Top Warehouse Management Systems: A Comprehensive Guide
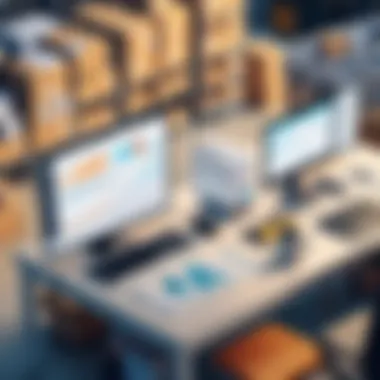
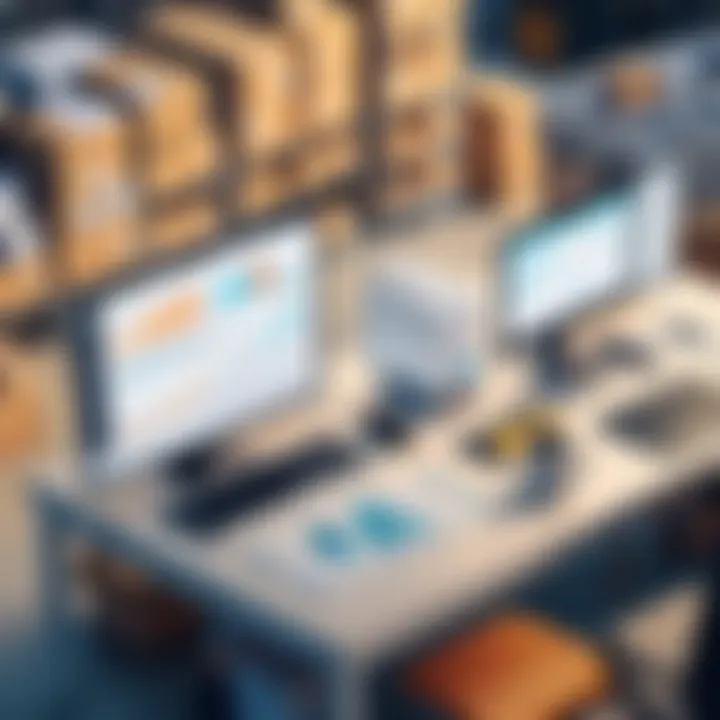
Intro
In the contemporary business environment, efficient inventory management is paramount. The rise of e-commerce and global supply chains places heightened demands on logistics. Warehouse Management System (WMS) software has emerged as a crucial tool. This software enables organizations to optimize their storage and distribution processes. Understanding the value and functionalities of various WMS options is essential for any business aiming for operational excellence.
This article seeks to provide clarity on the various WMS software available today. By detailing their key features, pricing structures, and user experiences, this guide caters to IT professionals, business owners, and decision-makers. The goal is to offer data-driven insights that help in choosing the right system for specific needs.
Software Overview
Software Category and Its Purpose
Warehouse Management Systems are sophisticated software solutions designed to support and streamline warehouse operations. Their primary purpose is to enhance inventory accuracy, reduce operational costs, and improve order fulfillment speed. A WMS typically manages tasks such as inventory tracking, picks and packing processes, and shipping logistics.
Key Features and Functionalities
Each WMS software has specific features that set it apart. Common functionalities include:
- Real-time inventory tracking: Automation allows for live updates on stock levels.
- Order management: Facilitates the processing of customer orders efficiently.
- Reporting & analytics: Provides insights into warehouse performance metrics.
- Integration capabilities: Works seamlessly with other systems such as ERP or SCM solutions.
With these features, businesses can make informed decisions, improving overall efficiency.
Comparative Analysis
Comparison with Similar Software Products
When evaluating WMS solutions, it is essential to compare them against similar products. For instance, systems like SAP Extended Warehouse Management and Oracle Warehouse Management Cloud offer different advantages. Detailed comparisons can reveal which software aligns best with specific operational goals.
Market Positioning and User Demographics
Understanding market positioning is vital. Some WMS products cater specifically to small and medium enterprises, while others are geared towards larger corporations. User demographics often determine the design and scalability of the software, influencing its adoption across different sectors.
"The right WMS software can transform your warehouse into a competitive advantage, provided you choose the one that fits your needs best."
In summary, the analysis of various warehouse management system software presents an opportunity to enhance business logistics efficiency significantly.
Understanding Warehouse Management Systems
Warehouse Management Systems (WMS) are vital tools that streamline and optimize the management of warehouse operations. Having a comprehensive understanding of WMS is essential for businesses aiming to enhance their logistics and operational efficiencies. This section delves into the definition of WMS and its significance within supply chain management.
Definition of WMS
A Warehouse Management System is a software application designed to support and automate warehouse functionality. This includes inventory management, order fulfillment, shipping, and receiving. By providing real-time data, a WMS allows businesses to track product quantities and locations throughout the warehouse effectively. The system is central to ensuring that stock levels are maintained, orders are picked accurately, and products are shipped on time.
Importance of WMS in Supply Chain Management
The role of a WMS extends beyond mere inventory tracking. It plays a crucial part in the optimization of the supply chain. Here are several key benefits of implementing a WMS:
- Enhanced Visibility: A good WMS gives organizations greater visibility over their inventory. Users can obtain real-time insights into stock levels and product movements. This visibility minimizes the risk of stockouts and reduces excess inventory.
- Improved Accuracy: By automating processes like picking and packing, a WMS reduces human errors. Accurate order fulfillment improves customer satisfaction and fosters trust in the business.
- Operational Efficiency: A WMS allows for better resource allocation. Tasks such as inventory counting or order picking can be streamlined, leading to faster processing times. For instance, functions can be scheduled to avoid delays in workflow.
