Inventory Management Project Reports: A Complete Guide
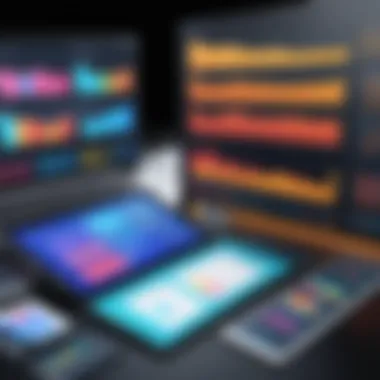
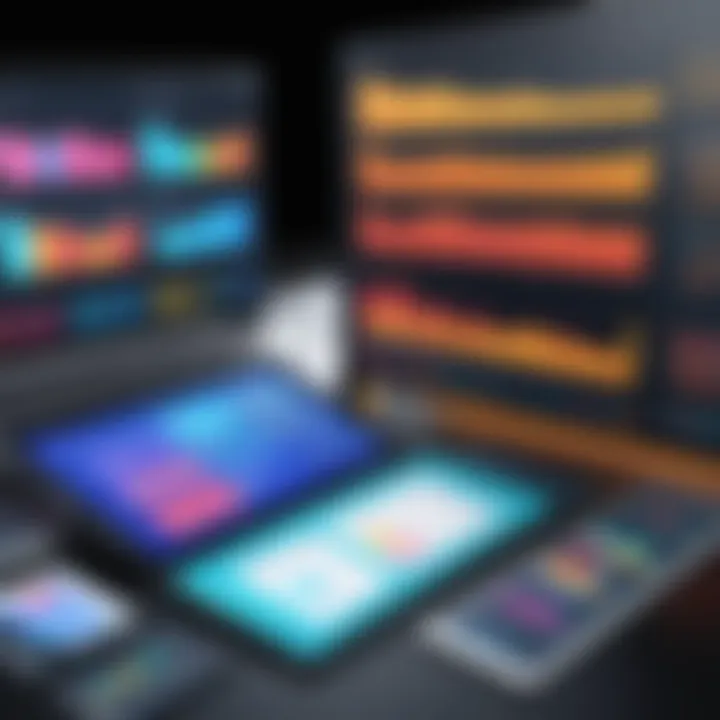
Intro
In a competitive market driven by rapid change, effective inventory management is crucial for success. Inventory management project reports play a vital role in this context, offering insights that can enhance decision-making and streamline operations. Organizations rely on these reports to assess inventory levels, analyze trends, and ensure that resources align with strategic business objectives.
This article will delve deeply into the components and methodologies associated with inventory management project reports. By understanding the significance of these reports, businesses can optimize their supply chain dynamics, leading to improved efficiency and a sustainable competitive edge. We will cover various aspects, including the software solutions that support these reports and a comparative analysis of market offerings. Our aim is to equip tech-savvy individuals, business professionals, and IT specialists with valuable insights that can inform their practices and drive better results.
Preamble to Inventory Management Project Reports
In the realm of supply chain management, inventory plays a critical role. Inventory management project reports stand at the intersection of operational efficiency and strategic decision-making. They present a structured approach to monitoring and analyzing inventory levels, which is essential for maintaining a balance between supply and demand. This section is designed to delve into the definition, purpose, and strategic significance of these reports, emphasizing their need in contemporary business practices.
Definition and Purpose
Inventory management project reports are detailed documents that provide insights into the state of inventory within an organization. They encompass critical data such as stock levels, valuation methods, and turnover rates. The primary purpose of these reports is to enable businesses to make informed decisions regarding procurement, storage, and distribution. By systematically gathering and analyzing inventory data, organizations can identify trends, optimize stock levels, and minimize carrying costs. This leads to a more agile supply chain that can respond effectively to market demands.
Importance in Business Strategy
The significance of inventory management project reports transcends mere operational tasks. They are pivotal in crafting a coherent business strategy. These reports facilitate:
- Informed Decision-Making: Accurate reports equip managers with the necessary insights to make strategic decisions regarding inventory purchases and sales strategies.
- Cost Management: By emphasizing optimal inventory levels, businesses can reduce excess stock, which ties up capital and leads to increased holding costs.
- Performance Evaluation: Regular reporting helps to establish performance metrics, allowing businesses to evaluate both their operational efficiency and the effectiveness of their inventory strategies.
- Competitive Advantage: Companies that excel in inventory management through detailed reporting can respond to customer needs faster than their competitors.
Effective inventory management is not just about tracking stock; it is about aligning inventory strategies with overall business objectives.
Key Elements of Inventory Management Reports
Understanding the key elements of inventory management reports is essential for effective decision-making and operational efficiency in any business. These reports serve as foundational tools to provide insights about inventory levels, valuations, and turnover rates. The right elements not only inform stakeholders but also guide strategies related to purchasing, production, and sales. Specific focus on inventory valuation methods, Stock Keeping Units (SKU), and lead time and reorder points can significantly shape business outcomes.
