Enhancing Efficiency with Planned Maintenance Systems
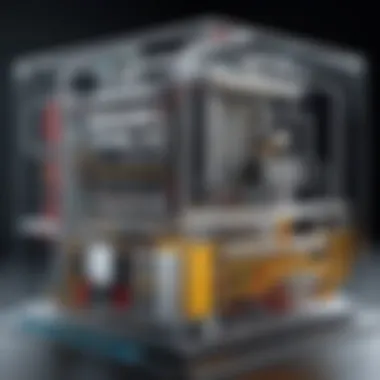
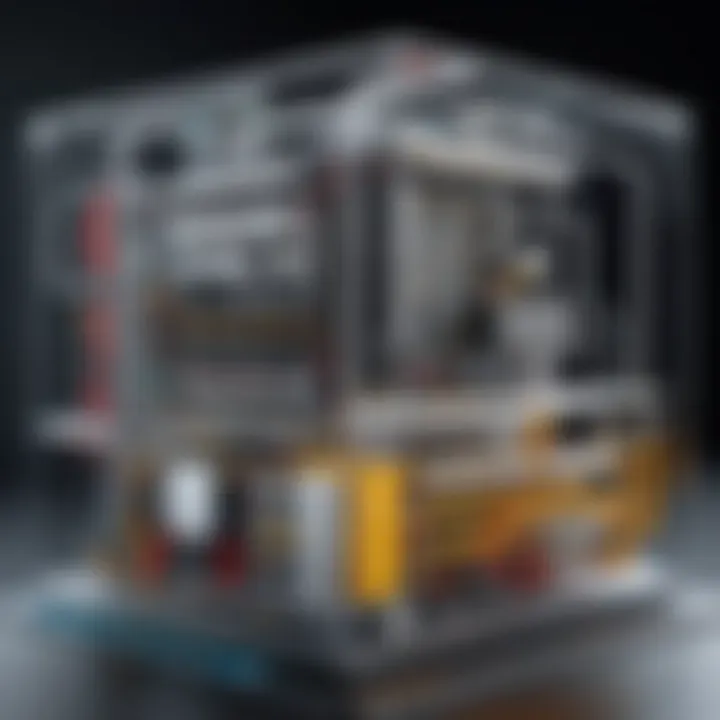
Intro
Planned maintenance systems have become an integral part of operations in various industries. They serve as frameworks designed to streamline maintenance workflows, thereby reducing downtime and enhancing productivity. For IT professionals and business owners, understanding the ins and outs of these systems is crucial. The ability to optimize maintenance processes can lead to significant operational gains. This article examines the various dimensions of planned maintenance systems, including their structure, benefits, and best practices for implementation.
Software Overview
Software Category and Its Purpose
Planned maintenance software falls under the category of Computerized Maintenance Management Systems (CMMS). The primary purpose of these systems is to facilitate regular maintenance tasks, manage assets, and track work orders. With a planned maintenance approach, organizations can prevent unexpected equipment failures, ensuring seamless operations.
Key Features and Functionalities
Planned maintenance systems come equipped with several key features that contribute to their effectiveness:
- Work Order Management: Efficient tracking and management of maintenance tasks.
- Scheduling and Planning: Automated scheduling of maintenance activities to minimize disruption.
- Asset Management: Comprehensive tracking of all assets, including their lifecycle status.
- Reporting and Analytics: Generation of reports for data-driven decision-making and continuous improvement.
These functionalities empower businesses to implement proactive maintenance strategies, ultimately saving costs and increasing overall efficiency.
Comparative Analysis
Comparison with Similar Software Products
When evaluating planned maintenance systems, it is essential to compare them with similar software products in the market. Certain well-known systems like Fiix, Hippo CMMS, and EMaint excel in various aspects, such as user interface or specific features. However, the choice often hinges on the specific needs of the organization.
Market Positioning and User Demographics
Planned maintenance systems typically cater to a wide range of industries, including manufacturing, healthcare, and utilities. The primary users are facility managers, maintenance teams, and operations managers. By focusing on these demographics, vendors position their offerings to meet unique industry requirements, enhancing user adoption and satisfaction.
"Adopting a planned maintenance strategy transforms maintenance from a reactive to a proactive approach, significantly improving operational efficiency."