- Cost Reduction: Efficient warehouse management leads to lower operational costs. By optimizing storage space and inventory handling processes, businesses can reap significant savings in their logistics operations.
Implementing a WMS can lead to significant improvements in supply chain efficiency, helping businesses achieve their operational goals more effectively.
Overall, an understanding of Warehouse Management Systems is indispensable for businesses looking to excel in logistics and inventory management. This knowledge enables IT professionals and business leaders to make informed choices regarding software selection, directly influencing operational success.
Key Features of Top WMS Software
The realm of warehouse management system (WMS) software is diverse and competitive. Understanding the key features is vital for organizations aiming to optimize their supply chain processes. This segment highlights the critical aspects of WMS that enhance efficiency, accuracy, and overall effectiveness in warehouse operations. Each feature plays a significant role in meeting the demands of modern logistics.
Inventory Tracking Capabilities
Accurate inventory tracking is the cornerstone of effective warehouse management. WMS software provides real-time data on stock levels, locations, and movement within the warehouse. This level of visibility ensures that businesses can respond swiftly to stock discrepancies, thus minimizing loss and optimizing resources. Furthermore, advanced WMS solutions utilize barcodes and RFID technology to automate inventory tracking, reducing human error and streamlining operations. With these capabilities, businesses can maintain optimal stock levels, prevent stockouts, and manage inventory turnover efficiently.
Order Fulfillment Processes
Order fulfillment is a critical component of warehouse operations. The right WMS software enhances this process through automated picking, packing, and shipping functions. Efficient order management reduces processing time and improves customer satisfaction. By utilizing features like batch picking and wave picking, staff can handle multiple orders simultaneously, significantly increasing overall productivity. Additionally, integrating order tracking functionalities allows businesses to provide customers with accurate delivery timelines, which is key to maintaining trust in the e-commerce landscape.
Integration with Other Systems
A robust WMS must seamlessly integrate with other essential systems such as Enterprise Resource Planning (ERP), Customer Relationship Management (CRM), and supply chain management tools. This integration ensures a harmony of data flow across different functionalities within the organization. With everything interconnected, organizations can improve decision-making, as all departments share real-time information. For instance, when inventory levels are updated in the WMS, the ERP system reflects this change instantly, enabling proactive reordering and stock management.
Reporting and Analytics Tools
Data-driven decision-making is essential for competitive advantage. Advanced WMS software comes with powerful reporting and analytics tools that provide insights into key performance indicators (KPIs). These reports help organizations identify trends, assess productivity levels, and evaluate inventory turnover rates. By leveraging such data, businesses can refine their strategies, making informed choices that drive efficiency and growth. The ability to create custom reports will enable managers to focus on metrics that align with their specific operational goals, ensuring that strategies are tailored for optimal performance.
"Effective warehouse management hinges on the seamless integration of technology with operational processes."
In summary, understanding and leveraging these key features of WMS software empower organizations to enhance their logistical efficiency. Each capability contributes uniquely to streamlining operations, improving customer service, and achieving scalability in a rapidly evolving market. As businesses evaluate their options, a clear grasp of these features will be instrumental in selecting software that truly fits their operational needs.
Types of WMS Software
Understanding the different types of Warehouse Management System (WMS) software is crucial for organizations seeking to optimize their logistics operations. Each type offers unique advantages and challenges. Selecting the right solution can significantly impact efficiency, cost, and overall success in supply chain management. This section will cover the three primary types of WMS software: On-Premise Solutions, Cloud-Based Alternatives, and Hybrid Systems. Each type presents distinct features and considerations that align with various business needs.
On-Premise Solutions
On-Premise WMS solutions are installed directly on the company's servers. This gives organizations total control over their software and data. One key benefit of on-premise systems is the customization potential. Businesses can tailor the software to meet their processes without restrictions from third-party providers. Additionally, for companies managing sensitive data, on-premise solutions may provide more robust security.
However, these systems often require higher upfront investment costs and ongoing maintenance expenses. Organizations need to invest in hardware infrastructure and IT personnel to manage the system. Moreover, updates may not be automatic, leading to potential issues if the software becomes outdated.
Cloud-Based Alternatives
Cloud-Based WMS software operates on the cloud, allowing businesses to access their systems via the internet. This type of software is usually subscription-based, leading to lower initial investments. Cloud solutions are often more scalable than on-premise options, making them a good choice for growing businesses.
The ease of updates is another advantage. Users receive automatic updates, ensuring they always have the latest features and security enhancements. Furthermore, communication and integration with other cloud-based platforms and services is typically seamless.
However, companies should consider their internet reliability. If the network goes down, access to the system may also be interrupted, affecting business operations. Security is another concern, as data is stored off-site, which might not align with all companies' compliance requirements.
Hybrid Systems
Hybrid WMS solutions combine features from both on-premise and cloud-based systems. These systems offer the flexibility of cloud access while still allowing for some data to be stored locally. This approach can satisfy organizations needing certain data on-site for compliance or performance reasons.
