Effective Inventory Control Strategies for Accountants
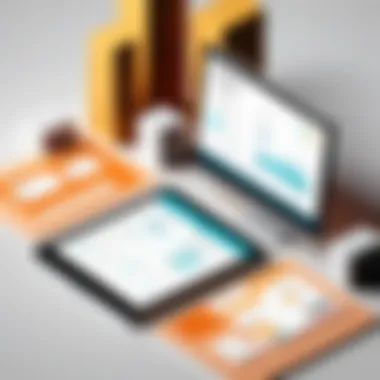
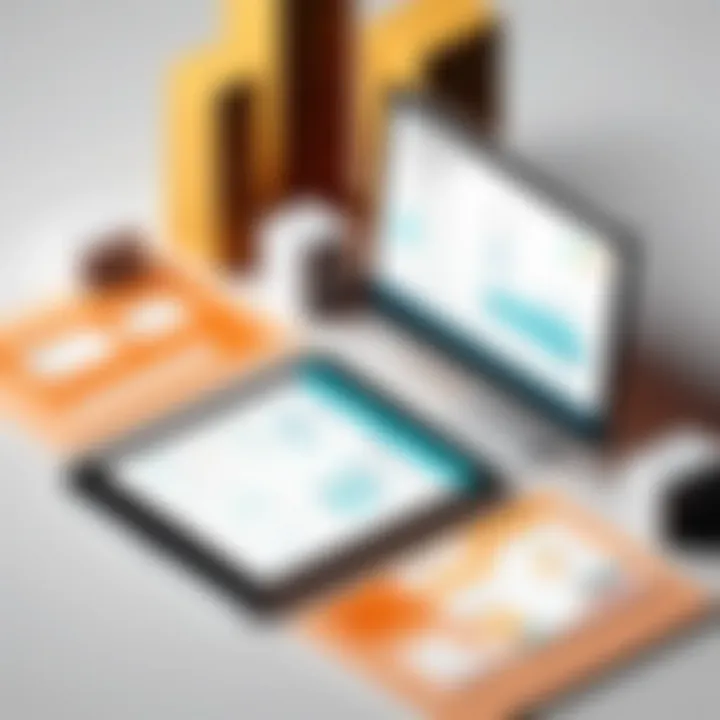
Intro
Inventory control stands as a cornerstone of sound accounting practices, intertwining operational efficiency with financial accuracy. As businesses grow, managing inventory effectively becomes more than just a necessity; it's a strategic advantage. An organization’s ability to monitor its stock can significantly influence cash flow, operational decisions, and overall profitability.
By understanding inventory control, one can gauge how it impacts financial health. It's not merely about knowing how much of a product exists; it's also about knowing what that stock means in the larger financial picture. With the advent of technology, traditional methods have evolved, enhancing accuracy and providing real-time data that can be invaluable for decision-making.
In this article, we'll explore the vital link between inventory control and accounting. From inventory valuation methods to the role of technology in controlling stock levels, we aim to unravel the cogs of this intricate relationship.
Understanding Inventory Control
Inventory control is a linchpin in the intricate machinery of accounting. It involves the processes and systems that manage stock levels, ensuring that a business has the right amount of inventory on hand to meet customer demand without incurring excess costs. The importance of mastering inventory control cannot be overstated; it directly influences a company's profitability and operational efficiency. Proper management of inventory translates into reduced carrying costs and improved cash flow, both vital for sustaining business operations.
Definition and Importance
Inventory control refers to the strategies utilized to oversee and manage the quantity, location, and timing of inventory. This activity isn't merely about counting items but involves a deeper understanding of forecasting demand, identifying trends, and optimizing stock levels. The importance lies in its capacity to prevent stock shortages and excesses, both of which can create operational headaches. A well-maintained inventory system ensures that products are available when needed while minimizing waste and obsolescence.
Types of Inventory
Different types of inventory exist, each serving a distinct purpose in the realm of business operations. Recognizing these categories can help in making informed management choices.