Inventory Valuation Methods
There are several methods to value inventory, and each has its own characteristics. Choosing the right one is a critical decision for any business as it affects both financial statements and tax obligations.
FIFO
FIFO stands for First-In, First-Out. This method assumes that the oldest inventory items are sold first. The primary benefit of using FIFO is that it reflects the current cost of inventory more accurately in times of inflation. This makes FIFO a popular choice in this article since it can significantly improve gross margin reporting.
Key characteristics of FIFO include its straightforward approach and the ease of tracking inventory for companies with perishable goods. However, its disadvantage is that in times of rising prices, FIFO can lead to higher taxable income due to increased profits being reported.
LIFO
LIFO, or Last-In, First-Out, assumes that the most recently acquired items are sold first. This can be a beneficial strategy for companies dealing with rapidly rising costs. In effect, LIFO allows for lower profits and, thus, lower tax liabilities during inflationary periods.
One major characteristic of LIFO is that it can create a tax advantage in certain economic conditions. However, companies must note that LIFO can lead to inventory valuation that does not reflect actual market prices, which might mislead investors or management.
Weighted Average
The Weighted Average method calculates the cost of inventory based on the average cost of products available during the period. It smooths out price fluctuations and offers a stable cost figure across varying periods. This method is beneficial in environments where inventory items are indistinguishable.
Weighted Average offers the advantage of simplicity and can work well for businesses with high transaction volumes. Yet, it lacks the precision that FIFO or LIFO might offer, particularly in times of volatile pricing.
Stock Keeping Units (SKU)
SKUs are unique identifiers assigned to products and services. They play an essential role in inventory management, helping businesses track their items accurately. Each SKU represents an individual product and its attributes, such as size, color, and type. The value of SKUs lies in their ability to facilitate easier tracking. This allows businesses to analyze sales patterns and manage inventory more effectively. Moreover, by maintaining accurate SKUs, companies can ensure better customer service, as they can readily provide information about product availability.
Lead Time and Reorder Points
Understanding lead time and reorder points is crucial for maintaining optimal inventory levels. Lead time refers to the time taken between placing an order and receiving the inventory. It is important for effective supply chain management. Companies need to account for lead times when determining when to reorder stock. Failure to do this can result in stockouts, lost sales, or excessive inventory holding costs.
Reorder points, on the other hand, are predetermined inventory levels that trigger the ordering process. This number takes into consideration demand variability and lead time to ensure that there is always sufficient stock available. Setting accurate reorder points can minimize the risk of disruptions and enhance overall inventory turnover.
Data Collection and Analysis
Data collection and analysis are essential components in the realm of inventory management project reports. Collecting accurate data is foundational for drawing meaningful insights that can drive each phase of inventory operations. Without reliable data, even the most sophisticated reporting methodologies can fail to yield valuable outcomes. This section emphasizes how strategic data collection contributes to effective analysis that aligns with business goals and enhances operational efficiency.
Sources of Data
Internal Systems
Internal systems serve as a vital source of data for inventory management. These systems include Enterprise Resource Planning (ERP), Warehouse Management Systems (WMS), and Point of Sale (POS) systems. The key characteristic of having internal systems is their ability to provide real-time information. This immediacy assists in maintaining data accuracy and ensures that decision-makers have the most current information. Internal systems are widely regarded because they can be tailored to meet an organization’s specific needs. However, one must consider that implementation can be resource-intensive, requiring both time and financial investment. In this article, internal systems are beneficial as they provide comprehensive data on stock levels, order statuses, and customer demands.
External Suppliers
External suppliers contribute crucial data that can enhance inventory reporting. They provide insights into supply chain dynamics and manage orders efficiently. The key characteristic of collaborating with external suppliers is gaining access to a wider pool of data, which includes lead times and pricing fluctuations. This aspect makes it a popular choice among businesses looking to optimize stock levels. By integrating data from suppliers, businesses can refine their inventory strategies. However, relying solely on external data can pose risks, such as inaccuracies or latency in information updates. In this article, engaging with external suppliers emphasizes the need for seamless communication and trust.
Market Research
Market research plays a significant role by offering relevant data about industry trends, customer behavior, and competitive analysis. The key characteristic of market research is its ability to provide contextual intelligence, which helps businesses understand broader market dynamics. This information is beneficial for forecasting demand and aligning inventory strategies accordingly. Unique features of market research include access to qualitative insights and quantitative data through surveys and analytics. However, the disadvantage can be the time required to conduct thorough research and interpret findings. In this article, the focus on market research highlights its importance in making informed decisions related to stock management.
