Comprehensive Guide to CMMS Maintenance Software

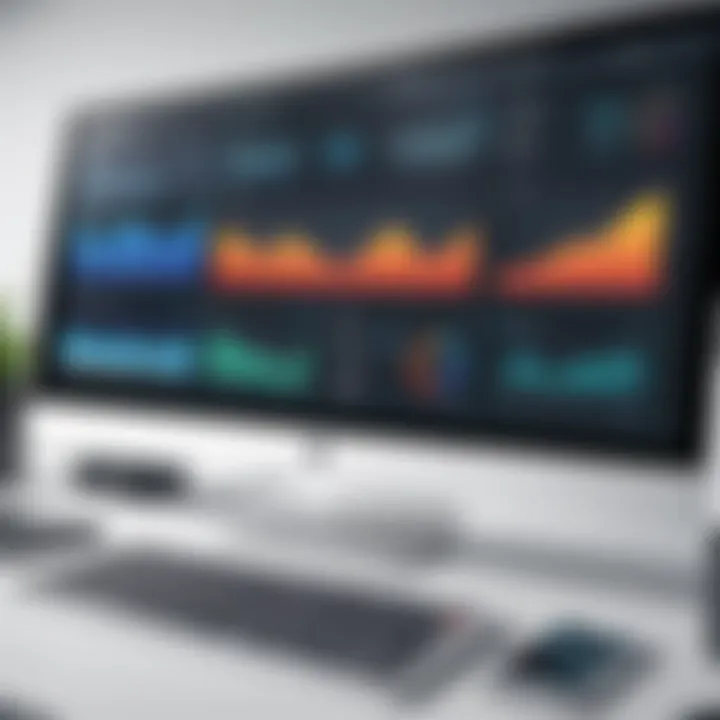
Intro
Computerized Maintenance Management Systems (CMMS) have become an essential component for modern organizations aiming to streamline their maintenance operations. These systems are tailored to help businesses manage their assets, schedule maintenance tasks, and ultimately enhance the productivity of their operations. With the growing reliance on technology, understanding the functionalities and benefits of CMMS software has never been more crucial for business owners and decision-makers.
CMMS software serves a critical purpose in maintenance management. Its primary function is to provide a centralized platform where maintenance tasks can be tracked and optimized. By utilizing CMMS, organizations can significantly reduce equipment downtime, extend the lifespan of assets, and lower operational costs. With the right software, entities can transform their maintenance strategies, converting reactive approaches into proactive practices.
In this article, we will delve into various aspects of CMMS software, including its defining features, how it compares to similar software products, and the key trends shaping the industry. By examining these topics, we aim to equip tech-savvy individuals and professionals with the insights needed to make informed decisions regarding maintenance management.
Prelude to CMMS Maintenance Software
The modern industrial landscape is characterized by rapid technological advancements and increasing operational complexities. In this context, the significance of Computerized Maintenance Management Software (CMMS) cannot be overstated. With organizations seeking to maximize efficiency and minimize downtime, CMMS becomes a vital tool for maintenance management. This section will delve into what CMMS is, why it matters, and how it fits into the broader fabric of organizational operations.
Definition of CMMS
CMMS refers to a comprehensive software tool designed specifically to aid organizations in maintaining their assets and equipment. The primary goal of CMMS is to streamline the maintenance processes, making them more efficient and effective. By employing this software, companies can manage work orders, track asset performance, and schedule maintenance activities, all from a centralized platform. In essence, CMMS is a digital backbone that facilitates proactive maintenance rather than reactive measures, thus enhancing overall productivity.
Historical Context
The evolution of CMMS has roots dating back to the late 20th century when organizations began to realize the importance of structured maintenance practices. Originally, these systems were rudimentary, often relying on paper records and manual processes. Over the years, with the advent of computing technology, CMMS underwent significant transformations. The introduction of personal computers in the workplace allowed for the digitalization of maintenance activities.