- Raw Materials: These are the basic materials used in the manufacturing process. Their availability is critical to ensuring production runs smoothly. The fundamental characteristic of raw materials is their potential; they are the building blocks from which finished products are created. Investing in raw materials can often lead to benefits such as bulk purchasing discounts, but they also tie up significant capital until production converts them into sellable goods.
- Work-in-Progress (WIP): WIP includes items that are in various stages of production but are not yet completed. This type is crucial for businesses that operate in manufacturing or refining sectors. Its key feature is the ongoing transformation from raw materials to finished goods. The main advantage of closely monitoring WIP is maintaining workflow efficiency; however, too much WIP can signify bottlenecks and lead to increased holding costs.
- Finished Goods: These are products that have been completed and are ready for sale. The standout feature of finished goods is their readiness to generate revenue. Managing finished goods inventory effectively can result in quicker sales cycles, contributing to healthier cash flow. On the flip side, holding too much finished goods can lead to excess inventory that might have to be discounted or even written off if not sold timely.
Inventory Control Objectives
The objectives of inventory control are aligned with enhancing the overall business strategy. There are several key goals that inform these objectives.
- Accuracy: Aiming for high accuracy in inventory records is vital. Accurate data allows businesses to make informed decisions regarding purchases and supply chain management. The main characteristic of accuracy in inventory control is the alignment between physical counts of goods and the recorded quantities. Achieving this requires vigilant checks and balances, such as regular audits and reconciliations. If accuracy slips, it can cause chaos in supply management, leading to stockouts or overstocking.
- Efficiency: Efficiency in inventory management streamlines operations and reduces unnecessary time and effort. The key characteristic of efficiency is the capability to meet demand without overstretching resources. Efficient systems leverage technology to provide real-time updates on stock levels, thereby optimizing the supply chain. Although it requires an upfront investment in technology and training, the long-term benefits include improved turnaround times and reduced waste.
- Cost-Effectiveness: Maintaining a cost-effective inventory system enables a firm to keep expenses in check while maximizing revenues. The unique feature here is balancing costs associated with storage, insurance, and potential obsolescence against sales revenue. Flawless inventory control minimizes excess and reduces waste, ultimately contributing to overall profitability. However, a focus solely on cutting costs can lead to inadequate stock levels, which might hinder sales opportunities.
Inventory Valuation Methods
First-In, First-Out (FIFO)
The FIFO method assumes that the first items purchased are the first to sell. This approach is particularly useful during times of rising prices, as it leads to lower cost of goods sold and higher profits. By valuing ending inventory at the latest prices, the balance sheet appears stronger.
Some advantages of FIFO include:
- Higher profitability in inflationary periods: Since older, cheaper inventory is counted as sold, profits appear inflated compared to LIFO.
- Simplicity: The concept is straightforward and often easier to implement for many businesses.
- Alignment with physical flow: FIFO typically mirrors the physical flow of goods in many industries.
However, FIFO can also lead to higher tax liabilities when profits increase due to higher reported earnings.
Last-In, First-Out (LIFO)
In contrast to FIFO, LIFO suggests that the most recently acquired inventory is sold first. This method can lead to lower taxable income during inflationary periods since the cost of goods sold will reflect the more expensive, newer purchases.
Some pros of LIFO are:
- Tax advantages: When prices rise, LIFO helps reduce tax obligations by decreasing taxable income.
- Improved cash flow: Lower taxes mean more cash available for reinvestment.
- Matching costs: It better matches current costs against current revenues, giving a clearer picture of profitability.
Yet, LIFO is not without its downsides, as it can result in outdated inventory valuations on the balance sheet, leading to inflated asset values over time. Additionally, it's not permitted under International Financial Reporting Standards (IFRS).
Weighted Average Cost
The weighted average cost method calculates inventory value based on the average cost of all items available for sale during the period. This method smooths out price fluctuations over time, creating consistent income statements.