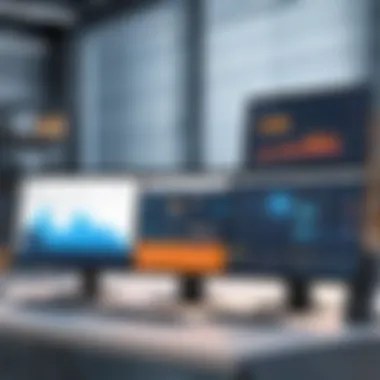
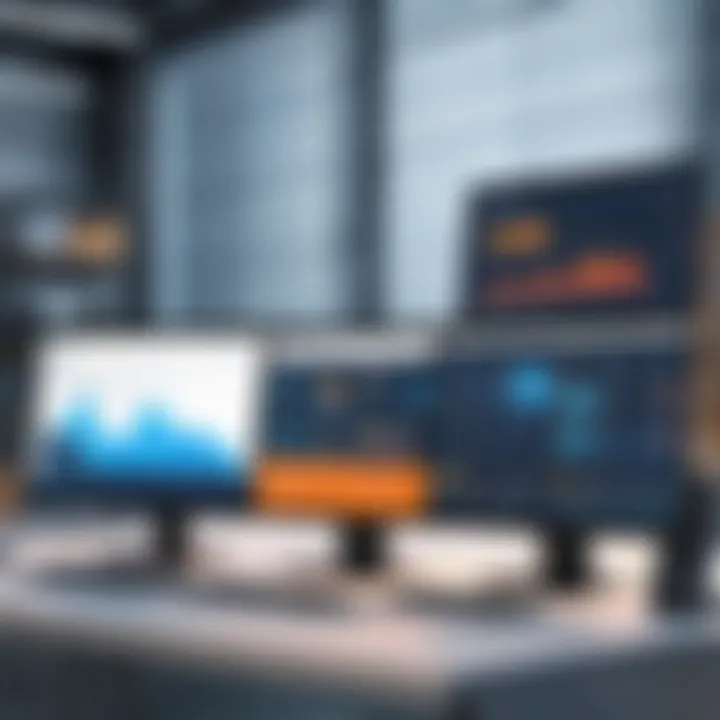
The main advantage here is adaptability. Organizations can retain control over critical operations through on-premise systems while benefiting from cloud scalability and ease of use. Costs can vary widely depending on how the hybrid system is implemented. Generally, they may be more expenseive than purely cloud solutions but potentially less than fully on-premise implementations.
Choosing the right type of WMS software is essential. By understanding the features and requirements of each system type, businesses can align their choice with their operational goals.
Scalability in WMS Software
Scalability in warehouse management system (WMS) software holds significant importance for businesses that aim to grow and adapt in a volatile market. As organizations expand, their operational requirements can shift dramatically. A scalable WMS ensures that businesses can adjust their resources and functionalities to keep up with increased demands. This flexibility not only enhances efficiency but also protects the initial investment in software.
When a warehouse management system is scalable, it effectively minimizes disruption during periods of business growth, allowing companies to add new features or increase capacity without overhauling the entire system. This leads to sustained productivity and reduces potential downtime. Thus, scalability can be viewed as a long-term strategy that safeguards against obsolescence.
Adapting to Business Growth
The ability to adapt to business growth is a crucial characteristic of scalable WMS software. As market demands fluctuate, businesses may face sudden spikes in order volume or shifts in product types. A scalable system can handle these changes efficiently.
- Increased Storage Needs: Scalability allows for the addition of new storage locations or modifications in layout without disrupting existing operations.
- Expanded Functionality: As business needs evolve, new features can be integrated seamlessly. For example, if a company starts offering seasonal products, specific functionalities for tracking these items can be implemented.
- Resource Management: A scalable WMS helps optimize workforce management as well. If the business grows, the system can incorporate additional staff or roles to maintain efficiency.
The adaptability of WMS software is critical in a fast-paced supply chain environment.
Customizable Features
Another significant element of scalability is the availability of customizable features. Businesses are unique, and their WMS should reflect that individuality. Customizable features in a WMS allow different organizations to tailor functions according to their specific needs.
- User Preferences: Different staff members may have varying needs based on their roles. A customizable WMS enables tailored dashboards and operational tools, enhancing usability.
- Process Alignment: Each industry may require distinct workflows. Custom features can ensure that a WMS aligns closely with the company’s specific operational processes, from shipping to returns management.
- Integration Options: Customization should extend to integration capabilities, enabling the WMS to sync with existing ERP systems or other necessary software. This ensures a cohesive data flow across business functions.
In summary, scalability within WMS software is essential for adapting to changes in business size and market dynamics. The ability to implement custom features further solidifies a warehouse management system's utility across various industries.
Cost Considerations for WMS Software
Cost is a crucial factor when selecting a Warehouse Management System (WMS). It influences the decision-making process significantly. A clear understanding of the financial implications can lead to more informed choices. The right WMS software can offer both immediate and long-term benefits, thus improving the overall efficiency of warehouse operations. Businesses must weigh the initial costs against potential savings over time.
Initial Investment vs. Long-Term Savings
Investing in WMS software involves upfront expenses such as purchasing, implementation, and training costs. These initial costs can seem high but must be considered against the long-term savings and improvements in efficiency. With proper planning, businesses can reduce operational costs, minimize errors, and improve inventory management. For instance, a robust WMS can decrease labor costs and enhance order accuracy. Thus, the return on investment may surpass initial outlay over time.
"A well-chosen WMS has the potential to pay for itself within a few years by streamlining processes, reducing inventory holding costs, and enhancing customer satisfaction."
Pricing Models in the Industry
When evaluating WMS software, it's essential to understand the different pricing structures available. Key models include:
- Subscription-based Pricing: Common in cloud solutions. Businesses pay a regular fee, which can simplify budgeting.
- Perpetual Licensing: A one-time purchase with ongoing maintenance costs. This model can be more costly initially but may offer savings in the long run.
- Tiered Pricing: Costs vary based on features or modules chosen. Users can select only what they need, tailoring the investment to their requirements.