As organizations continue to seek enhanced efficiencies, the adoption of effective planned maintenance systems will remain a pivotal strategy for sustainable growth.
Understanding Planned Maintenance Systems
Understanding planned maintenance systems is crucial for businesses aiming for operational efficiency. Such systems not only organize maintenance tasks but also play a significant role in extending the lifespan of assets and reducing unexpected failures. A well-structured planned maintenance system can create a culture of proactive management rather than reactive fixes, which ultimately saves time and money.
One aspect that merits attention is the integration of these systems with existing workflows. By aligning maintenance schedules with operational demands, companies can minimize disruptions. Furthermore, it empowers teams to strategize effectively, assess risks, and prioritize tasks based on urgency and importance. Hence, these systems become instrumental in facilitating smooth operations across various sectors.
Definition and Purpose
A planned maintenance system can be defined as a structured approach to managing maintenance activities with a focus on predictability and efficiency. This system encompasses scheduled inspections, preventive maintenance tasks, and planned repairs. The primary purpose is to optimize the reliability and functionality of equipment while minimizing downtime and maintenance costs.
In essence, such systems help in creating a systematic routine for maintenance, allowing companies to anticipate needs rather than respond to emergencies. By harnessing data collected from these activities, organizations can also refine strategies over time.
Historical Context of Maintenance Practices
Historically, maintenance practices varied significantly across industries. In earlier times, many organizations relied on reactive maintenance. This meant that equipment was repaired only after breakdowns occurred, often leading to prolonged downtimes.
With the onset of industrialization, the need for efficiency prompted a shift toward more structured maintenance practices. The introduction of the Total Productive Maintenance (TPM) model in the 1970s marked a turning point, encouraging companies to engage all employees in maintenance activities. As technology progressed, planned maintenance systems evolved, incorporating software solutions for better scheduling, tracking, and management.
Today, businesses are increasingly adopting advanced planned maintenance systems that integrate cutting-edge technology like predictive analytics and artificial intelligence. This historical evolution underscores the importance of adapting maintenance strategies to modern needs, ensuring that organizations remain competitive in evolving markets.
The Components of a Planned Maintenance System
To comprehend the effectiveness of a planned maintenance system, one must explore its critical components. Each element plays a significant role in creating a seamless and efficient maintenance operation. Understanding these components enables organizations to develop an integrated approach that optimizes resources and extends asset lifespans.
Asset and Inventory Management
Effective asset and inventory management is vital for a successful planned maintenance system. This component involves tracking all equipment, tools, and materials that an organization utilizes in its operations. By cataloging assets, maintenance teams can gain a clear understanding of what is available, its condition, and where it is located. Moreover, the management of inventory ensures that necessary spare parts and consumables are readily accessible when needed.
Inadequate asset management can lead to unnecessary downtime due to equipment failures or delays in repairs. When an organization knows what they have—and where to find it—they can respond more promptly to maintenance needs. For instance, implementing a centralized asset database allows for quick references and audits. Consequently, organizations can establish better procurement strategies and reduce excess inventory.
Scheduling and Planning Tools
Scheduling and planning tools are essential for orchestrating maintenance activities. The ability to effectively organize tasks transforms maintenance from a reactive to a proactive venture. This systematic approach minimizes equipment failures and extends the life of assets.
Tools that facilitate scheduling typically include work order management systems, computerized maintenance management systems (CMMS), and calendar integrations. By utilizing these tools, organizations can prioritize tasks, allocate resources efficiently, and set realistic timelines. In turn, this leads to reduced disruption in daily operations and higher equipment availability.
A well-structured schedule ensures that maintenance personnel are not overburdened while also maximizing productivity. This creates a culture of preparedness and reliability. Through proper planning, organizations can achieve a balance between routine maintenance activities and unplanned repairs.