The late 1980s and 1990s marked a significant turning point, as organizations began adopting more sophisticated CMMS tools. These early systems laid the foundation for today's advanced solutions, which now incorporate features like mobile access, real-time data analytics, and integration with other business systems.
As industries continue to digitize, CMMS stands at the forefront of maintenance management modernization. This software not only reflects the advancements in technology but also aligns with organizations' shifting priorities towards operational excellence and sustainable practices.
Core Functions of CMMS Software
The core functions of CMMS software play a crucial role in optimizing maintenance operations within an organization. These functions are designed to streamline processes, enhance productivity, and ultimately contribute to better asset management. When employed effectively, CMMS software can significantly reduce downtime, prevent equipment failures, and improve the overall efficiency of maintenance teams. Understanding the core functions is essential for professionals aiming to leverage technology to their advantage.
Maintenance Planning and Scheduling
Maintenance planning and scheduling is a fundamental aspect of CMMS software. This function focuses on systematic processes to ensure that maintenance tasks are performed at the right time, thereby maximizing equipment uptime. Organizations can create preventive maintenance schedules based on various factors including equipment usage hours, manufacturer recommendations, and historical performance data. This approach results in a reduction of unplanned maintenance and extends the lifespan of assets.
The ability to visualize maintenance schedules on a calendar view can greatly assist maintenance managers in allocating resources efficiently. Additionally, maintenance planning allows for accurate forecasting of downtime and facilitates aligned staffing levels. For example, if a machine requires maintenance every 100 hours, the CMMS can notify the team ahead of time to prepare and minimize operational disruptions.
Work Order Management
Work order management is another key function of CMMS software. This feature enables technicians to receive, manage, and complete work orders efficiently. It streamlines the entire process, from creating a work request to closing out the order after completion.
Through a CMMS, managers can prioritize tasks based on urgency, assign them to specific technicians, and track progress in real-time. This systematic approach not only improves accountability among staff members but also helps ensure that maintenance tasks are completed on schedule. Furthermore, by analyzing work order history, organizations can identify recurring issues and address them proactively, further enhancing operational efficiency.
The integration of mobile access into work order management also empowers technicians in the field. They can access relevant information, update statuses, and close work orders from their mobile devices, leading to faster and more accurate results.
Inventory Management
Inventory management within a CMMS is essential for tracking spare parts and materials required for maintenance operations. Effective inventory management reduces excess stock, minimizes delays in repairs, and optimizes costs. By monitoring inventory levels and usage patterns, CMMS software helps organizations make informed decisions regarding restocking and procurement.
Moreover, having an accurate overview of inventory can prevent stockouts of critical parts, thereby ensuring that maintenance tasks are completed without unnecessary hold-ups. CMMS can also generate alerts for reorder levels, allowing teams to act proactively, rather than reactively.
Efficient inventory management fosters better relationships with suppliers, since organizations can negotiate bulk purchases based on accurate forecasting.