- Freemium Models: Some providers offer basic versions for free, charging for premium features. This can allow companies to test software before committing financially.
Understanding these models can help organizations align their budget with operational goals. Choosing the right pricing structure can significantly affect the overall cost of ownership.
User Experience and Interface
User experience (UX) and interface design are crucial in evaluating warehouse management system (WMS) software. A positive UX can significantly influence staff adoption rates, streamline operations, and improve overall efficiency within the supply chain. Users need a system that is intuitive and minimizes the learning curve. Software with a complex interface can deter staff from utilizing its full potential, leading to inefficient processes or even errors in inventory management.
Ease of Use for Staff
The ease of use for staff directly impacts how quickly they can adapt to the new software. A system that is straightforward allows employees to navigate effortlessly through various functions. It reduces frustration that can arise from cumbersome navigation. Simple icons, clear menus, and logical workflows help facilitate quick understanding.
Benefits of a User-Friendly Interface
- Reduces Training Time
- Increases Productivity
- Minimizes Errors
- Enhances Employee Satisfaction
Using an interface that promotes ease of use is not just beneficial for immediate tasks but impacts long-term operational practices. Staff who feel confident using the system will likely engage more deeply with the functionality provided.
Training Requirements
Despite a user-friendly interface, training remains essential. Effective training helps staff become familiar with advanced features and functionality that a WMS offers. Initial training sessions should cover all critical elements of the system. Ongoing training sessions can be designed to introduce new features as the software evolves.
Consideration must also be given to the various learning styles of employees. Some may prefer hands-on training while others benefit from guided video tutorials or written manuals. Flexibility in training approaches can dramatically enhance staff readiness and capability.
"Investing in quality training can increase job competency and retention of institutional knowledge, creating stability in operations."
A thorough understanding of training requirements underscores the importance of a robust user experience. Without proper training aligned to the interface, even the best-designed system may falter in execution. The goal should always be on maximizing usability and ensuring that the staff feels equipped to leverage the software to its fullest potential.
Integration Capabilities of WMS Software
In today's complex business environment, the ability of Warehouse Management Systems (WMS) to integrate with other software solutions is a significant factor in their effectiveness. Successful integration capabilities allow companies to create a seamless flow of information and ensure the optimal functioning of inventory management processes. This aspect becomes critical as businesses adopt multiple software solutions to handle various aspects of logistics and operation.
A solid WMS should not operate in isolation; its integration with other systems enhances operational efficiency, reduces data entry errors, and improves overall communication among departments. For companies looking to scale and adapt to changing operational needs, these integration capabilities become even more essential. Here are key considerations and benefits regarding integration capabilities:
- Enhanced Data Visibility: Integrating a WMS with various data sources, like ERP or supply chain software, provides real-time insights. For example, seamless access to inventory levels allows quick decision-making, improving responsiveness.
- Streamlined Operations: When a WMS connects effectively with other systems, it minimizes the need for manual processes. Automated data exchange means less chance for human error and faster order fulfillment.
- Customization Options: Each business has specific operational requirements. A WMS that supports various integration avenues allows for tailored solutions, providing distinct competitive edges.
"Integration enhances the strategic value of WMS by fostering collaboration among different functional areas, ultimately leading to superior customer service and operational efficiency."
ERP Systems Compatibility
Integrating WMS with Enterprise Resource Planning (ERP) systems is particularly vital. ERP systems handle core business functions such as finance, HR, and supply chain management. A well-integrated WMS can significantly enhance the efficiency of these functions.
Key Advantages:
- Accurate Data Synchronization: Keeping inventory data consistent across platforms reduces discrepancies.
- Improved Reporting: With integrated data, generating insightful reports becomes easier, aiding better financial and operational planning.
- Operational Cohesion: Teams working from the same data source foster better interdepartmental collaboration, aligning efforts toward common goals.
Selecting a WMS that allows easy integration with major ERP systems, such as SAP or Oracle, ensures that organizations can leverage their existing investments while boosting productivity.
Third-Party Logistics Integration
Third-Party Logistics (3PL) providers are increasingly adopting WMS solutions to enhance their service offerings. Integrating WMS with 3PL services is a strategic move for businesses that rely on external logistics providers. This integration creates a transparent interface for managing logistics activities more effectively.
Benefits Include:
- Cost Reductions: Efficiently managing logistics operations reduces waste and lowers costs.
- Scalable Solutions: As businesses grow, integrating with 3PL providers can help companies scale their logistics operations without substantial infrastructure investment.
- Data-Driven Decisions: Enhanced data flow between the WMS and 3PL offers actionable insights, allowing businesses to refine their logistics processes and inventory management.
Evaluating Vendor Reputation
In the realm of warehouse management systems (WMS), choosing the right software vendor is a critical aspect of ensuring operational success. Evaluating vendor reputation is not just a preliminary step; it’s foundational in decision-making. A solid reputation often correlates with reliable products and services. This segment will explore why assessing vendor credibility and gathering insights from customers are necessary for informed choices.