Documentation and Compliance Tracking
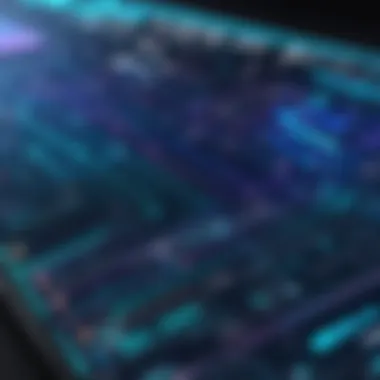
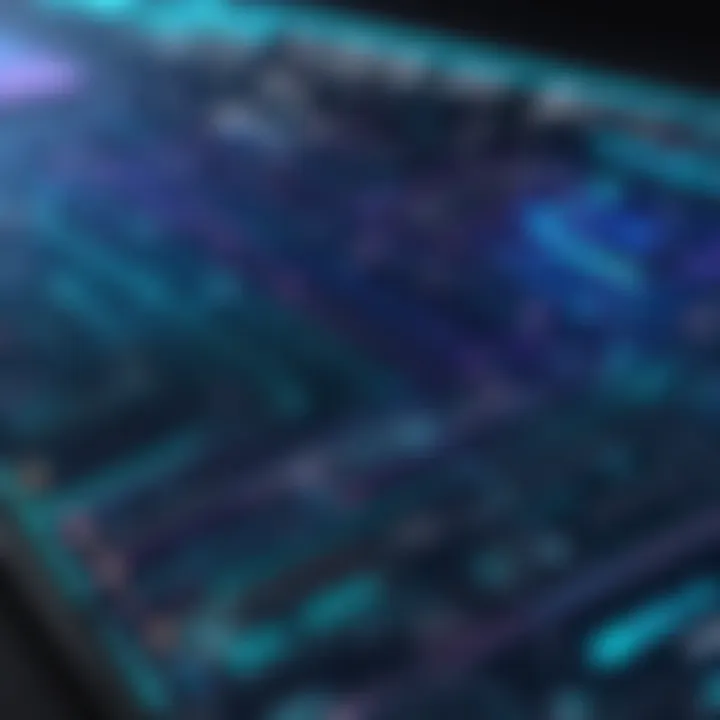
Documentation and compliance tracking are often overlooked but are fundamental in ensuring that maintenance operations meet industry standards and regulations. This component assists organizations in maintaining accurate records of all maintenance tasks, inspections, repairs, and compliance activities.
Stable documentation practices lead to increased transparency and facilitate audits. Compliance tracking is particularly important in regulated industries, such as healthcare and manufacturing, where adherence to standards is critical. Regular audits supported by thorough documentation can protect against legal liabilities and enhance reputation.
Moreover, having a detailed history of maintenance activities enables organizations to analyze performance metrics, identify trends, and make informed decisions on future maintenance strategies. This capability also supports predictive maintenance efforts, as historical data can indicate when maintenance should occur before failures happen.
In summary, the components of a planned maintenance system—asset and inventory management, scheduling and planning tools, and documentation and compliance tracking—form the backbone of an effective maintenance strategy. Collectively, they enable organizations to reduce downtime, manage resources efficiently, and maintain compliance with standards.
Benefits of Implementing a Planned Maintenance System
Understanding the benefits of implementing a planned maintenance system is vital for organizations aiming to enhance their operational efficiency. A well-structured maintenance plan is not just about fixing equipment when it breaks down. It covers a strategic approach toward maintaining assets, ensuring their optimal performance and longevity, which translates into significant organizational advantages.
Reduction in Downtime
One of the most significant benefits of a planned maintenance system is the reduction in downtime. Unscheduled equipment failures can halt operations, leading to lost productivity and revenue. When a business engages in regular maintenance activities, it can predict when an asset might fail and take proactive measures to mitigate issues.
- Predictive Maintenance: By utilizing data analytics and monitoring tools, organizations can forecast potential failures. This allows for maintenance to be scheduled during non-peak hours, minimizing impact on operations.
- Fewer Emergencies: Regular checks and maintenance practices mean fewer crises and urgent repairs. This not only reduces the stress on maintenance teams but also leads to more predictable workflows.
With less downtime, companies can ensure smoother operations, which is critical in today’s fast-paced market.
Increase in Equipment Lifespan
A planned maintenance system contributes greatly to an increase in equipment lifespan. Neglecting maintenance can lead to accelerated wear and tear, ultimately shortening the life of machinery and other assets. By adhering to a regular maintenance schedule, organizations can maintain optimal operating conditions, thereby extending the lifespan of their equipment.