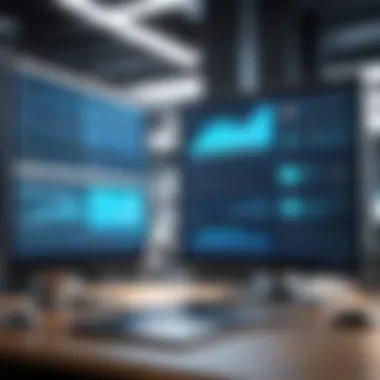
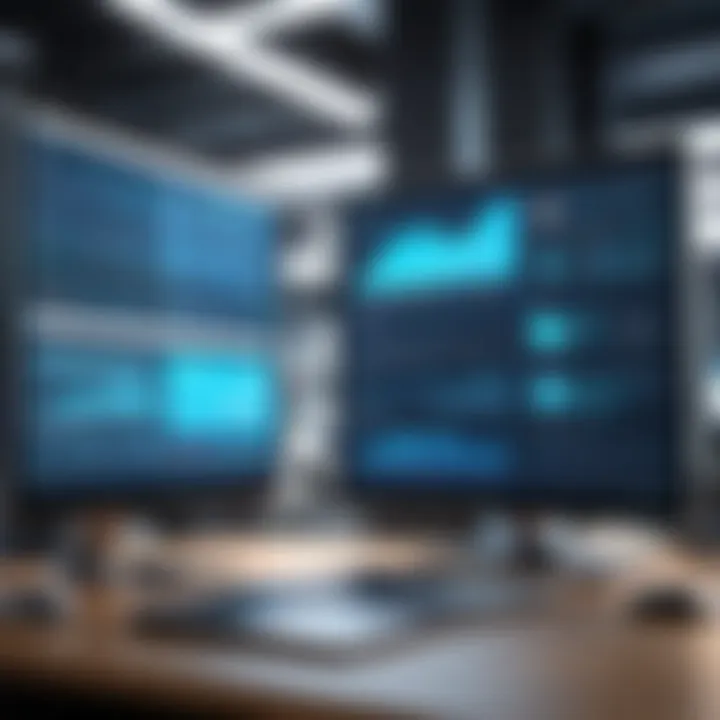
In summary, the core functions of CMMS software—maintenance planning and scheduling, work order management, and inventory management—serve as the backbone of efficient maintenance operations. By utilizing these functions thoughtfully, organizations can improve their maintenance practices, enhance productivity, and ultimately achieve significant cost savings.
Benefits of Utilizing CMMS Software
The integration of CMMS software into maintenance operations is not merely an option; it is an essential strategy for modern organizations aiming to transform their operational capabilities. By utilizing CMMS, businesses can reap considerable benefits that enhance overall productivity, reduce costs, and ensure compliance with various regulations. These advantages pave the way for minimizing downtime and extending the lifespan of assets, a critical factor in today’s fast-paced environment.
Increased Operational Efficiency
Operational efficiency is a primary outcome when organizations adopt CMMS software. This software allows for streamlined processes in maintenance planning and execution. Tasks that once required extensive manual work now become automated. For instance, scheduling regular maintenance can be done within a few clicks. This reduces the possibility of human error and ensures that no maintenance activities are overlooked. Furthermore, CMMS software equips teams with real-time data. They can access crucial information about equipment conditions, enabling proactive instead of reactive maintenance strategies.
Here are a few ways in which CMMS enhances operational efficiency:
- Automation of Tasks: Routine tasks like work order generation occur seamlessly.
- Scheduling: Users can easily set up schedules that optimize time and resource use.
- Data Accessibility: Staff can access needed data on the go, without waiting for reports or summaries.
The increased efficiency translates into higher productivity levels across departments, pushing businesses toward their objectives more effectively.
Cost Reduction
Financial savings are a significant benefit of employing CMMS software. The initial investment in CMMS might seem substantial, but the long-term savings outweigh these costs considerably. Firstly, by implementing a structured maintenance program, organizations prevent the high expenses associated with unscheduled equipment failures. This leads to reduced repair costs and avoids potential revenue losses that come with downtime.
Moreover, businesses can optimize inventory management. CMMS provides valuable insights into the usage of parts and supplies, minimizing excess or obsolete inventory. Consequently, companies can make informed decisions on purchasing, further reducing unnecessary expenditures.
In summary, CMMS contributes to cost reduction by:
- Decreasing Downtime: Preventive maintenance leads to fewer unplanned outages.
- Optimizing Inventory: Better management of stock levels prevents over-purchasing.
- Reducing Labor Costs: Automation and efficiency reduce the amount of labor needed for maintenance tasks.
Regulatory Compliance
In an increasingly regulated landscape, compliance becomes a critical issue for many industries. CMMS software assists companies in adhering to regulatory standards effectively. By maintaining accurate records of maintenance activities, businesses can demonstrate compliance during inspections or audits.