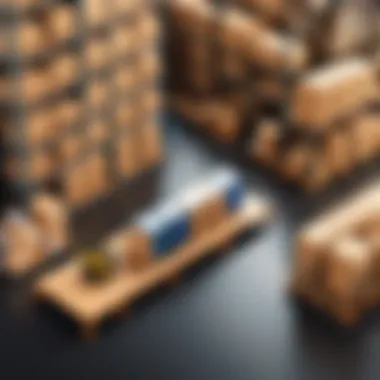
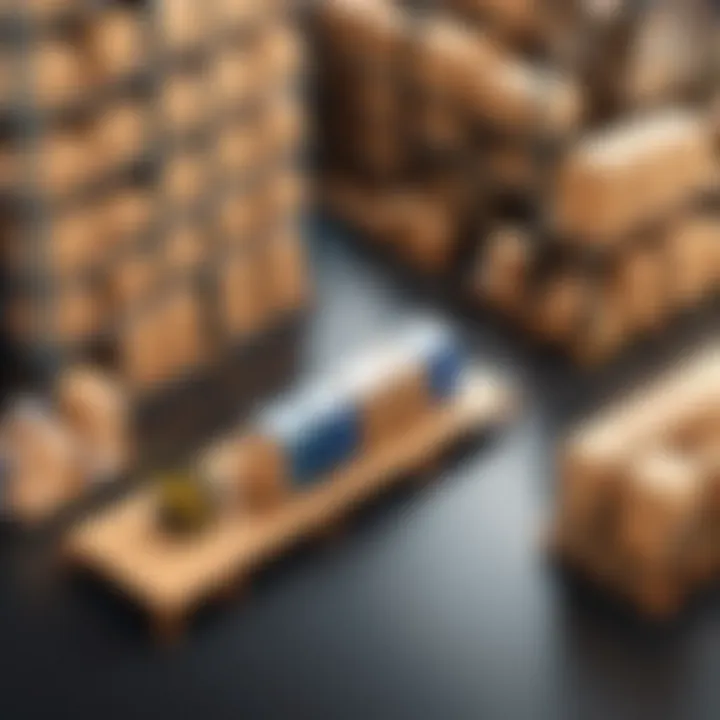
Researching Provider Credibility
Researching the credentials and history of WMS providers can save businesses both time and resources. Start by examining how long the vendor has been in the market. Established companies often have refined their offerings over time and built a strong reputation. Consider the following elements when researching a provider:
- Longevity: A vendor’s time in the industry is a good indicator of stability and reliability.
- Certifications: Check for any industry-specific certifications that demonstrate adherence to quality standards.
- Partnerships: Vendors who maintain strong partnerships with prominent technology companies often leverage more advanced tools and solutions.
Next, visit professional platforms such as LinkedIn to explore the company’s activities and employee engagement. Companies that show a commitment to employee growth and customer satisfaction typically have a more robust and adaptable service. Utilizing resources like Wikipedia or Britannica may also offer historical context about the company's reputation and evolution in the market.
Customer Reviews and Case Studies
Customer reviews provide real-world insights into a vendor's capabilities and service quality. These testimonials can elucidate both strengths and weaknesses of the software in action. Access various review platforms where users share their experiences, such as Reddit or even on the vendor's page itself. Look for patterns in the feedback:
- Common Issues: Take note of repeated complaints; these could indicate significant problems within the software.
- User Experience: Positive reviews regarding the interface and support services suggest that users find the software manageable and beneficial.
An effective way to gauge customer satisfaction is through case studies. These documents typically outline how a particular business utilized the WMS, the challenges faced, and the solutions provided by the vendor. Case studies can reveal practical applications and success metrics that might not appear in standard reviews. They give a clearer picture of whether a vendor can meet your specific needs.
In summary, thoroughly evaluating vendor reputation is essential for a successful WMS implementation. A provider’s credibility and customer feedback can illuminate the path toward making a sound decision that aligns with your business's logistics goals.
Future Trends in WMS Technology
The landscape of warehouse management systems (WMS) continues to evolve. Staying current with future trends is essential for companies looking to maintain a competitive edge. As logistics and supply chains undergo transformations, the integration of advanced technologies is becoming increasingly vital. Understanding these trends helps organizations identify opportunities to enhance efficiency, reduce costs, and improve customer satisfaction.
Automation and Robotics
Automation has emerged as a key player in optimizing warehouse operations. Automated processes streamline various tasks, such as inventory management, order fulfillment, and shipping. By minimizing human intervention, companies can achieve higher accuracy and faster processing times.
Robotics technology also plays a significant role. Automated guided vehicles (AGVs) can transport goods within the warehouse, reducing the need for manual labor. These robots ensure that products are moved efficiently and safely. Additionally, robotic arms are used for tasks like packaging and sorting, which can further expedite operations.
Benefits of automation and robotics include:
- Increased Efficiency: Reduced time for repetitive tasks leads to faster throughput.
- Cost Reduction: Lower labor costs, even when factoring in the initial investment in technology.
- Improved Accuracy: Reduce human error through consistent robotic operations.
As companies implement these technologies, they may face considerations such as upfront costs, training for staff, and integration with existing systems. Nonetheless, the long-term advantages far outweigh these initial challenges.
Artificial Intelligence Integration
Artificial intelligence (AI) is revolutionizing how warehouses operate. With AI integration, WMS software can analyze vast amounts of data, enabling better decision-making. This technology can predict inventory needs, optimize storage solutions, and enhance overall operational efficiency.
AI improves forecasting accuracy by analyzing trends, seasonal demands, and sales patterns. This leads to:
- Enhanced Inventory Management: Companies can anticipate stock shortages or overages, reducing waste and lost sales.
- Dynamic Routing: AI can optimize shipping routes in real-time based on traffic conditions, weather, and other variables.
- Personalized Customer Experiences: By analyzing customer data, businesses can tailor their offerings to meet specific needs, which can lead to increased loyalty.
Integrating AI in WMS does present challenges, including the need for a skilled workforce and the potential for data privacy concerns. However, the benefits of improved efficiency and responsiveness to market changes validate these investments.
Investing in future technologies like automation and AI is no longer optional; it is a critical component for success in modern warehousing.
