A Comprehensive Guide to Stress Analysis Software
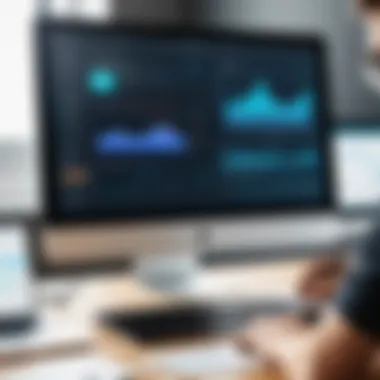
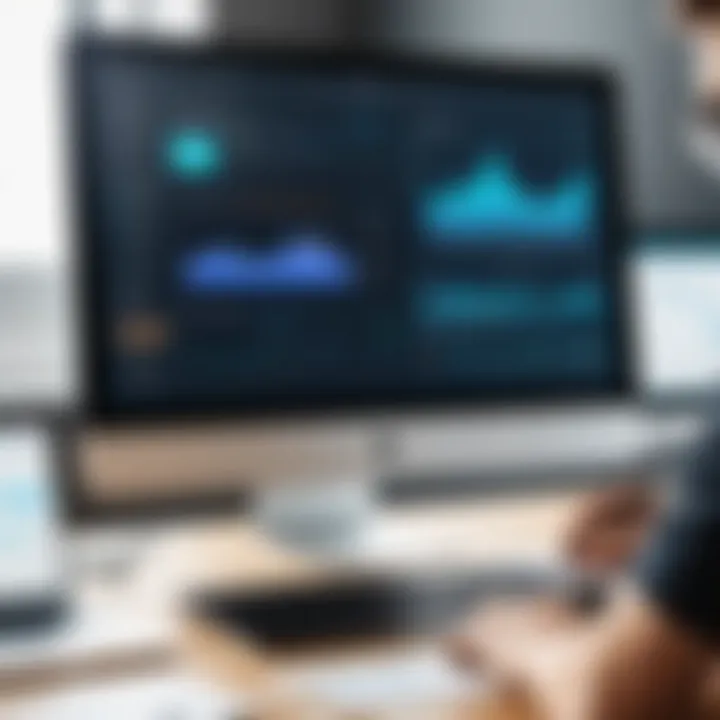
Intro
Stress analysis software plays a vital role in engineering design and assessment. It helps predict how structures respond to external forces, such as loads, temperatures, and other environmental conditions. The ability to accurately understand stress can prevent failures and ensure the safety and durability of various applications. As technology advances, this software continues to evolve, integrating new methodologies and improving functionality.
Understanding the complexities of stress analysis software is essential for IT professionals and business leaders who are selecting the right tools for their projects. This article explores important factors like software methodologies, key features, user experiences, and market trends. By analyzing these components, one can gain insight into what to look for in efficient stress analysis solutions.
Software Overview
Software category and its purpose
Stress analysis software is categorized mainly under simulation and analysis tools. Its core purpose is to numerically examine the behavior of materials and structures under various conditions. Often used in structural engineering, aerospace, automotive, and manufacturing sectors, these tools assist in optimizing designs and ensuring compliance with safety standards.
Key features and functionalities
Essential features of stress analysis software include:
- Finite Element Analysis (FEA): This is a key technique that divides complex structures into smaller, manageable zones to analyze stress distribution.
- Static and Dynamic Analysis: This distinguishes responses to static loads versus time-dependent forces, which is crucial for real-world applications.
- Visualization Tools: These features help users gain insights by providing visual representations of stress concentrations and deformation.
- Material Property Libraries: Access to predefined materials and their properties facilitates accurate simulations.
Some leading software options like ANSYS, Abaqus, and SolidWorks offer a variety of these functionalities. Their ability to integrate with other engineering tools enhances their utility in multi-disciplinary projects.
"Choosing the right stress analysis software can significantly impact the outcome and efficiency of engineering projects."
Understanding these key features helps organizations select the most suitable software that aligns with their specific needs.
Comparative Analysis
Comparison with similar software products
Different stress analysis tools offer unique advantages. For example, ANSYS is known for its comprehensive and powerful simulation capabilities, while SolidWorks is favored for its user-friendly interface, making it accessible for teams that may struggle with technical complexity. On the other hand, Abaqus excels in nonlinear simulations, which are critical for advanced material behavior modeling.
Market positioning and user demographics
The market for stress analysis software is competitive. Some tools cater to large engineering firms, while others focus on small to mid-size enterprises. Users range from engineers and technicians to project managers who need reliable data to make informed decisions. Analytics on user demographics also indicate that worldwide adoption is increasing among educators and students, highlighting the growing need for understanding these tools in early engineering education.
As a result, selecting software involves not only evaluating features but also understanding market positioning and user needs. This complexity ensures that organizations must stay informed about industry trends and emerging technologies to maintain a competitive edge.