Some highlights of using weighted average cost include:

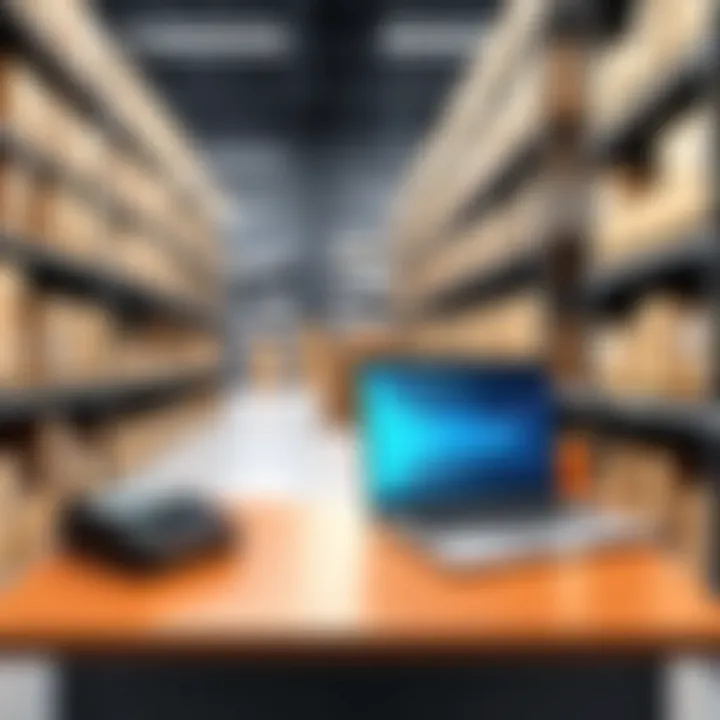
- Mitigates extreme value fluctuations: This method can neutralize the volatility of both FIFO and LIFO.
- Easier record-keeping: With fewer calculations needed to determine the cost of goods sold, the process becomes less labor-intensive.
- Stable profit margins: The averaging effect can help maintain consistent profit margins, making financial forecasting more reliable.
However, it may not be suitable for businesses that require precise tracking of inventory costs and prices, especially if the cost of goods fluctuates significantly.
Specific Identification
Specific identification is a method where specific costs are directly assigned to individual items in inventory. This method is common in industries where items are unique, such as real estate or high-end auto sales.
Notable features of specific identification include:
- Accuracy in cost tracking: Each item’s actual cost is precisely recorded, allowing for accurate financial statements.
- Direct matching of revenue and costs: It matches the actual cost of sold items directly with revenues from the sale, providing clarity on profit levels.
- Useful for high-value items: Particularly beneficial for businesses dealing in diversified products, where each has a significantly different value.
Despite its benefits, specific identification can be labor-intensive and may not be feasible for businesses with large volumes of identical items.
In summary, understanding inventory valuation methods is essential for effective inventory management and optimal financial reporting. Each method brings its own set of advantages and challenges that can affect the overall financial health of a business.
Impact of Inventory Control on Financial Statements
Understanding how inventory control affects financial statements is crucial for companies aiming to portray an accurate picture of their economic health. The interplay between inventory management and accounting practices can significantly shape a business's financial outcomes. Well-managed inventories can enhance profitability, while poor control may lead to inflated costs and potential losses. The precision in reporting inventory, thus, directly influences key financial metrics—making it a focal point in both accounting and operational strategy.
Balance Sheet Implications
The balance sheet presents a snapshot of a company's financial position at a given moment. Proper inventory control ensures that the inventory figures reflected are accurate, which is essential in providing a trustworthy overview of total assets. When inventory is overstated or understated, it distorts the balance sheet and can mislead stakeholders regarding the company's liquidity and financial stability.
Inventory valuation affects current assets directly. The method used, whether FIFO or LIFO, can either inflate or deflate inventory values, subsequently impacting the equity section as well. For instance, during inflationary periods, using FIFO usually results in higher asset values on the balance sheet than LIFO due to older, cheaper inventory being sold off first. Hence, firms must regularly compile inventory records to align their financial reporting against actual inventory levels, ensuring clear and concise balance sheet reports.
Income Statement Effects
Cost of Goods Sold
Cost of Goods Sold (COGS) is a pivotal measure that affects the gross profit calculation on the income statement. It represents the direct costs attributable to the production of the goods sold during a specific timeframe. The careful management of inventory directly influences COGS because it dictates which inventory gets sold first, depending on the valuation method in use.