In summary, understanding future trends in WMS technology, particularly automation and AI, is crucial for businesses aiming to optimize their logistics operations. Embracing these advancements equips companies to meet evolving consumer demands while maintaining efficiency and cutting costs.
Case Studies of Leading WMS Software
Case studies are pivotal in illustrating the practical applications and effectiveness of warehouse management system (WMS) software. By showcasing real-world scenarios, these studies provide valuable insights into how various organizations have implemented WMS solutions to overcome operational challenges. Understanding these case studies allows businesses to visualize potential impacts, tailor solutions to their needs, and make informed decisions about adopting specific WMS technologies.
One significant benefit of analyzing case studies is the ability to learn from the experiences of others. Companies can identify key success factors that contributed to effective inventory management, streamlined order fulfillment, and improved operational efficiency. Additionally, these studies highlight challenges faced during the implementation process and the strategies employed to address them. This knowledge equips organizations with better preparedness when integrating their chosen WMS.
Furthermore, case studies foster a deeper understanding of the versatility of WMS solutions across different industries. When organizations see tangible results in sectors like retail, manufacturing, and healthcare, they gain confidence in the scalability and adaptability of the systems they are considering.
“Learning from others’ experiences is one of the most effective ways an organization can improve its own processes.”
Success Stories in Inventory Management
Success stories in inventory management provide active examples of how companies have transformed their warehousing practices through WMS. For instance, consider a retail chain that faced significant issues with stockouts and overstock situations. After implementing a leading WMS solution, the company utilized real-time inventory tracking, which allowed them to maintain optimal stock levels. As a result, they reduced their carrying costs by 20% and improved customer satisfaction due to enhanced product availability.
Another salient example involves a manufacturing firm that struggled with order inaccuracies and delayed shipments. Upon integrating a WMS with advanced analytics features, they saw a considerable decrease in errors during the picking and packing processes. This improvement directly led to a 30% increase in order fulfillment speed, thus positively impacting client relationships and operational throughput.
Comparative Analysis of Market Leaders
A comparative analysis of market leaders in WMS software reveals distinct characteristics and capabilities that set them apart. Each solution offers unique features tailored to different business environments. For example, SAP Extended Warehouse Management excels in complex, large-scale inventory operations, while Oracle Warehouse Management Cloud stands out for its seamless cloud integration and intuitive user interface.
When evaluating various WMS software options, businesses should consider the specific functionalities that align with their operational requirements. By examining aspects like scalability, customization options, and integration capabilities, decision-makers can better understand how each solution matches their logistics framework.
In addition, analyzing market leaders' strengths and weaknesses aids in discerning which software provides the best ROI for various industry situations. Some WMS solutions are particularly effective in environments with high product turnover, while others might be more adept at handling less frequently ordered items. Understanding these nuances enables organizations to select a WMS that drives efficiency in their particular operational context.
Customizing WMS for Specific Industries
Customizing a Warehouse Management System (WMS) for specific industries is not just beneficial; it is crucial for optimizing operations and achieving maximum efficiency. Each industry has unique challenges and requirements that a one-size-fits-all solution cannot adequately address. Customization allows businesses to align the software capabilities with their operational processes, improving accuracy and speed in logistics management.
When businesses embrace tailored WMS solutions, they can integrate features that directly respond to the intricacies of their industry. Specific elements to consider include regulatory compliance, inventory turnover rates, and the nature of products managed. Benefits really add up, as businesses can see enhanced productivity, reduced operational errors, and improved customer satisfaction.
Retail and E-commerce Solutions
In the retail and e-commerce sectors, inventory control is key. A customized WMS focuses on streamlining order processing and improving stock visibility. Enabling real-time inventory tracking is critical here. Businesses can minimize stockouts and overstock situations. Automation features, such as order fulfillment and returns management, enhance the customer experience.
Challenges like seasonal demand fluctuations also require specialized solutions. Customization can include advanced forecasting tools, enabling retailers to make well-informed decisions based on shopping trends. This way, the WMS becomes a strategic asset rather than just a support tool.
Manufacturing Needs
In manufacturing, a tailored WMS addresses aspects like production scheduling and materials management. The integration of just-in-time inventory practices can significantly enhance efficiency. Manufacturers often deal with complex supply chains and numerous material suppliers. Thus, a customized system must provide robust tracking of raw materials alongside finished goods.
An emphasis on quality control monitoring within the system can ensure compliance with industry standards. Many manufacturers benefit from implementing features that facilitate the management of multi-location inventories, enabling smooth operations across multiple facilities.
Healthcare Sector Requirements
In the healthcare industry, the stakes are higher due to the critical nature of the products managed, such as medications and medical equipment. A WMS customized for healthcare must ensure strict regulatory compliance, including tracking and reporting capabilities for adherence to governmental requirements.
Key functionalities might include expiration date management, ensuring that products are used within their safe period. Furthermore, systems should facilitate ease of access to important inventory data for medical staff, as timely information can directly impact patient care.