- Regular Inspections: Conducting regular inspections helps in identifying minor issues before they escalate into major problems. Addressing these concerns early can save costly repairs and replacement expenses down the line.
- Improved Performance: Well-maintained equipment generally runs more efficiently. This leads to not only longer service life but also enhances overall productivity.
Through planned maintenance, businesses can exploit their assets to their fullest potential.
Cost Efficiency and Resource Allocation
Implementing a planned maintenance system can also result in significant cost savings. The costs associated with reactive maintenance can skyrocket due to emergency repairs, overtime labor, and production losses. A strategic planned maintenance approach enhances fiscal management and resource allocation.
- Budget Management: With a clear maintenance schedule, businesses can better allocate budgets, ensuring sufficient funds for necessary maintenance activities. This leads to more informed financial planning.
- Resource Optimization: Planning maintenance in advance allows workforce availability to be more efficiently utilized. Employees can be scheduled accordingly, reducing idle time while maximizing labor productivity.
Overall, the cost efficiency gained through planned maintenance helps organizations in their long-term financial strategy and sustainability.
Effective maintenance strategies not only safeguard investments but also promote a culture of operational excellence within the organization.
Challenges in Implementing Planned Maintenance Systems
Implementing a planned maintenance system can offer extensive benefits, but it is not without its challenges. Understanding these challenges is essential for businesses seeking to enhance operational efficiency. These obstacles can influence the overall success of the implementation process. By addressing these issues, organizations may better prepare themselves to reap the full benefits of a planned maintenance system.
Resistance to Change
One significant challenge is the resistance to change within an organization. Employees may feel comfortable with current workflows, making it difficult to transition to a new system. This resistance can stem from various factors, such as fear of job loss, the complexity of new processes, or lack of clear communication.
To mitigate this issue, companies should focus on effective change management strategies. This may include:
- Training programs to familiarize employees with the new system.
- Establishing clear communication channels to address concerns.
- Involving team members in the planning process to foster a sense of ownership.
Involving employees early on can create buy-in and help them understand the benefits of the new maintenance system. This proactive approach helps reduce anxiety and builds confidence in the change.
Data Management and Integration Issues
Data management and integration issues form another major hurdle. A successful planned maintenance system relies on high-quality data to drive decision-making. However, inconsistent, inaccurate, or siloed data can hinder the performance of these systems.
Organizations may face challenges regarding:
- Data capture from multiple sources.
- Ensuring data quality across platforms.
- Integrating various systems and software for seamless operation.
To overcome these obstacles, it is crucial to implement robust data governance practices. This includes establishing standards for data entry, utilizing centralized data storage, and ensuring regular audits of data accuracy. Investing in software solutions that support integration can also streamline the process, reducing the time and effort needed for data management.
Cost of Implementation
The cost of implementing a planned maintenance system often raises concerns for many organizations. Initial investments can be high, encompassing software purchases, employee training, and potential infrastructure upgrades.
However, organizations may view implementation costs through a different lens. Long-term benefits, such as reduced downtime and extended equipment lifespan, can offset these initial expenditures. It is important to consider:
- Total cost of ownership (TCO) over time.
- Potential return on investment (ROI).
- Alternatives or phased implementation strategies to minimize upfront costs.
By conducting a thorough cost-benefit analysis, decision-makers can identify the best path forward for their organization, ensuring not only a successful implementation but also financial viability.