Data Verification Techniques
Data verification techniques are critical to ensure the integrity and accuracy of inventory reports. Organizations can implement routine audits, cross-checking data among various sources, and utilizing validation tools to ascertain data reliability. These techniques involve a multi-step process that involves data cleansing, consistency checks, and exploratory analysis. By doing so, businesses significantly reduce the risk of errors in decision-making, therefore enhancing overall report reliability.
Analytical Tools and Software
The choice of analytical tools and software directly influences the effectiveness of inventory data analysis. Tools like Microsoft Excel, Tableau, and inventory management-specific platforms integrate advanced features. These features include forecasting, trend analyzation, and inventory simulation. Analytical tools provide the needed infrastructure for organizations to make sense of large data sets efficiently. The advantages relate to their capacity to handle complex queries and visualizations that are vital in conveying insights. A consideration for businesses is the cost and complexity of some software solutions, making user training and system integration necessary for effective deployment.
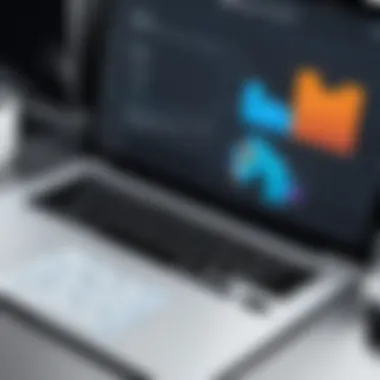
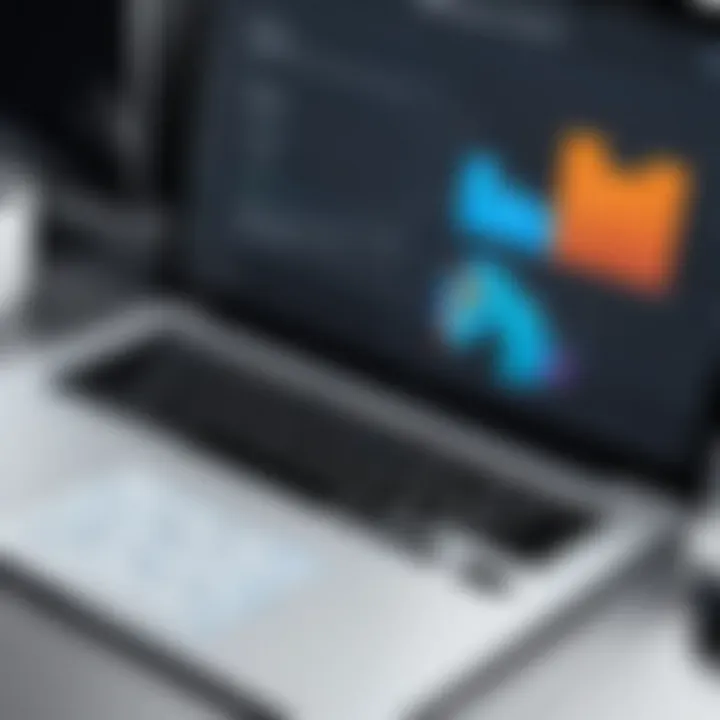
"Accurate data collection enables informed decisions, reducing the potential for costly mistakes in inventory management."
The methodologies for data collection and analysis are interconnected with every facet of inventory management. By understanding the sources of data and applying rigorous verification and analytical strategies, organizations position themselves to make sound decisions and enhance their competitive edge in the market.
Report Structure and Framework
The structure and framework of inventory management reports is crucial. It serves as the backbone of the document that communicates essential information effectively. A well-defined structure not only enhances readability but also facilitates a clear understanding of the data. It influences how stakeholders engage with the report. A logical flow ensures that vital points are highlighted and supporting evidence is presented in an orderly manner.
Key components of a report structure typically include an executive summary, inventory overview, performance metrics, and forecasting sections. Each element plays a role in driving home the importance of inventory management. It helps businesses assess their performance, identify areas for improvement, and make informed decisions based on the data presented.
Moreover, a strategic framework aligns the report with the overarching business goals. When the structure is coherent, it becomes easier to draw insights from the data. For practitioners, this can directly translate into better management practices and operational efficiencies.
A structured report is not just informative; it is an essential tool for decision-making that can impact the organization's bottom line.
Executive Summary
The executive summary is a crucial section in any inventory management report. It provides a concise overview of the entire document and summarizes key findings, conclusions, and recommendations. This section is primarily aimed at executives or stakeholders who may not have the time to read the entire report in detail. It captures the essence of the report in a few short paragraphs.
An effective executive summary should be clear and engaging. Crucially, it should highlight important metrics and trends such as overall inventory performance, significant variances compared to previous periods, and impact on cash flow. It acts as a snapshot of the information contained within the report, leading readers into a deeper understanding of the content.
