: With rising cyber threats, the demand for robust security features will grow.
Overall, the future of accounting software in manufacturing looks promising. By embracing innovations and adapting to new trends, manufacturers can significantly enhance their financial workflows and operational efficiencies.
User Perspectives: Feedback from Manufacturers
In the ever-evolving landscape of manufacturing, the insights and experiences of manufacturers regarding accounting software hold significant value. Understanding user perspectives is critical in evaluating the effectiveness of these solutions. The feedback from users often highlights practical elements that can enhance or hinder operational efficiency. This section delves into two vital aspects: Satisfaction with current solutions and Desired features and improvements.
Satisfaction with Current Solutions
Manufacturers who adopt accounting software generally express varying degrees of satisfaction. A majority appreciate the streamline efciency these solutions bring. They report improvements in financial accuracy, time savings, and simplified reporting processes. For example, many tools offer automated functions for invoicing and payroll. This automation reduces the manual effort required and minimizes errors, which is crucial in a sector where precision is paramount.
Moreover, the integration of inventory management within accounting software is a notable benefit. Many users commend systems like Sage 300 or QuickBooks Desktop for the robust tracking capabilities that complement overall business operations. This integration allows for real-time monitoring of stock levels, which ultimately aids in meeting production demands effectively.
However, there are challenges too. While some manufacturers are satisfied, others voice concerns about the responsiveness of customer support or the user interface. The learning curve associated with certain software can deter full adoption, especially for smaller businesses that may lack specialized IT personnel. Thus, feedback on satisfaction often reveals a nuanced landscape: The positive features must be weighed against potential drawbacks to make informed decisions.
Desired Features and Improvements
User feedback reveals a clear desire for enhancements in accounting software tailored to manufacturing needs. Customers frequently seek greater customization options that align software capabilities with unique business workflows. For instance, many manufacturers wish to be able to tailor reporting features to gain insights that are specific to their operations.
In addition to customization, cloud-based solutions are increasingly in demand. Users favor systems that offer remote access and collaboration capabilities. Solutions like Xero and NetSuite have been praised for their cloud features that facilitate accessibility. However, many still encounter concerns regarding data security in cloud environments.
Manufacturers also express a desire for better integration capabilities. They want seamless connections between accounting software and other operational tools, such as Enterprise Resource Planning (ERP) systems. Effective integration reduces redundancy and allows for a unified view of finances and operations, enhancing decision-making processes.
"A system that adapts to our needs and integrates easily with our existing tools is paramount for us to maintain efficiency."
Wider adoption of artificial intelligence features for predictive analytics and expense forecasting is also gaining interest. Users believe that leveraging AI can drive significant insights, resulting in better financial planning and resource allocation. Therefore, feedback underscores an essential narrative: while manufacturers appreciate current solutions, they are looking toward the future with aspirations for more adaptable, secure, and intelligent accounting systems.
This feedback loop, comprised of satisfaction levels and desired improvements, shapes the direction of product development and innovation in accounting software tailored for manufacturers. Listening to users is key to progress in this sector.
Resources for Further Learning
Understanding the complexities of accounting software for manufacturers necessitates ongoing education. As technology evolves, new features and best practices emerge. Therefore, access to reliable resources is essential for manufacturers seeking to refine their accounting processes and enhance operational efficiency. This section highlights the importance of continual learning in this domain, providing avenues for insight into tools, trends, and industry standards.
Investing time in education can yield significant benefits. For instance, understanding the nuances of accounting software can help manufacturers streamline their financial processes and resolve issues before they escalate. Furthermore, a firm grasp of compliance regulations ensures that manufacturers avoid costly penalties. Ultimately, resources for further learning equip decision-makers with the knowledge they need to make informed choices about software solutions.
Online Courses and Webinars
Online courses and webinars represent an effective method for manufacturers to gain insights into accounting software tailored to their needs. These platforms offer flexibility and convenience, suiting busy professionals who may find it difficult to attend in-person classes.
Many online learning platforms provide specific courses focusing on the features of different accounting software. Topics often include:
- Functionalities specific to manufacturing environments
- Best practices for financial reporting
- Techniques for effective data management
By engaging in these educational opportunities, manufacturers can deeply understand how to leverage accounting software for improved operational efficiency. Participants can also interact with experts in the field, fostering discussions that can illuminate practical applications of the software.
Moreover, webinars are particularly valuable as they allow live demonstrations and Q&A sessions. This direct engagement can address specific concerns and help users navigate challenges in real-time.
Industry Publications and Reports
Staying updated with industry publications and reports is essential for manufacturers. These resources provide vital information on trends and innovations in accounting software. They often encompass case studies, interviews with industry leaders, and analyses of emerging technologies.
Key benefits of leveraging industry publications include:
- Informed Decision-Making: Comprehensive reports help professionals make choices grounded in current data and insights.
- Benchmarking: Publications often feature comparisons of different accounting tools, enabling manufacturers to assess their options more effectively.
- Understanding Market Dynamics: Awareness of broader economic and technological trends can foster strategic planning.
Examples of respected sources include trade organizations, research firms, and industry journals. Regularly reviewing these materials keeps professionals well-informed and prepared for the future.
"The best way to predict the future is to create it."
- Peter Drucker
In summary, utilizing resources for further learning is crucial for manufacturers navigating the landscape of accounting software. Online courses, webinars, and industry publications offer valuable opportunities for enhancing knowledge, ultimately leading to more informed decisions.