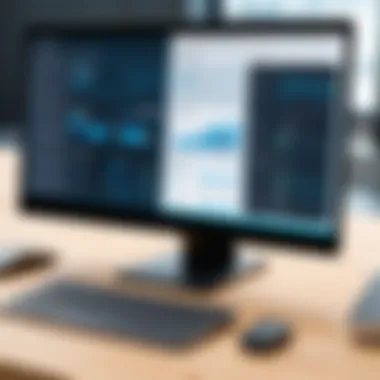
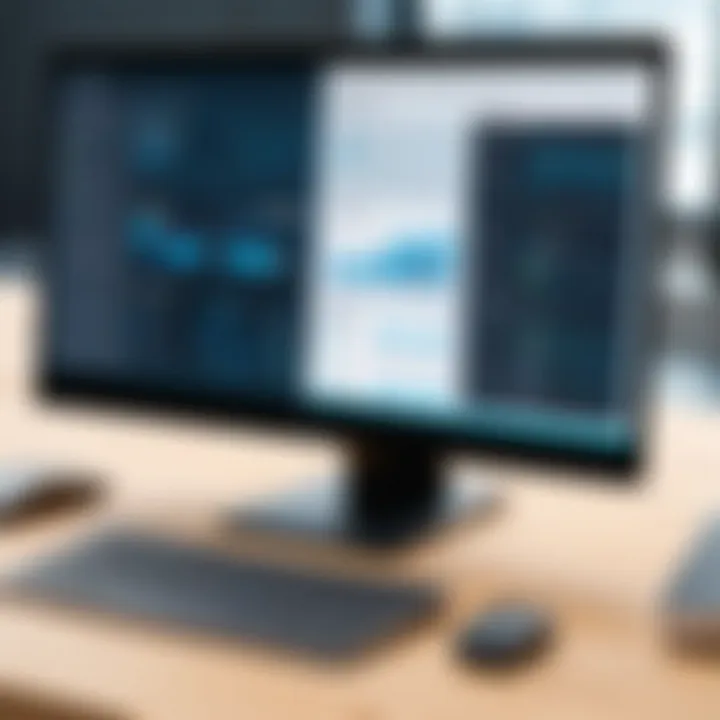
"Investing in a planned maintenance system may seem expensive, but the potential savings far outweigh the initial costs when done correctly."
Addressing these challenges effectively can pave the way for successful implementation. Organizations that recognize and plan for these issues can significantly enhance their operational efficiency and make effective use of their planned maintenance systems.
Key Metrics for Evaluating Planned Maintenance Systems
Evaluating the effectiveness of planned maintenance systems is essential for ensuring long-term operational efficiency. Key metrics provide insightful data that can guide decision-makers in optimizing maintenance strategies. By focusing on metrics, organizations can pinpoint areas of improvement, streamline processes, and enhance productivity. In this section, we look closely at three primary metrics: Mean Time Between Failures (MTBF), Maintenance Cost Ratio, and Return on Investment (ROI). Each of these metrics offers unique insights into the performance and cost-effectiveness of a maintenance system.
Mean Time Between Failures (MTBF)
Mean Time Between Failures is a crucial metric used to measure the reliability of equipment in a planned maintenance system. MTBF represents the average time elapsed between equipment failures. A higher MTBF signifies greater reliability and indicates effective maintenance practices in place.
Calculating MTBF is straightforward. The formula used is:
[
]
Understanding MTBF helps organizations evaluate the performance of their maintenance initiatives. When MTBF figures are low, it may indicate that equipment is not being maintained properly, leading to frequent breakdowns. Thus, it highlights the need for a review of maintenance schedules and practices. Improving MTBF not only minimizes downtime but also reduces repair costs, essential for driving operational efficiency.
Maintenance Cost Ratio
The Maintenance Cost Ratio is a vital indicator that helps businesses assess the cost-effectiveness of their maintenance operations. This ratio compares maintenance expenditure to the overall operational costs. A low Maintenance Cost Ratio implies efficient use of resources, whereas a high ratio may signal overspending or ineffective maintenance strategies.
To calculate this ratio, the formula is:
[
g
]
Monitoring this metric is important as it shifts focus from just the costs associated with maintenance to the operational output. Ideally, organizations should aim for a balanced ratio that reflects effective maintenance while managing costs. This understanding assists in justifying budget allocations and enhancing strategies for operational efficiency.
Return on Investment (ROI)
Return on Investment is a fundamental metric for determining the financial viability of planned maintenance systems. This metric helps organizations evaluate the monetary benefits gained from investments in maintenance against the costs incurred. A positive ROI indicates that a company is getting back more than what it spends on maintenance, which is essential for sustainable operational practices.
The calculation for ROI is:
[
g
]
In assessing ROI, organizations can make informed decisions regarding maintenance investments and resource allocations. By prioritizing high-ROI activities—like preventive maintenance—companies can enhance overall operational performance and profitability.
Understanding and implementing these metrics helps organizations steer their maintenance strategies towards achieving a balance between reliability, cost efficiency, and profitability.