Inventory Overview
The inventory overview section provides insight into the stock levels, categories, and locations. It serves as the foundation for the analysis that follows. This part describes the total inventory volume, provides an account of the various items held in stock, and highlights any deviations from expected levels.
This overview allows stakeholders to assess inventory management practices and the readiness of the supply chain. One must consider factors such as lead times, stock turnover rates, and any issues contributing to excess or deficits in stock. Overall, this section allows key personnel to gauge the effectiveness of their inventory management strategies.
Performance Metrics
Performance metrics are essential to evaluate the efficiency of inventory management practices. They offer measurable data that reveals how well inventory is managed.
Inventory Turnover Ratio
Inventory turnover ratio is a critical metric that gauges how often inventory is sold and replaced within a given period. It indicates operational efficiency. A high turnover ratio demonstrates effective inventory management, while a low ratio may suggest overstocking or weak sales.
The significance of this ratio lies in its ability to inform decision-making about purchasing and stock levels. A unique aspect is its direct impact on cash flow. By improving this ratio, companies can free up cash for other investments. However, caution is necessary to avoid stockouts that may disrupt business operations.
Gross Margin Return
Gross margin return assesses the profitability of inventory. It examines how much profit is generated from investments in inventory. A high gross margin return indicates that the inventory is effectively turning into profit and signifies good management practices. This metric is beneficial for understanding the efficiency of sales relative to inventory costs.
Its unique feature lies in its dual focus on both sales and cost management. On the downside, it can sometimes oversimplify complex inventory cost issues, which might obscure some problem areas. Hence, it is vital to couple it with other metrics for a comprehensive evaluation.
Forecasting and Projections
The forecasting and projections section predicts future inventory needs based on historical data trends, market analysis, and demand forecasting. Accurate projections are necessary for effective inventory management. This section can guide procurement strategies and ensure that stock aligns with anticipated customer demand.
Engaging in proper forecasting ensures that businesses can avoid stockouts and overstock situations. By leveraging advanced analytical tools and techniques, organizations can create more reliable inventory forecasts. Additionally, adapting to market changes becomes easier when businesses can anticipate shifts in supply needs.
Best Practices for Creating Effective Reports
Creating effective inventory management reports is crucial for any organization. These reports hold significant power in driving informed decisions and ensuring operational efficiency. When structured well, they offer insights into stock levels, help forecast demand, and identify issues that may affect the supply chain.
Clarity and Conciseness
The first best practice emphasizes the need for clarity and conciseness in reports. A well-crafted report should convey information clearly without unnecessary jargon. It is vital to ensure that every stakeholder can understand the data presented.
- Use Simple Language: Avoid complex terms when a simple alternative is available.
- Be Direct: Get straight to the point. State the findings, implications, and recommendations succinctly.
- Organize Information: Group similar information together. This helps the reader follow the flow of data without confusion.
The benefits of clarity cannot be overstated. Stakeholders, from executives to operational teams, can quickly grasp the status of inventory. This speeds up decision-making and minimizes the risk of misinterpretation.
Utilization of Visual Aids
Visual aids play a critical role in enhancing the comprehension of reports. Charts, graphs, and infographics illustrate data in a way that plain text cannot. This is important for complex data sets that require visual representation for better understanding.
- Charts: Utilize bar or pie charts to represent stock levels, turnover rates, or other metrics.
- Graphs: Line graphs can depict trends over time, helping to visualize fluctuations in inventory.
- Infographics: Create infographics for summarizing critical information.
When used properly, visual aids can significantly enhance the accessibility of reports. They enable readers to interpret data swiftly, which is especially useful in a fast-paced business environment. Moreover, they can make reports more engaging, retaining the reader's attention.
Regular Updates and Reviews
Another vital practice is the need for regular updates and reviews of inventory reports. Inventory dynamics can change rapidly, influenced by sales, market demand, or supply chain issues. By keeping reports up-to-date, organizations can maintain accuracy in decision-making.
- Set a Review Schedule: Establish weekly or monthly review cycles for reports to ensure relevance.
- Adjust to Feedback: Incorporate feedback from report users to refine data presentation and focus areas.
- Track Changes: Document any significant changes in methodology or data collection to maintain a historical record.
Regular updates foster a culture of continuous improvement. They encourage users to rely on current data for strategic decisions, thereby enhancing operational efficiency.
"Consistency in reporting fosters reliability. It’s about creating a strong foundation of trust in the data gathered."
In summary, following these best practices ensures effective inventory management reports are not only informative but also actionable. It involves clear communication, leveraging visual tools, and committing to regular updates for ongoing relevance. This structured approach is essential for organizations aiming to optimize inventory management strategies.
Challenges in Inventory Reporting
Challenges in inventory reporting are a critical aspect to consider when discussing the overall effectiveness of inventory management systems. The ability to accurately report on inventory not only influences operational efficiency but also the decision-making process within an organization. Therefore, understanding these challenges is essential for tech-savvy individuals and business professionals looking to refine their inventory strategies.