The software also helps document procedures and policies related to maintenance protocols. This feature ensures that the organization follows the best practices and statutory requirements in its operations. Incorporating CMMS solutions can significantly lower the risk of compliance-related penalties, contributing to a safer and more accountable business environment.
Key benefits in terms of compliance include:
- Documented Maintenance Records: Easy retrieval of past maintenance data helps during audits.
- Task Documentation: Clear records ensure that standard operating procedures are followed.
- Improved Safety: Regular checks promote safe operating conditions, reducing liability risks.
Key Features of CMMS Software
CMMS software serves as a crucial tool for automating and improving maintenance processes in various organizations. Understanding its key features can help businesses optimize their investment and leverage technology effectively for maintenance management. Specific functionalities of CMMS software enhance usability, accessibility, and data management, empowering users to streamline tasks and achieve better operational efficiency.
User-Friendly Interface
A user-friendly interface is an essential feature of CMMS software. It directly impacts how users interact with the system. When software is intuitive, it requires less training, making it easier for employees to understand and use. This is particularly vital in environments where employees have varying levels of technical expertise.
Key elements of a user-friendly interface include well-organized menus, clear navigation tools, and customizable dashboards. These attributes allow users to quickly access relevant information. A visually appealing interface can also reduce fatigue from prolonged use, which is a common issue with complex software systems. As a result, organizations can enhance productivity and minimize errors by ensuring that users spend less time learning the system.
Mobile Accessibility
Today’s workforce is becoming increasingly mobile, and CMMS software needs to reflect this trend. Mobile accessibility enables users to manage maintenance tasks while on-the-go. This feature facilitates real-time communication and data entry, which is essential for remote teams or personnel working in the field.
With mobile access, maintenance technicians can receive updates, check work orders, and enter data right from their smartphones or tablets. This streamlines workflows and improves response times to maintenance issues. This accessibility is especially critical in industries such as manufacturing or facility management, where immediate action can significantly reduce downtime and increase asset availability.
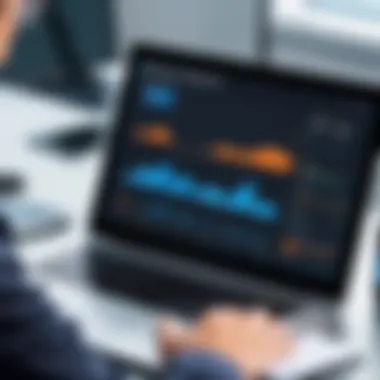
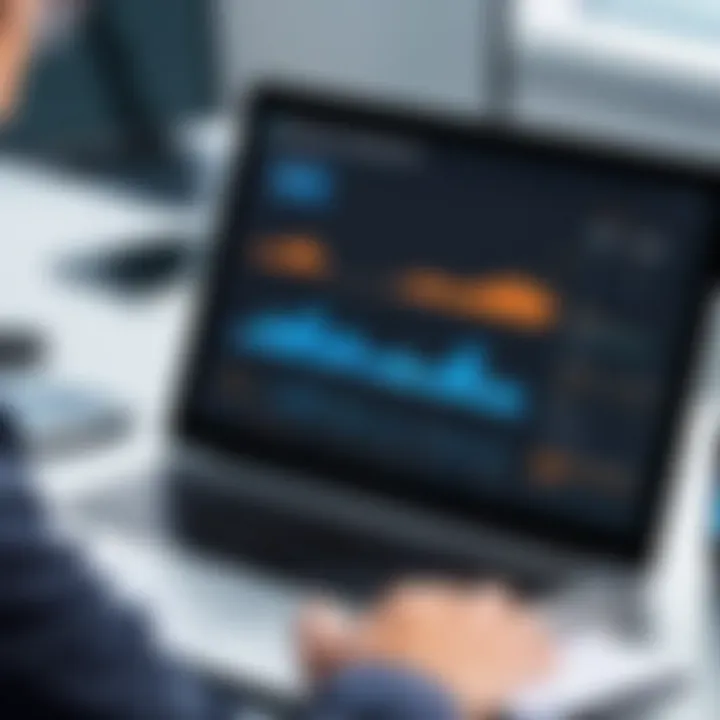
Reporting and Analytics Tools
Reporting and analytics tools within CMMS software provide insights that organizations can leverage to make informed decisions. These features allow users to track maintenance activities, analyze performance metrics, and generate detailed reports. Organizations can identify trends over time, such as equipment failures or maintenance costs, which helps in recognizing areas for improvement.