Technological Advances in Planned Maintenance Systems
Technological advances have significantly transformed the landscape of planned maintenance systems. These innovations are not merely supplementary; they are essential for enhancing the efficiency and effectiveness of maintenance operations. The integration of advanced technologies provides numerous benefits. Companies can reduce unplanned downtime, improve asset management, and optimize resource allocation. In a competitive environment, leveraging such technology is critical.
Use of Predictive Analytics
Predictive analytics uses historical data to forecast future events. In the context of planned maintenance, it allows organizations to anticipate equipment failures. By analyzing patterns, companies can predict when maintenance is necessary, rather than relying on scheduled time intervals. This leads to timely interventions, minimizing the risk of unexpected outages.
Some benefits include:
- Increased Reliability: Predictive analytics improves the reliability of machinery. It helps technicians address issues before they escalate.
- Cost Savings: By preventing major breakdowns, companies can save little on emergency repairs.
- Data-Driven Decisions: With solid data, managers can make informed decisions rather than guessing.
Mobile Maintenance Solutions
Mobile maintenance solutions bring flexibility and efficiency to maintenance management. Field technicians can access vital information and update work orders in real time through mobile applications. This immediacy reduces the communication delay and enhances workplace productivity.
Consider these key advantages:
- Accessibility: Technicians can access manuals, diagrams, and past reports on-the-go.
- Quick Response Time: Immediate updates on tasks allow for faster responses to equipment issues.
- User-Friendly Interfaces: Modern mobile solutions offer intuitive interfaces, making it simple for staff to use.
The Role of Artificial Intelligence
Artificial intelligence (AI) has emerged as a game-changer in the realm of planned maintenance systems. It analyzes vast amounts of data at high speed and offers insights that would be overwhelming for human analysts. AI algorithms can recognize complex patterns and identify anomalies quicker than traditional methods.
The influence of AI includes:
- Enhanced Predictive Maintenance: AI can improve the accuracy of predictive models, making forecasts more reliable.
- Automation of Routine Tasks: AI can automate scheduling and documentation, allowing staff to focus on strategic tasks.
- Continuous Learning: AI systems adapt and improve over time, optimizing processes based on new data.
"Embracing technology is necessary for staying competitive. Companies that integrate these advances will see significant improvements in operational efficiency."
As planned maintenance systems evolve, adopting these technological innovations is crucial for companies aiming to enhance productivity and maintain a competitive edge.
Case Studies: Successful Implementation of Planned Maintenance Systems
In an era where operational efficiency is paramount for businesses, examining real-world implementations of planned maintenance systems provides valuable insights. Case studies serve as concrete examples showcasing the effectiveness of these systems across various sectors. They offer key lessons on best practices, potential challenges, and the overall impact on productivity and cost management. This section will address how organizations have benefited through the implementation of planned maintenance systems, ultimately enhancing their operational frameworks.
Manufacturing Sector Applications
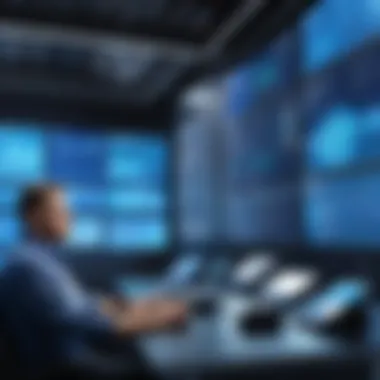
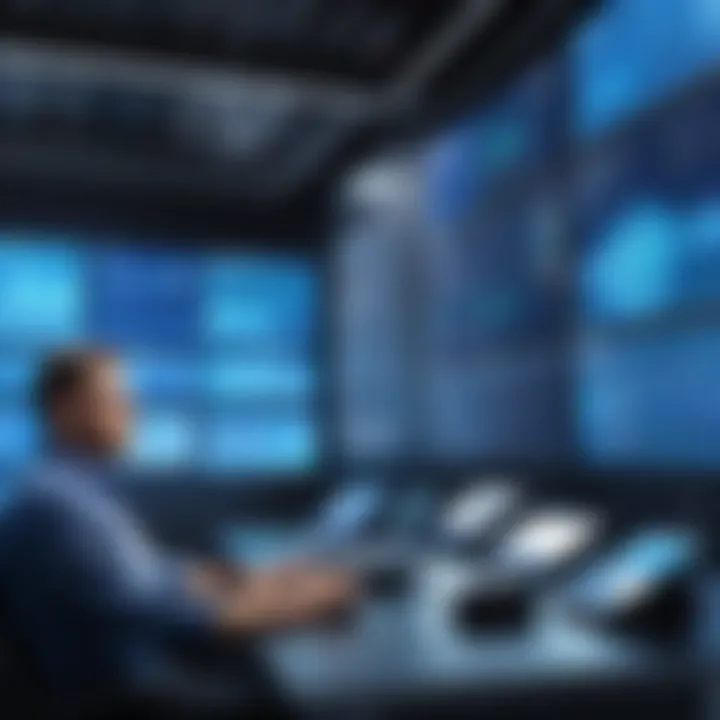
The manufacturing industry is often the first to adopt planned maintenance systems due to the critical nature of equipment uptime. Let's consider a mid-sized automotive parts manufacturer that faced frequent production halts caused by machine failures. By implementing a planned maintenance system, they established regular maintenance schedules based on machine usage and overall condition.