Implementation Strategies for WMS Software
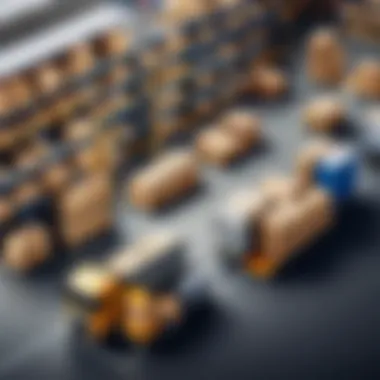
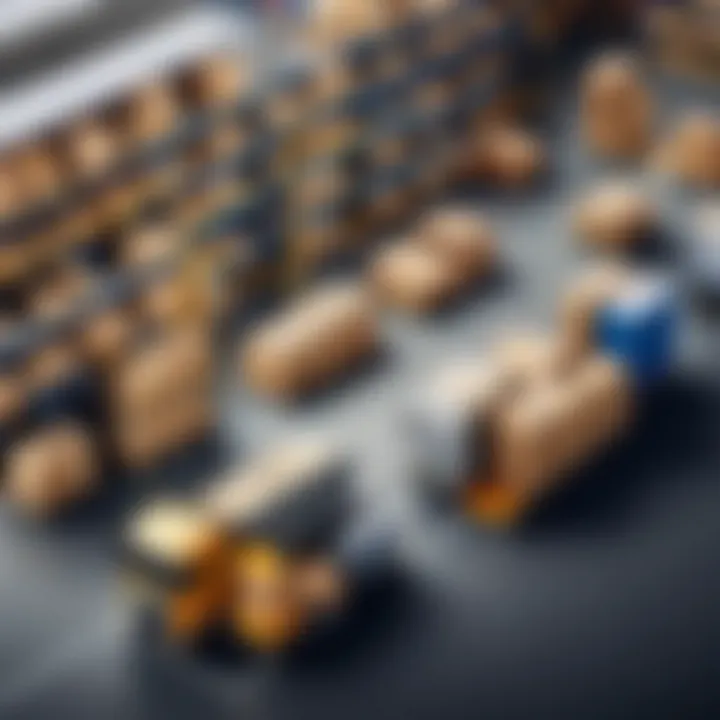
Implementing a Warehouse Management System (WMS) can significantly enhance operational efficiency. Proper strategies during implementation are crucial for ensuring the software delivers expected benefits. The importance of having a structured approach cannot be overstated. It allows businesses to minimize disruption during the changeover, align the system with operational needs, and ultimately achieve a higher return on investment.
Assessing specific elements such as resource allocation, timelines, and workflow integration is essential. A well-planned implementation will address potential pitfalls, ensuring smooth transitions.
Using an agile methodology can also be fruitful. This approach allows for iterative testing and adjustment, fitting the WMS better to evolving business demands. A clear strategy helps in navigating complex scenarios. Companies can respond faster to issues and optimize their operations effectively.
Planning and Preparation
Planning and preparation are foundational to any successful WMS implementation. Taking time upfront to define goals, requirements, and timelines will yield benefits down the line. The planning phase should involve stakeholders from various departments. This will ensure all perspectives are considered, leading to a more comprehensive understanding of organizational needs.
A detailed project plan is necessary. This plan should outline key milestones and deadlines. Involving IT professionals, warehouse managers, and end-users in this phase can gather valuable insights. Here are some considerations:
- Define Key Performance Indicators (KPIs): Measuring success will require clear KPIs that align with business goals.
- Assess Current Processes: Identify gaps in current workflows that the WMS should address.
- Resource Allocation: Ensure appropriate resources, including personnel and technology, are ready for implementation.
Missteps in planning can lead to costly delays and ineffective use of the new system. Therefore, taking a methodical approach ensures that every aspect is covered.
Testing and Feedback Loops
Testing is a critical phase in WMS implementation. Before going live, it is essential to conduct exhaustive testing to discover any issues. This helps to identify bugs and usability challenges that may hinder operational efficiency. Incorporating feedback loops during this phase allows for continuous improvement. Users should be actively involved in providing insights on functionality and ease of use.
A feedback mechanism can involve:
- User Experience Testing: Have real users interact with the system to gauge satisfaction and ease of use.
- Iterative Adjustments: Use feedback to make necessary adjustments before full deployment.
- Documentation of Issues: Maintain a log of problems encountered and solutions implemented to inform future enhancements.
This testing process can lead to a more robust and user-friendly system. It also fosters a culture of collaboration and communication, which is invaluable in the long run.
"Adequate testing and feedback are pivotal to ensuring the implemented WMS meets all business requirements effectively."
Successful implementation strategies are not just about the technology but also about managing people and processes efficiently. By prioritizing planning and testing, companies can leverage their WMS investments for optimal performance.
Ongoing Support and Maintenance
In the realm of warehouse management systems, the importance of ongoing support and maintenance cannot be understated. Organizations invest significant resources into WMS solutions, and the longevity and effectiveness of these systems hinge greatly on their support structure. Proper maintenance ensures that your system remains efficient and up-to-date, adapting to both operational changes and technological advancements.
Regular support also plays a crucial role in minimizing downtime. Any disruptions in warehouse operations can lead to substantial losses; thus, having a reliable support system is essential. Moreover, ongoing maintenance can help in preventing small issues from escalating into major problems that require costly fixes, ultimately safeguarding your return on investment.
Key benefits of ongoing support include ensuring that staff can efficiently use the system, and guaranteeing that the software seamlessly integrates with other tools and platforms within the business environment. This kind of proactive management is critical for long-term success in any logistics operation.
Vendor Support Options
When it comes to vendor support, organizations should carefully assess available options. The quality and responsiveness of vendor support can significantly impact how effectively an organization utilizes its WMS.
Key aspects to consider include:
- Availability of Support: Some vendors provide 24/7 support, while others may operate on limited hours. Understanding your business’s needs is vital when selecting a vendor.
- Support Channels: Options like phone, email, and live chat can vary by vendor. Multi-channel support can provide more flexibility.
- Response Time: Effective vendors should respond promptly to support requests. A long wait for assistance can hinder warehouse operations.
- Documentation and Training: Quality support also includes comprehensive manuals and training resources. This is valuable for onboarding new employees or refreshing the knowledge of existing staff.