A high COGS could indicate inefficient inventory management or a high sales volume but also means lower gross profit margins. Conversely, a lower COGS signifies better inventory turns and efficient stock management practices. A popular choice among accountants is to maintain detailed inventory records which help provide clarity on COGS and improve financial forecasting. The key characteristic here is that variances in COGS significantly affect profit margins: the more accurate the COGS, the clearer the view of profitability.
Some unique features of COGS include:
- It serves as a vital tool in identifying inventory-related issues, driving necessary operational changes.
- Accurate recording of COGS bolsters investor confidence, knowing the firm's efficiency and profitability metrics are reliable.
While calculating COGS, one must keep in mind its limitations. Changes in inventory valuation methods can sway reported profits and, thus, financial health perceptions.
Gross Profit Calculation
Gross profit is calculated as revenue minus COGS, revealing how efficiently a company produces and sells its goods. This figure is crucial for stakeholders since it shows the basic profitability of the company's sale activities. When inventory management is conducted effectively, gross profit can be maximized by reducing COGS through efficient stock control.
The essential characteristic of gross profit calculation is its capability to spotlight operational effectiveness. When a company knows its gross profits, it can better allocate resources towards growth and development. The unique feature here is that fluctuations in gross profit margins are indicative of inventory control success or failure and have a direct line to business strategies.
Some advantages of gross profit calculations include:
- It enhances strategic decision-making, guiding marketing, production, and financial choices based on profitable lines of products.
- By analyzing trends in gross profit margins, companies can comprehend demand fluctuations and adjust inventory levels proactively.
On the flip side, too much reliance on gross profit figures might lead to overlooking critical operational costs that might not be reflected in COGS. Therefore, while it’s an effective metric, it needs to be part of a wider analytical framework to ascertain overall health.
Role of Technology in Inventory Control
In the ever-evolving landscape of business, the role of technology in inventory control cannot be overstated. With the complexities surrounding stock management and financial reporting, leveraging advanced tech tools has become essential. Technology enhances accuracy, streamlines processes, and ultimately safeguards the bottom line. This section will delve into various technological components that significantly influence inventory control.
Inventory Management Systems
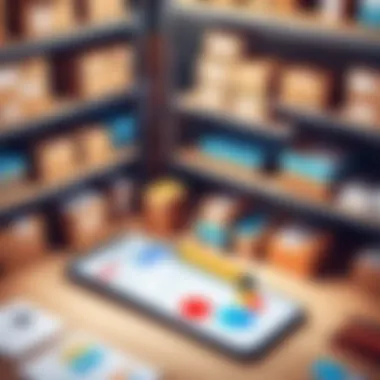

Software Solutions
Software solutions form the backbone of modern inventory management. They make managing stock more effective, allowing businesses to track their inventory in real-time. Notably, these systems offer integration with accounting software, creating a cohesive ecosystem that facilitates seamless data flow. A key characteristic of these solutions is their ability to provide detailed analytics. They allow businesses to identify trends, predict demand, and optimize stock levels accordingly.
However, these systems aren't without their challenges. They often require a steep learning curve, particularly for employees who may not be tech-savvy. Additionally, the cost of high-end software can be daunting for smaller enterprises. Yet, the advantages they provide—like accurate inventory counts and improved decision-making—often far outweigh these drawbacks.
Cloud-Based Systems
Cloud-based systems bring a fresh perspective to inventory management. They provide the flexibility of accessing inventory data from anywhere, making it easier for businesses with multiple locations or remote workers. The key characteristic of cloud solutions is scalability. Companies can adjust their storage and computing power as needed, catering to the erratic demands of inventory control.
A unique feature of cloud-based systems is their ability to offer automatic updates. Unlike traditional software that requires periodic manual updates, cloud systems ensure that users are always on the latest version, minimizing security risks and maximizing efficiency. The downside, however, may include concerns regarding data security and reliance on internet connectivity for access.
Automation in Inventory Management
Automation is transforming inventory management into a more precise and efficient practice. This progression is vital as it allows businesses to reduce human error and focus on strategic tasks instead. Automated systems can handle everything from stock level alerts to generating purchase orders, making operations smoother and more responsive to real-time data.