This approach led to significant improvements:
- Reduced Downtime: The proactive maintenance reduced unscheduled downtime by 30% within the first year.
- Increased Productivity: With reliable equipment, production levels increased, resulting in higher profit margins.
- Enhanced Data Utilization: The use of real-time data allowed operators to make informed decisions on maintenance needs, which streamlined operations.
Overall, this case exemplifies how a well-structured planned maintenance system can create a robust process that directly impacts the bottom line of manufacturers.
Facility Management and Maintenance
In facility management, maintaining various systems—from HVAC to security—is critical to ensuring safety and comfort. A case study involving a large university revealed how the adoption of planned maintenance systems transformed their operations.
Before implementing the system, maintenance requests were reactive, leading to inefficient use of resources. After adopting a planned approach, the university noticed several improvements:
- Cost Savings: Maintenance costs decreased by 20% as the need for emergency repairs diminished.
- Increased Lifespan of Equipment: By maintaining systems on a regular basis, the lifespan of HVAC units and elevators extended significantly.
- Higher Satisfaction: Stakeholder satisfaction increased due to fewer disruptions and a more reliable facility.
This case sheds light on how tailored planned maintenance systems can play a crucial role in facility management, ultimately creating a better environment for both staff and students.
Oil and Gas Industry Implementations
The oil and gas industry, often fraught with unique challenges, presents another compelling case for the implementation of planned maintenance systems. Take, for example, a major offshore drilling company that faced continuous equipment failures leading to substantial operational costs.
After implementing a rigorous planned maintenance strategy, the company noted remarkable transformations:
- Improvement in Compliance: Enhanced regulatory compliance, as maintenance logs became organized and easier to track.
- Risk Mitigation: Identifying potential equipment failures before they escalate safeguarded both personnel and assets, reducing the risk of accidents.
- Efficiency Gains: Streamlining maintenance processes allowed for a more efficient operational flow, ultimately boosting production output.
Each of these case studies illustrates that through the focused implementation of planned maintenance systems, various industries not only mitigate risks but also realize significant financial and operational benefits.
Selecting the Right Planned Maintenance Software
Selecting the right planned maintenance software is crucial for any organization that seeks to optimize its maintenance operations. It can significantly influence productivity, cost-efficiency, and overall service quality. With numerous options available in the market, the challenge lies in identifying which software best aligns with an organization’s specific needs and objectives. The right solution streamlines maintenance tasks, reduces downtime, and fosters effective resource usage while also ensuring compliance with regulatory requirements. Evaluating software effectively is the foundation for a successful planned maintenance system.
Criteria for Evaluation
When assessing maintenance software, several criteria must be considered:
- User-Friendliness: The software should be intuitive for all users in the organization. A complicated interface can lead to poor adoption and inefficiencies.
- Scalability: As businesses grow, so do their maintenance needs. Choose software that can scale to accommodate growing operations without major overhauls.
- Integration Capabilities: The ability to integrate with existing systems, such as ERP or asset management solutions, enhances data sharing and operational cohesion.