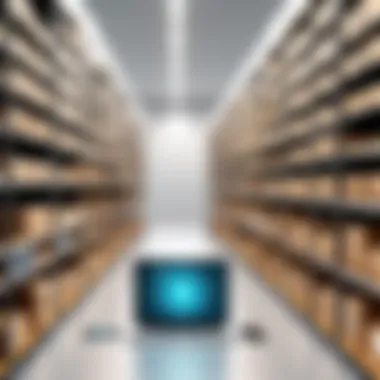
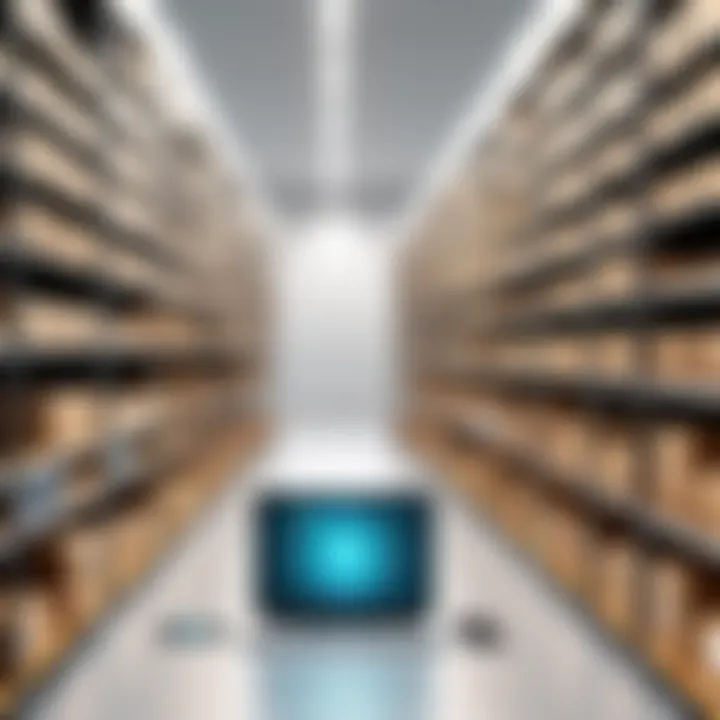
Data Accuracy Issues
Data accuracy is fundamental in inventory reporting. Inaccurate data can lead to faulty decision-making, which can have a cascading effect throughout the supply chain. For example, if an organization relies on outdated stock levels, it might either overstock or understock items, leading to increased costs and lost sales opportunities.
To combat data accuracy issues, businesses must implement robust data verification techniques. This includes frequent audits and cross-checking data from multiple sources. Automated systems that provide real-time updates can significantly reduce human error.
Additionally, having a clear method for capturing data, such as using barcodes or RFID tags, can enhance accuracy in inventory reporting.
Integration with Other Systems
The integration of inventory management systems with other operational systems is crucial for cohesive reporting. If inventory systems operate in silo, it can create discrepancies between what is reported and what is actually available. For example, a mismatch between sales data and inventory levels can render analyses misleading.
Organizations should aim to unify their inventory management solutions with accounting software and supply chain management systems. This integration facilitates smoother data flow and ensures that all departments receive consistent and accurate information. Technologies such as APIs can facilitate this integration, allowing various systems to communicate effectively.
Change Management and User Adoption
Implementing new inventory reporting systems or updates to existing systems often faces resistance from users. Change management is necessary to overcome this obstacle. Employees may be comfortable with legacy systems, making them reluctant to adapt to new reporting technologies.
To encourage user adoption, companies must invest in comprehensive training programs. Clear communication about the benefits of the new system can also alleviate concerns. Involving users in the transition process can ensure they feel respected and valued. Moreover, recognizing early adopters within the organization can promote a positive attitude towards the new system.
Successful change management can significantly mitigate challenges associated with user adoption and increase overall effectiveness in inventory reporting.
Addressing these challenges in inventory reporting not only improves the accuracy and efficiency of inventory management systems but also plays a vital role in aligning them with broader business strategies. Companies that navigate these issues successfully will see enhanced operational performance and better decision-making capabilities.
The Role of Technology in Inventory Management
Technology fundamentally reshapes inventory management practices. The integration of modern tools and systems enhances efficiency, accuracy, and visibility throughout the supply chain. As businesses face increased pressure to adapt to dynamic market conditions, leveraging technology becomes crucial. Understanding the role of technology is essential for optimizing inventory processes and improving overall business performance.
Automation and Inventory Management Systems
Automation in inventory management signifies the shift from manual processes to technologically driven solutions. With systems like SAP, Oracle NetSuite, and Fishbowl, companies can streamline operations and reduce human error. Automated algorithms can track stock levels in real time. When inventory counts reach predetermined thresholds, these systems trigger reorder notifications, thereby avoiding stockouts.