Implementing such automation does not only reduce workload but also improves operational speed. However, the upfront investment can be significant, and there’s a learning curve attached. Nonetheless, as businesses increasingly recognize the value of accuracy and speed, automation in inventory management emerges as a significant leverage point.
"Technology in inventory control is no longer a luxury; it’s a necessity for maintaining competitiveness in the market."
With the integration of these technologies, businesses can revolutionize their inventory control processes, resulting in a more efficient, streamlined, and intelligent approach to accounting. As we move towards the future, the interplay between inventory control technology and accounting becomes clearer, making this an indispensable area of focus for any organization.
Best Practices for Inventory Accounting
Effective inventory accounting can significantly influence a company's financial health. Proper management ensures that assets are recorded accurately, reducing discrepancies and improving overall operational efficiency. By adhering to best practices, businesses can minimize waste, avoid stockouts, and enhance their profitability. The integration of accounting standards with inventory management is not merely a task but a strategic move that directly affects various aspects of operations.
Regular Audits and Reconciliation
Conducting regular audits and reconciliation of inventory records is essential. This practice helps in identifying discrepancies between the physical count of inventory and recorded amounts. An audit can shed light on any potential theft, loss, or mismanagement issues lurking in the shadows. Moreover, reconciliation allows firms to correct errors in their accounting entries. In turn, this fosters accuracy in financial statements, which is vital for investors and stakeholders.
- Types of Audits
- Physical Inventory Counts: Scheduled counts to verify stock levels.
- Cycle Counts: Frequent checks of selected inventory items throughout the year.
- Spot Checks: On-the-spot assessments of inventory items as needed.
Each approach has its pros and cons, but the ultimate aim remains the same – to maintain an accurate inventory record.
Use of Inventory KPIs
Monitoring key performance indicators (KPIs) allows companies to gain insight into their inventory management practices. These metrics can guide future decisions and serve as benchmarks for improvement. Two of the most prevalent KPIs in inventory management include Inventory Turnover Ratio and Days Sales of Inventory.
Inventory Turnover Ratio
The Inventory Turnover Ratio is a critical gauge of how efficiently a company turns its inventory into sales. This metric indicates how many times inventory is sold or used over a specified period. A high turnover ratio is often associated with effective inventory management and strong sales performance.
- Key characteristic: This ratio provides clarity on how quickly products move off the shelves.
- Why it’s beneficial: Keeping this metric high reduces carrying costs and minimizes the risk of obsolescence.
- Unique feature: It reflects consumer demand and indicates whether the right products are in stock.
- Advantages/Disadvantages: While a higher ratio suggests good sales performance, an excessively high ratio may indicate insufficient inventory, leading to lost sales from stockouts.
Days Sales of Inventory
Days Sales of Inventory (DSI) measures how many days it takes for a company to sell its entire inventory. This metric is vital for understanding how inventory levels influence cash flow and operational efficiency.
- Key characteristic: DSI provides insight into how effectively inventory is managed against sales.
- Why it’s beneficial: A low DSI is desirable as it indicates faster sales, but too low may lead to stockouts.
- Unique feature: It allows firms to gauge how quickly they are selling their goods, impacting purchasing decisions.
- Advantages/Disadvantages: While a high DSI can point to slow sales, a carefully managed DSI can ensure optimal inventory levels aligned with market demand.
Collaboration with Suppliers
Strong relationships with suppliers cannot be overstated in inventory management. Collaboration can lead to better forecast accuracy and smoother supply chain operations. By working closely with suppliers, companies can ensure timely deliveries, negotiate favorable terms, and gain insights into supply chain challenges and opportunities.