Choosing a vendor that excels in these support areas helps ensure that your WMS functions optimally.
Regular System Updates
Regular system updates are a cornerstone of effective WMS maintenance. These updates provide enhancements, bug fixes, and new features that can bolster the user experience. Considering that technology evolves at a rapid pace, keeping the software current ensures that organizations are utilizing all available tools that can improve efficiencies.
Benefits of regular system updates include:
- Enhanced Security: Software updates often include security patches that protect against emerging threats, a crucial factor given the sensitive nature of inventory data.
- Improved Functionality: Updates frequently come with improvements that streamline processes and enhance the overall performance of the WMS.
- User Feedback Implementation: A responsive vendor will often incorporate user feedback into updates. This ensures that the software evolves in alignment with the needs of its users.
- Regulatory Compliance: Industries face ever-changing regulatory demands. Regular updates can help maintain compliance with legal standards, avoiding costly penalties.
"The cost of maintenance is always less than the cost of repair."
By prioritizing these aspects, businesses can enhance their logistical capabilities and maintain a competitive edge in a rapidly evolving market.
Comparative Reviews of Top WMS Software
Comparative reviews of warehouse management system software are critical for organizations looking to enhance their logistics operations. When selecting a WMS, businesses face a plethora of options, each with unique features and functionalities. An informed evaluation not only sheds light on the strengths and weaknesses of various software solutions but also assists in aligning a company's objectives with the right tools. This process involves analyzing how well each system meets specific business needs, facilitating effective decision-making.
Understanding the differences between WMS options can lead to significant improvements in operational efficiency. Companies that invest time in comparative reviews can expect to identify the best fit for their inventory management, order processing, and reporting requirements. As a result, these reviews often provide essential insights into pricing models, user experiences, and integration capabilities.
Leading Solutions Overview
In the landscape of warehouse management systems, several solutions have consistently stood out for their robust functionalities and adaptability. Each of these leading systems presents unique benefits, thus making comparative reviews invaluable.
- SAP Extended Warehouse Management: Renowned for seamless integration with SAP ERP systems, it also features advanced analytics tools.
- Oracle Warehouse Management: Offers extensive automation, real-time inventory tracking, and comprehensive reporting.
- Manhattan Associates WMS: Highly flexible, it is well-suited for various industries and provides strong support for omni-channel fulfillment.
- Infor WMS: Known for its user-friendly interface and strong analytical capabilities, Infor supports strategic decision-making by providing detailed insights.
- Fishbowl Inventory: More suited for small to medium-sized businesses, it focuses on inventory management and order fulfillment without overwhelming complexity.
All of these solutions come with a mix of advantages that cater to specific operational challenges.
Strengths and Weaknesses Analysis
Conducting a strengths and weaknesses analysis is fundamental during the comparative review of WMS software. Here are some pertinent points:
- Strengths:
- Weaknesses:
- Customization: Many leading systems allow for significant customization to meet unique industry specifications.
- Automation: Automation features reduce manual errors and enhance speed in order processing and inventory management.
- Data Insights: Advanced analytics provide actionable insights, aiding strategic decisions and improving supply chain visibility.
- Cost: Some top-tier solutions may require significant upfront investment and ongoing operational costs.
- Complexity: High-end systems can be complex to configure and manage, often requiring specialized training for staff.
- Integration Challenges: While many solutions offer integration capabilities, the actual process may involve technical challenges, ensuring compatibility with existing systems.
By understanding both strengths and weaknesses, decision-makers can find the right balance between functionality and cost-effectiveness.
Epilogue and Recommendations
In this article, we have seen the multifaceted nature of Warehouse Management Systems (WMS) and their pivotal role in streamlining business operations. As companies increasingly rely on efficient logistics to maintain competitiveness, understanding the nuances of WMS software becomes crucial. This section aims to summarize essential insights and provide actionable recommendations for the diverse set of stakeholders involved in the selection process.
Summarizing Key Points
We have explored various aspects of WMS software throughout the article. Key points include:
- Definition and Importance: WMS software is vital for effective supply chain management, enabling accurate inventory tracking and efficient order fulfillment.
- Features and Capabilities: The discussed features like inventory tracking, integration with other systems, and reporting tools are essential for effective warehouse operations.
- Types of Solutions: Distinguishing between on-premise, cloud-based, and hybrid systems helps businesses choose the right deployment model.
- User Experience: Ease of use in WMS directly correlates to operational efficiency. Training requirements also influence user adoption.
- Vendor Reputation: Evaluating provider credibility through research and case studies is crucial for informed decision-making.
"Investing in the right WMS software can lead to significant improvements in efficiency and cost savings for businesses of all sizes."
Next Steps for Businesses
After reviewing the insights from this article, businesses should take the following steps to move forward with their WMS selection:
- Conduct a Needs Assessment: Determine your specific warehouse challenges and needs. This assessment should guide your search for WMS software that aligns closely with your objectives.
- Explore Vendors and Solutions: Use the knowledge gained to create a shortlist of potential providers. Look for solutions that offer scalability, adaptability, and needed features.
- Engage in Demos and Trials: Before committing, participating in product demos or free trials can provide valuable insights on user experience and software functionality.
- Budget Planning: Consider the initial investment against potential long-term savings. Choose a pricing model that aligns with your financial strategy.
- Continuous Learning: Stay informed about future developments in WMS technology. Emerging trends such as automation and AI integration may enhance operational effectiveness further.
By adhering to these recommendations, business leaders can better navigate the complexities of WMS software, leading to improved efficiency and a strategic edge in the marketplace.