Effective reporting capabilities can also support compliance and regulatory requirements, ensuring that all necessary documentation is kept up to date. By harnessing the power of data analytics, organizations can enhance their overall maintenance strategy, optimize resource allocation, and ultimately achieve long-term sustainability in operations.
"Informed decision-making is essential for modern maintenance management. Effective reporting tools within CMMS systems provide the data necessary for strategic planning and operational excellence."
Understanding these features will help organizations choose the right CMMS solution and maximize its benefits. By focusing on usability, mobility, and data insights, companies can significantly improve their maintenance practices.
Challenges in Implementing CMMS Software
Implementing CMMS software is a strategic move for any organization aiming to enhance its maintenance operations. However, various challenges can arise during this process, making careful consideration essential. Businesses can benefit greatly by understanding these obstacles and developing strategies to manage them effectively. The primary challenges include resistance to change, data migration issues, and integration with existing systems.
Resistance to Change
Human behavior plays a significant role in the success of any software implementation. Many employees may feel apprehensive about adopting new technology, fearing that it will disrupt their familiar workflows. This resistance often stems from uncertainty about the effects of CMMS on daily tasks. Overcoming this challenge requires clear communication about the advantages of using the software. Providing training sessions can improve confidence and ease the transition.
It is important for leadership to illustrate the positive impacts of CMMS, such as increased productivity and less downtime. Engaging employees early in the process for feedback and input can also foster a sense of ownership and reduce resistance. Organizations that prioritize change management strategies tend to experience smoother implementation processes.
Data Migration Issues
Data migration is another critical hurdle. Businesses must transfer existing maintenance data into the new CMMS, which can be complex and time-consuming. Inaccurate or incomplete data can result in significant complications post-implementation. Therefore, it is vital to plan this step meticulously.
Before migration, organizations should conduct thorough audits of their existing data. This ensures accuracy and relevancy in the new system. Additionally, working closely with the CMMS vendor can facilitate the migration process effectively. They often provide tools and methodologies specifically designed for this purpose to streamline the transfer and minimize data loss.
Integration with Existing Systems
The final major challenge lies in integrating CMMS software with existing systems. Many organizations already have several software solutions for different functions, such as inventory management and human resources. Ensuring compatibility between these systems and the new CMMS can be difficult. Lack of proper integration can lead to isolated data sets, inefficient workflows, and ultimately undermine the benefits of adopting CMMS.
To address these issues, organizations should evaluate their existing systems before selecting a CMMS. Looking for software that has flexible integration options can significantly help. Collaborating with IT professionals or vendors who have experience with integrations can also provide insights and support, ensuring that the systems work harmoniously together.
"Understanding and addressing these challenges upfront can lead to a successful and efficient CMMS implementation."
By being aware of these challenges and preparing for them, companies can maximize their investment in CMMS software. This preparation allows for smoother transitions and lays the foundation for improved maintenance operations.
Selection Criteria for CMMS Software
Choosing the right Computerized Maintenance Management System (CMMS) software is a critical task for organizations of any size aiming to enhance their maintenance operations. As technology evolves, the selection process becomes increasingly complex. The importance of thorough selection criteria cannot be overstated. With so many options available, organizations must evaluate various aspects to ensure they choose a solution that aligns with their goals and operational needs.