- Benefits of Collaboration:
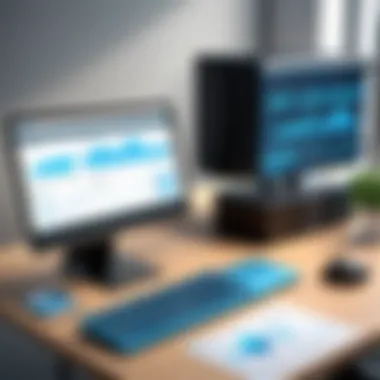
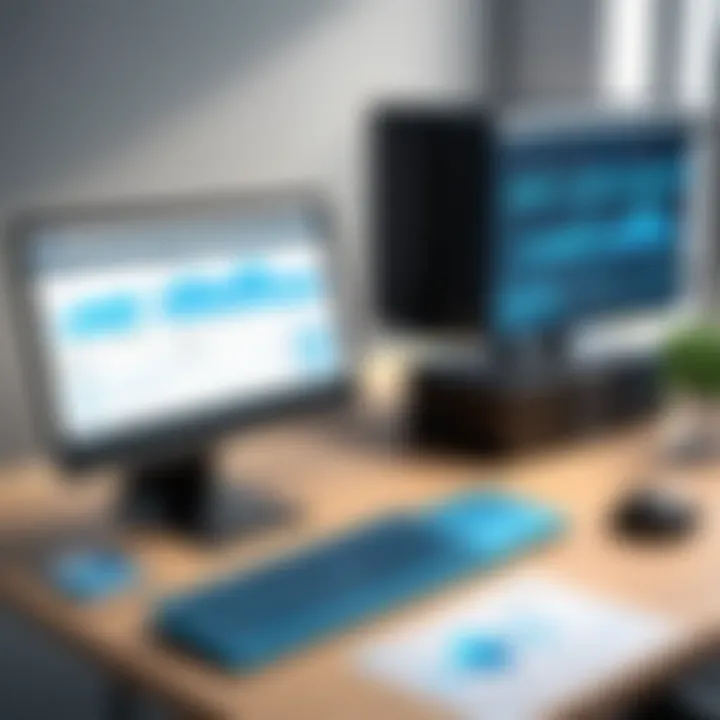
- Improved communication streamlines the ordering process.
- Joint forecasting can minimize excess inventory or shortages.
- Development of trust-based relationships encourages innovation.
When businesses foster a collaborative environment with their suppliers, they not only streamline their operations but also enhance their capacity to respond to market changes. This proactive approach is fundamental in sustaining a competitive edge in the market.
Challenges in Inventory Control
Inventory control often feels like walking a tightrope. Balancing the fine line between providing enough stock to meet demand and not overloading on excess inventory is an ongoing task for businesses of all sizes. Tackling the challenges inherent in inventory management is crucial, as effective control can lead to cost savings, improved cash flow, and overall efficiency. In this section, we will explore the pressing issues: stockouts and overstocking, as well as the need for seamless integration with accounting systems.
Stockouts and Overstocking
Stockouts and overstocking are two sides of the same coin. When a business runs out of a product (stockout), customers walk away empty-handed, often seeking alternatives. This can cause significant loss of sales and damage to the brand's reputation. A compounding issue arises with overstocking; having too much inventory ties up cash, clutters storage space, and increases the risk of obsolescence.
To illustrate, consider a retail clothing store that misjudged seasonal demand. If winter wear is overstocked in April, the added costs of storing that inventory might eat into profits. Conversely, an unexpected rise in demand for a popular jacket could lead to swift stock depletion, disappointing eager customers.
Managing these extremes requires keen forecasting techniques.
- Demand forecasting methods can include historical sales data analysis, seasonality considerations, and even market trends.
- Safety stock is another solution, acting as a buffer to ensure that stockouts remain rare.
"Success in inventory control is not merely having goods but ensuring the right amount is available at the right time."
Using Inventory Management Systems, businesses can gain real-time insights, minimizing errors and improving decision-making. These systems offer analytics that can highlight patterns in customer purchases, leading to better resource allocation.
Integration with Accounting Systems
The link between inventory control and accounting systems is another crucial area that requires attention. A disjointed approach can result in significant discrepancies and inefficiencies. If inventory quantities are not accurately reflected in the accounting records, reports may show inflated profits or losses. This can mislead management and affect strategic decisions.