- Benefits of Automation:
- Increased Accuracy: Automation minimizes data entry errors by removing human intervention.
- Time Efficiency: Automated reports and analyses can be compiled in seconds, enabling quicker decision-making.
- Better Resource Allocation: Employees can focus on strategic tasks rather than routine inventory checks.
Investing in inventory management systems leads to measurable improvements in customer satisfaction and operational efficiency. Businesses can harness the power of automation to respond swiftly to market demands.
Blockchain for Traceability
Blockchain technology introduces a new level of transparency in inventory management. It creates a secure and immutable record of transactions, thereby enhancing traceability across the supply chain. Each product can be tracked from its origin to its final destination, reducing concerns regarding counterfeit goods.
"Blockchain can streamline processes by providing an auditable trail of products, ensuring compliance and boosting consumer trust."
- Key Advantages of Blockchain:
- Enhanced Security: The decentralized nature of blockchain fortifies data against unauthorized access.
- Greater Visibility: Stakeholders can see the complete history of a product, which aids in accountability.
- Improved Efficiency: Smart contracts can automate compliance checks and transaction approvals, expediting processes.
By utilizing blockchain for inventory management, businesses gain insights and control that were previously unattainable. As companies strive for greater transparency, adopting this technology is pivotal.
Artificial Intelligence in Demand Forecasting
Artificial Intelligence (AI) revolutionizes demand forecasting by processing large datasets at superior speeds. AI algorithms analyze historical inventory data, market trends, and even social media sentiments to predict future demand more accurately. Tools like Microsoft Azure and Google Cloud AI can facilitate this advanced forecasting.
- Advantages of AI in Demand Forecasting:
- Improved Precision: AI can identify complex patterns that traditional methods might overlook.
- Proactive Management: Companies can adjust purchasing strategies based on forecasted demand, minimizing excess inventory.
- Adaptability: AI systems can learn from new data, ensuring that forecasting models remain relevant over time.
Integrating AI into inventory management can significantly enhance responsiveness and strategic decision-making in a competitive environment. Businesses could create a robust forecasting model that aligns closely with actual market needs.
Implementing Inventory Management Strategies
Implementing inventory management strategies is critical for organizations seeking to balance supply with demand effectively. The strategies discussed here—Just-In-Time (JIT) inventory, ABC Analysis, and safety stock considerations—are vital for optimizing operations and reducing costs in inventory management. Each strategy offers unique benefits and requires careful consideration to suit the specific needs of a business, ultimately leading to enhanced efficiency and profitability.
Just-In-Time (JIT) Inventory
Just-In-Time inventory is a strategy that aims to improve efficiency by receiving goods only as they are needed in the production process. This minimizes inventory costs by reducing excess stock and storage needs. One key benefit of JIT is the reduction of holding costs, which can free up cash flow that can be redirected into other operational areas.
However, implementing JIT requires a dependable supply chain and excellent coordination with suppliers. Small delays can lead to significant disruptions, so it necessitates close relationships with suppliers and accurate demand forecasting. Companies like Toyota have famously utilized JIT, allowing them to maintain an extremely lean inventory.
Implementing JIT effectively also involves rigorous tracking systems and clear communication channels between all parties involved. Organizations must adopt an agile approach, allowing for quick adjustments as market conditions change.
ABC Analysis
ABC Analysis is a categorization technique used to prioritize inventory items based on their importance. Typically, this method divides inventory into three categories:
- A: High-value items with a low frequency of sales
- B: Moderate value items with a moderate frequency of sales
- C: Low-value items with a high frequency of sales
The primary benefit of ABC Analysis is that it allows businesses to focus their attention and resources on managing the most critical items that contribute significantly to revenue. It ensures that high-value items receive appropriate stock levels to prevent stockouts, while less crucial items can be managed with lower inventories, thus optimizing storage space.
Implementing ABC Analysis enables efficient stock replenishment processes and aids in decision-making regarding which products to emphasize, thus streamlining operations across the supply chain.