Understanding Organizational Needs
Before diving into available software options, it is essential to take a step back and fully understand your organization's unique needs. Each organization has distinct systems, processes, and maintenance challenges. Identifying these factors is crucial in selecting CMMS software that will deliver the most significant benefits.
- Identify Current Pain Points: Start by evaluating existing maintenance processes. Identify recurring issues such as excessive downtime, ineffective communication, or slow response times. This insight guides the decision-making process and helps narrow down suitable software solutions.
- Determine Key Features Required: Consider the features most relevant to your operations. Do you need mobile access for field technicians? Is work order management a high priority? Collaborating with stakeholders across different departments can yield valuable perspectives about specific requirements.
- Assess Future Growth Plans: Organizations must also consider future expansions or changes. The software should be scalable to accommodate growth without requiring an entire system overhaul. Failing to account for future needs may lead to increased costs and disruptions down the line.
Evaluating Vendor Reputation
When choosing CMMS software, it is essential to evaluate the reputation of potential vendors. A strong vendor can greatly influence the success of the software in meeting your needs.

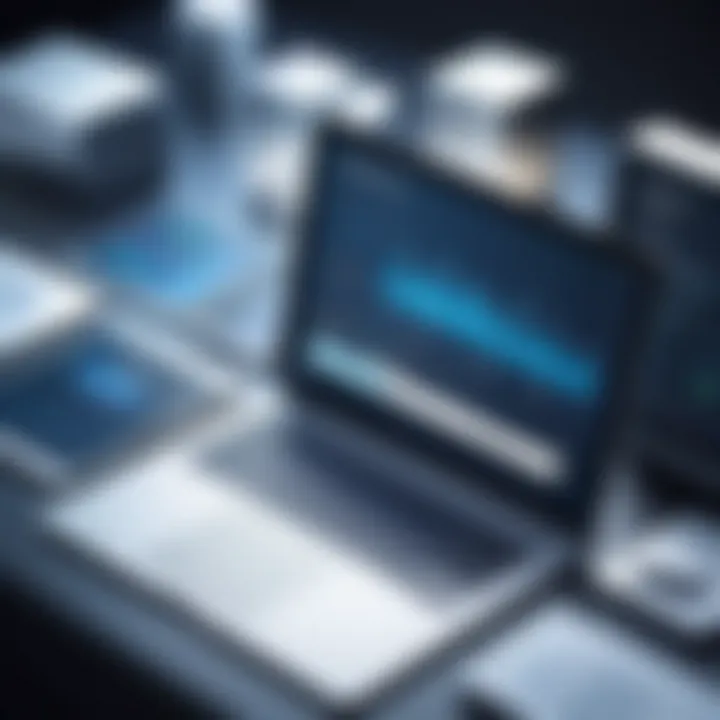
- Research User Reviews: Look for user feedback on various platforms. Websites like Reddit and industry-specific forums can provide real-world insights about different software options. Pay attention to both positive and negative reviews to get a balanced understanding.
- Seek Industry Recommendations: Consult colleagues or industry contacts who have experience using specific brands. Their firsthand accounts can help in gauging a vendor's reliability and service quality.
- Examine Customer Support: Strong customer support is a key factor in effective implementation and ongoing use. Evaluate the vendor's support response times and the availability of training resources. A supportive vendor can greatly enhance your experience.
Total Cost of Ownership
Understanding the total cost of ownership (TCO) associated with CMMS software is essential in evaluating financial commitments. Beyond initial purchase costs, there are several factors to consider.
- Licensing and Subscription Fees: Identify whether the software operates on a one-time purchase basis or a subscription model. Assess the costs over time to ensure the chosen solution fits your budget.
- Implementation Costs: This includes training, data migration, and possible hardware upgrades. These hidden costs can significantly impact the overall budget.
- Maintenance and Upgrades: Consider the long-term financial implications of maintenance and any required software upgrades. Organizations must ensure their chosen solution remains efficient without incurring unexpected expenses.