- Mobile Accessibility: Many maintenance activities occur in the field. Mobile access allows technicians to report issues and complete tasks in real time, improving response times.
- Cost: While initial costs are vital, consider long-term value and potential return on investment. Cheaper solutions may lack essential features.
- Support and Training: Examine the vendor's customer support offerings and available training resources. Ongoing support is important for troubleshooting and maximizing the software's potential.
Evaluating software against these criteria aids companies in making informed decisions that better suit their operational framework and maintenance strategies.
Top Software Solutions in the Market
The market for planned maintenance software is highly competitive, featuring several prominent solutions, each with unique offerings. Here are a few notable names:
- CMMS (Computerized Maintenance Management System): This type of software is designed specifically for maintenance management. Software examples include UpKeep, Fiix, and Maintenance Connection. Each offers various features such as work order management, predictive maintenance, and real-time reporting.
- ERP (Enterprise Resource Planning) Solutions: Solutions like SAP and Oracle often include modules for maintenance management. Although more holistic, they cater to larger organizations needing comprehensive resource management.
- Cloud-Based Solutions: Services like Gartner and Samsara provide cloud applications that facilitate remote access. Their pricing structure can benefit small to medium businesses looking for flexibility.
- Industry-Specific Software: For specialized sectors, tailored solutions such as Dude Solutions for education or Hippo CMMS for healthcare can provide necessary functionalities tailored to those environments.
Each of these platforms presents different strengths, so companies should align their selection with their operational needs, budget constraints, and future growth plans.
Future Trends in Planned Maintenance Systems
The realm of planned maintenance systems is continually evolving, driven by technological advancement and changing industry needs. Recognizing these trends is crucial for organizations aiming to enhance operational efficiency and maintain a competitive edge. Businesses must stay alert to these trends, as they offer innovative solutions that can substantially impact maintenance strategies. This section covers critical future trends, focusing on integration with the Internet of Things (IoT) and sustainable practices in maintenance.
Integration with IoT
The integration of IoT into planned maintenance systems represents a transformative shift. Many devices can now communicate and share data in real-time, which fosters greater transparency and efficiency in maintenance operations.
Using IoT technology allows for the collection of vast amounts of data on equipment performance. This data can trigger alerts for potential failures or malfunctions, enabling preventative maintenance before issues escalate. Moreover, coupling IoT with predictive analytics can refine maintenance schedules based on actual usage patterns, rather than mere assumptions or fixed schedules.
Benefits of integrating IoT include:
- Enhanced Monitoring: Continuous monitoring of asset health can lead to immediate corrective actions.
- Data-Driven Decisions: Analysis of collected data supports informed decision-making.
- Minimized Downtime: Early detection minimizes unplanned downtimes significantly.
- Improved Resource Allocation: Resources can be allocated more efficiently based on real-time needs.
As more devices become IoT-enabled, organizations can expect smarter, more proactive maintenance methodologies to become standard practice across multiple industries. This integration stands as both an opportunity and a necessity for organizations wanting to optimize their maintenance efforts.
Sustainability Practices in Maintenance
Sustainability has emerged as a vital principle in all aspects of business, and maintenance is no exception. As organizations worldwide become more environmentally conscious, the need for sustainable practices in maintenance strategies increases. This trend not only benefits the planet but also enhances operational efficiency and may even reduce costs in the long run.
Implementing sustainable maintenance practices can include several aspects:
- Energy Efficiency: Upgrading equipment to energy-efficient models can decrease resource consumption, leading to reduced operational costs and a lower carbon footprint.
- Waste Reduction: Efficient management practices aim to minimize waste, from parts and materials to hazardous substances.
- Recycling and Reusing: Finding ways to recycle components extends their life cycle, thus contributing to a circular economy.
Focus on sustainability can contribute positively to a company's brand image. Consumers and stakeholders increasingly favor organizations that prioritize environmentally friendly practices. Hence, a commitment to sustainability in maintenance practices gives businesses a competitive advantage.
"Incorporating sustainable practices not only fulfills ethical obligations but also leads to long-term economic benefits."
The trends in planned maintenance systems underline the necessity of adapting to emerging technologies and principles. Organizations that embrace IoT integration and sustainable practices will likely achieve greater operational efficiency, reduced costs, and enhanced durability of their assets.