Safety Stock Considerations
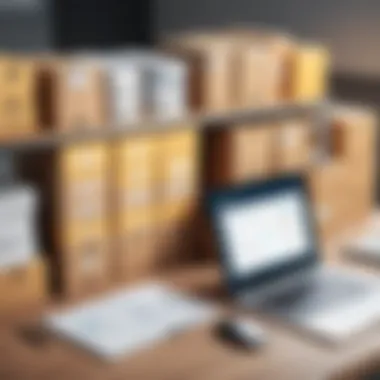
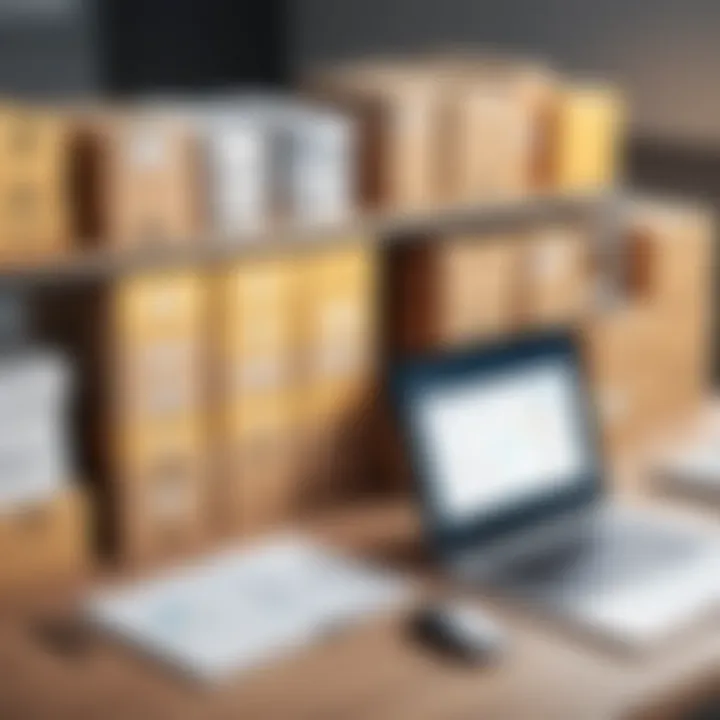
Safety stock acts as a buffer against uncertainties in demand and supply. It is the extra inventory kept on hand to prevent stockouts. Determining the correct amount of safety stock is essential as too much can lead to increased holding costs, while too little can result in missed sales and dissatisfied customers.
To calculate the appropriate level of safety stock, businesses must consider various factors, including lead time variability, service level requirements, and demand variability. Techniques such as statistical safety stock calculations can provide a more systematic approach, ensuring that the inventory aligns with business objectives and market fluctuations.
Incorporating safety stock into inventory management strategies facilitates smoother operations and enhances customer satisfaction by ensuring that products are available when needed. This ultimately contributes to a more stable revenue stream and reinforces the importance of careful planning.
Effective inventory management strategies are essential not only for maintaining operational efficiency but also for driving overall business success.
Measuring the Impact of Inventory Reports
Measuring the impact of inventory reports is crucial for businesses aiming to optimize their operations. Such reports serve as a mirror reflecting how well a company manages its inventory, which directly influences overall efficiency and profitability. Tracking the performance of inventory systems through reports not only provides insights into operational capabilities, but also identifies areas for improvement. By understanding this impact, organizations can make more informed decisions that align with their strategic objectives.
Key Performance Indicators (KPIs)
Key Performance Indicators are essential metrics that gauge the effectiveness of inventory management practices. KPIs provide quantifiable evidence of performance over time. They help define organizational success and track progress toward inventory management goals. Some common KPIs include:
- Inventory Turnover Ratio: This indicates how many times inventory is sold or used in a specific period. A higher ratio suggests efficient management, while a lower ratio may highlight overstocking issues.
- Days Sales of Inventory (DSI): This metric reflects the average number of days that inventory stays in stock before being sold. Lower DSI indicates faster sales cycles and better inventory management.
- Stockout Rate: This measures the frequency of stockouts, indicating potential sales losses due to unavailability of products.
By focusing on these and other relevant KPIs, companies can adapt their strategies, ultimately leading to enhanced performance and reduced operational costs.
Cost Savings Analysis
A thorough cost savings analysis tied to inventory reports reveals significant financial benefits. Inefficient inventory management can result in excess costs due to overstocking, wasted resources, or lost sales from stock shortages. Analyzing the financial implications allows businesses to identify:
- Carrying Costs: These include storage fees, insurance, and spoilage of goods. Reducing carrying costs represents a direct financial saving, improving the bottom line.
- Order Costs: Understanding the expenses related to placing orders can help streamline ordering processes, reducing overall operational costs.
- Loss of Revenue: By correlating inventory performance with sales, organizations can quantify potential revenue losses from inadequate inventory availability.
By regularly conducting cost savings analyses, businesses can refine their inventory strategies and enhance profitability systematically.
Customer Satisfaction Correlation
Understanding the correlation between inventory management and customer satisfaction is essential for long-term success. Well-managed inventory translates to product availability, timely deliveries, and overall customer experience. Factors to consider include:
- Product Availability: Consistent stock levels ensure that customer demands are met promptly. When customers find the products they want, satisfaction levels rise.
- Delivery Timeliness: Inventory reports can show how quickly items are dispatched. Efficient dispatches lead to higher customer satisfaction and repeat business.