Integrating inventory systems with accounting allows for:
- Real-Time Data Accuracy: Synchronizing inventory counts with financial records ensures that all stakeholders have a clear picture of what is available, what has been sold, and what remains.
- Streamlined Processes: Manual reconciliation between different systems consumes time and resources, creating potential for human error.
- Informed Decision-Making: Accurate data leads to better forecasting, aiding in the selection of appropriate inventory levels and reducing the oscillation between stockouts and excess products.
A common challenge businesses face is selecting the right system. Firms must look for solutions that cater to their specific requirements, such as those that can handle multi-location inventory management or provide robust reporting capabilities. Evaluating potential systems for compatibility with existing accounting frameworks is essential for optimizing efficiency.
In summary, the hurdles associated with inventory control can significantly impact a company's financial health and reputation. By understanding the dynamics of stockouts and overstocking, as well as ensuring seamless integration with accounting, businesses can put themselves in a position to face the market with confidence.
Future Trends in Inventory Control
In the realm of accounting, the future of inventory control is becoming increasingly pertinent as businesses strive for more efficient and adaptable methodologies. With the landscape of global commerce rapidly evolving, particularly due to technological advancements and changing consumer behaviors, understanding these trends is critical. Companies today must adopt flexible strategies to keep pace with market demands while ensuring cost-effectiveness and accuracy in their accounting practices.
The significance of these trends lies not only in streamlining operations but also in enhancing decision-making processes. Embracing future trends means navigating complexities in inventory management with a forward-thinking mindset. This section dives into two pivotal areas reshaping the inventory control landscape: the impact of artificial intelligence and adaptations to the burgeoning e-commerce market.
Impact of Artificial Intelligence
Artificial intelligence (AI) is not just a buzzword; it’s actively transforming how companies manage their inventory. Advanced AI algorithms can analyze vast amounts of data quickly, providing insights that were previously unattainable. For instance, AI can predict demand patterns based on historical data, seasonality, and even current market trends, leading to more informed purchasing decisions.
The benefits of integrating AI into inventory control are manifold:
- Predictive Analytics: By leveraging AI to forecast demand, companies can minimize stockouts and overstock situations. This leads to better cash flow and lower holding costs.
- Automation: AI facilitates automation at various stages of the inventory process. From reordering supplies to tracking stock levels in real-time, this reduces human error and saves time.
- Enhanced Efficiency: AI-driven systems learn and adapt over time, refining their recommendations and improving operational efficiency continuously.
As organizations adopt AI technologies, the dynamics of inventory management are set to shift dramatically. However, while embracing this trend, companies should tread carefully and consider the financial implications, including potential upfront costs and the integration challenges associated with such systems.
Adaptations to E-Commerce Growth
The exponential growth of e-commerce has had a profound influence on inventory management practices. More and more consumers are turning to online platforms for their purchasing needs. This shift necessitates a reevaluation of traditional inventory systems to meet higher expectations for speed and accuracy.
Businesses must consider several key adaptations in response to this trend:
- Real-Time Inventory Tracking: The ability to access live inventory data is crucial for e-commerce success. Companies are investing in cloud-based inventory management systems that allow for real-time updates across all sales channels, ensuring customers have accurate information about product availability.
- Flexible Fulfillment Strategies: With consumers expecting faster delivery times, businesses are rethinking their fulfillment approaches. This may include setting up fulfillment centers closer to populated areas or utilizing drop-shipping methods to streamline operations and reduce transit times.
- Integrating Inventory with Sales Platforms: Synchronizing inventory management systems with e-commerce platforms enhances visibility and reduces the chances of discrepancies that can lead to customer dissatisfaction.
Adapting to e-commerce growth isn't just about implementing new technologies—it's about rethinking existing processes to provide exceptional service. As online shopping continues to flourish, companies that swiftly adjust their inventory control mechanisms will not only survive but thrive.
In summation, harnessing trends such as AI and e-commerce adaptations is essential for modern inventory control. Businesses equipped to navigate these changes will gain a significant competitive edge in the marketplace.
As the landscape of inventory management continues to evolve, the need for innovative solutions becomes not just an option, but a necessity in achieving operational efficiency and fulfilling customer demands.