"Selecting the right CMMS software encompasses understanding what your organization truly needs, evaluating vendor reputation, and thoroughly calculating the total cost of ownership."
Taking the time to carefully consider these selection criteria leads to more informed decision-making and, ultimately, a more effective CMMS deployment.
The Future of CMMS Software
The future of CMMS software is promising and evolving. As organizations increasingly rely on technology to support their maintenance operations, understanding emerging trends becomes critical. Several factors will influence how CMMS software develops in the coming years. The incorporation of advanced technologies such as artificial intelligence (AI), Internet of Things (IoT) devices, and sustainability initiatives will lead to significant enhancements in how these systems function.
Adoption of Artificial Intelligence
Artificial Intelligence is shaping the future landscape of CMMS software significantly. The integration of AI allows for predictive maintenance, which is a substantial advancement over traditional methods. With precise data analysis, companies can foresee equipment failures before they occur. This predictive capability minimizes downtime and extends the lifetime of assets.
AI also enhances the decision-making process. With machine learning algorithms processing large volumes of operational data, organizations can identify patterns and optimize their maintenance schedules effectively. In this way, AI not only improves efficiency but also reduces overall operational costs.
Integration with IoT
The integration of Internet of Things is another vital aspect of the future of CMMS software. IoT devices enable real-time monitoring of equipment condition. This live data stream allows organizations to make timely interventions, reducing the time spent on maintenance.
The synergy between CMMS and IoT leads to smarter asset management. Data collected from connected devices can feed directly into CMMS systems for analysis. This integration further aids in resource allocation and prioritization of maintenance tasks. As IoT technology continues to advance, so too will the capabilities of CMMS software.
Sustainability and Green Initiatives
Sustainability is becoming a core value for many organizations. Future CMMS software will increasingly emphasize green initiatives. This shift reflects a broader commitment to environmental responsibility.
Organizations are looking to reduce their carbon footprint. Advanced CMMS systems can track energy usage and help identify areas where efficiency can be improved. Moreover, they can facilitate the selection of environmentally friendly materials and processes.
The End
The conclusion of this article serves as a critical point to reflect on the journey through CMMS maintenance software. This software is not just a tool; it is a framework that transforms maintenance operations within organizations. Recognizing the significance of adopting CMMS leads to improvements in various key areas, such as operational efficiency and cost management.
Summary of Key Insights
In summary, CMMS software brings numerous advantages that are essential for modern enterprises. Here are the main insights:
- Increased Efficiency: Automating maintenance tasks reduces manual errors and increases accuracy.
- Cost Management: By optimizing inventory and prolonging asset life, organizations can significantly lower maintenance costs.
- Data-Driven Decision Making: The ability to generate reports provides actionable data for better strategic planning.
- Regulatory Compliance: Maintaining detailed logs aids organizations in meeting various compliance standards.
These insights underpin the necessity for businesses to consider CMMS as an integral part of their operational strategy.
Final Thoughts on Future Trends
The future of CMMS maintenance software looks promising as it continues to evolve with technology. Notable trends to watch include:
- Artificial Intelligence: Enhanced predictive maintenance capabilities can foresee equipment failures.
- Internet of Things (IoT) Integration: IoT devices facilitate real-time data collection, making maintenance more proactive.
- Sustainability Initiatives: Organizations are focusing on green practices, and CMMS can support these efforts by promoting efficient resource usage.
As CMMS capabilities advance, organizations should remain attentive to these trends. Adapting to these changes will be crucial to achieving not only increased productivity but also a competitive edge in the market.
"Investing in CMMS not only safeguards assets but optimally aligns maintenance with the goals of the business."
Overall, this exploration of CMMS maintenance software illustrates its undeniable importance in optimizing maintenance practices. The combination of increased efficiency, cost effectiveness, and future technological advancements makes a compelling case for organizations to embrace this software.