- Feedback Metrics: Analysis of customer feedback related to stock issues can provide insights into how inventory practices affect customer perception and loyalty.
By measuring these aspects, organizations can adjust their inventory strategies to enhance customer satisfaction, making it a critical component of their overall business model.
Future Trends in Inventory Management Reporting
The realm of inventory management reporting continues to evolve rapidly, shaped by external pressures and advancements in technology. Understanding these future trends is vital for businesses seeking to optimize their inventory processes and maintain competitiveness. As organizations face increasing complexities in supply chain management, adapting to emerging trends will be crucial for effective decision-making and strategic alignment.
Evolving Regulatory Standards
Regulatory standards are changing continuously, driven by global market dynamics and consumer expectations. Companies must be aware of the latest compliance requirements to mitigate risks associated with inventory management. Regulatory frameworks often dictate how inventory should be recorded, valued, and reported. Failure to comply can result in severe financial penalties and reputational damage.
Moreover, evolving standards related to sustainability and environmental impact are becoming important considerations in inventory management. Companies need to integrate these regulations into their reporting frameworks. This ensures transparency and accountability regarding resource usage and waste production. Adopting practices that comply with emerging regulations can improve relationships with stakeholders and enhance brand reputation.
Integration with Big Data Technologies
The integration of Big Data technologies into inventory management offers significant advantages. Businesses can leverage vast amounts of data to gain insights into inventory patterns and demand forecasting. Utilizing Big Data analytics allows organizations to make informed decisions based on real-time information, improving accuracy in reporting.
Furthermore, businesses are beginning to implement machine learning algorithms that analyze historical data and predict future trends. This can lead to robust inventory management strategies that minimize stockouts and overstock situations.
Incorporating Big Data technologies into inventory management reporting not only improves efficiency but also enhances strategic planning. Organizations can expect to see an increase in inventory visibility and better responsiveness to market demands.
Sustainability Considerations
As sustainability takes center stage in corporate strategy, inventory management reporting must reflect environmentally responsible practices. Businesses are now evaluated on their sustainability initiatives, making it essential for inventory reports to showcase efforts toward reducing carbon footprints and waste production.
Incorporating sustainability metrics into inventory management can lead to more informed and responsible decision-making. This might include tracking the environmental impact of inventory transportation, the sourcing of materials, and the lifecycle of products. Reports should aim to highlight these aspects to attract environmentally conscious consumers and investors.
To conclude, future trends in inventory management reporting underscore the necessity for businesses to remain vigilant and adaptable. By recognizing evolving regulatory standards, integrating Big Data technologies, and focusing on sustainability, companies can navigate the complexities of inventory management more effectively. The proactive adoption of these trends will not only streamline operations but also align with broader business objectives.
Epilogue
The conclusion of an article on inventory management project reports is not merely a summary of previous sections. It serves as a vital reflection on the importance of effective reporting within inventory management as a whole. A well-structured inventory report integrates the findings from various sections and underlines the significance of accurate data, actionable insights, and strategic alignment in business operations.
Key elements in this conclusion include the recognition of inventory management as an essential component in optimizing supply chain performance. High-quality reports help identify inefficiencies, enhance decision-making, and inform future inventory strategies.
Businesses can benefit greatly from understanding the implications of these reports on their operations. The continuous flow of data into insightful reports can drive cost reductions, improve customer satisfaction, and maintain competitive advantages. Therefore, continuous improvement in reporting practices should be a priority for organizations aiming for excellence in inventory management.
Effective inventory reporting can significantly elevate a business's operational efficiency and strategic alignment.
Recap of Key Points
Summarizing the critical aspects of inventory management project reports reinforces the knowledge gained. Some key points to consider include:
- Definition and Purpose: The importance of defining inventory management and its primary objectives in business.
- Data Collection: Understanding the sources of data and the necessity of accurate data for reporting.
- Challenges and Solutions: Identifying common challenges in inventory reporting and how to overcome them through best practices.
- Technology's Impact: The evolving role of technology and how it modernizes reporting methods and enhances efficiency.
These points underscore the multifaceted nature of inventory reporting and its implications for business success.
The Continuous Improvement Journey
The notion of continuous improvement is critical in the context of inventory management. It is vital for organizations to adopt an attitude of ongoing evaluation and enhancement. This is not only about keeping pace with technological advancements but also about refining processes, data accuracy, and reporting frameworks.
Key considerations in this journey include:
- Regular Training: Educating staff on the latest practices and tools ensures effective usage of inventory management systems.
- Feedback Loops: Implementing feedback mechanisms can help in tweaking reports based on real-time business needs.
- Staying Adaptable: The market is constantly changing; hence, being adaptable in strategies can lead to better inventory management outcomes.
By actively engaging in the continuous improvement journey, businesses can significantly enhance their operational capabilities and keep their inventory management strategies competitive.