Prelude to Stress Analysis Software
Understanding stress analysis software is critical for any engineering or design professional today. These tools serve to analyze materials, structures, or components under various loading conditions. Their importance cannot be overstated, as they facilitate design validation, optimization, and assurance of safety standards in engineering projects. Having precise knowledge about how these tools function enables engineers to predict failure modes, assess risks, and ultimately, make informed decisions regarding material choices and design methodologies.
Definition and Purpose
Stress analysis software is designed to simulate how physical components withstand applied forces and moments. It assesses stress distribution, deformation, and overall performance of materials under specific conditions. Engineers use this software to predict potential weaknesses and understand behavior under load. The ultimate aim is to ensure that structures and components are safe, reliable, and cost-effective.
Typical applications include evaluating structural integrity in buildings, predicting component lifespan in machinery, and optimizing performance in automotive design. This software enhances efficiency in development processes, allowing teams to reduce the number of physical prototypes needed for testing.
Historical Context and Evolution
Initially, stress analysis relied heavily on manual calculations and simplified hand-drawn models, which often led to inaccuracies. As technology progressed, the introduction of computer-aided design (CAD) allowed for more detailed geometric rendering. However, the real turning point came with the implementation of finite element analysis (FEA) during the 1970s and 1980s. FEA provided a numerical approach to solving complex problems, breaking down objects into smaller, manageable finite elements.
Over the past few decades, stress analysis software has evolved significantly. Current programs integrate advanced computational algorithms, enabling real-time simulation and evaluation of stress distribution. Moreover, the incorporation of user-friendly interfaces and tools for data visualization has made these complex analyses accessible to a broader range of professionals. The shift towards cloud computing and real-time collaboration is further transforming how teams conduct stress analysis, allowing for increased efficiency and innovation in engineering design.
Significance in Engineering and Design
The role of stress analysis software in engineering and design is paramount. It provides tools that help engineers examine materials and structures under various loads and conditions. Understanding the stress within a structure is critical for ensuring safety and durability. With precise analysis, engineers can predict potential failure points, enhancing both the design process and the final output.
Role in Structural Engineering
In structural engineering, stress analysis software is essential. It aids in evaluating how different forces affect structural integrity. Engineers use this software to determine how buildings and bridges will behave under loads, such as wind pressure or seismic activity. By simulating these conditions, engineers can design structures that withstand these pressures, which is vital for public safety.
- Safety Assurance: The primary goal is to prevent catastrophic failures, which can arise from inadequate structural designs.
- Material Selection: Engineers can analyze which materials are most suitable for specific conditions, leading to cost-effective designs.
- Optimization: By using stress analysis software, engineers can improve the weight-to-strength ratio of structures, utilizing materials more efficiently.
Applications in Mechanical Engineering
Mechanical engineering also greatly benefits from stress analysis software. It enables engineers to optimize the performance of components and machinery under different operational scenarios. The software helps determine how mechanical parts respond to loads, vibrations, and thermal changes. This is particularly important for designing machines that are efficient and durable.
- Design Validation: Engineers can validate designs before physical prototypes are made, saving time and resources.
- Failure Analysis: The software identifies points of failure, helping engineers redesign components to enhance reliability.
- Performance Improvement: It assists in making incremental improvements to existing designs based on precise data.
Their significance in engineering extends beyond safety; it encompasses cost savings, increased productivity, and innovation in design. As technology advances, the integration of cause-and-effect relationships into the software will only enhance its value in both structural and mechanical applications. This makes stress analysis software an indispensable tool for engineers.
Types of Stress Analysis Software
Understanding the various types of stress analysis software is crucial for engineers and designers. Each type serves distinct purposes, tailored to specific needs in engineering disciplines. This section examines the principal categories of software utilized in stress analysis: Finite Element Analysis (FEA), Computational Fluid Dynamics (CFD), and Multibody Dynamics (MBD). Each type carries unique benefits and considerations that influence their use in practical applications.
Finite Element Analysis (FEA)
Finite Element Analysis (FEA) is one of the most widely used tools in structural engineering. FEA allows analysts to break down complex geometries into smaller, manageable elements. This approach facilitates simulations of physical phenomena, such as stress, strain, and deformation, under various loading conditions. It is particularly effective in assessing how materials and structures respond to external forces.
One primary benefit of FEA is its capability to provide detailed insights. Engineers can visualize stress distribution across a structure, identifying hotspots or areas prone to failure. Additionally, FEA models can adapt to linear and non-linear material behaviors, enriching the analysis.
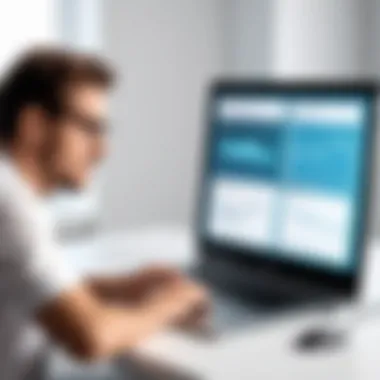
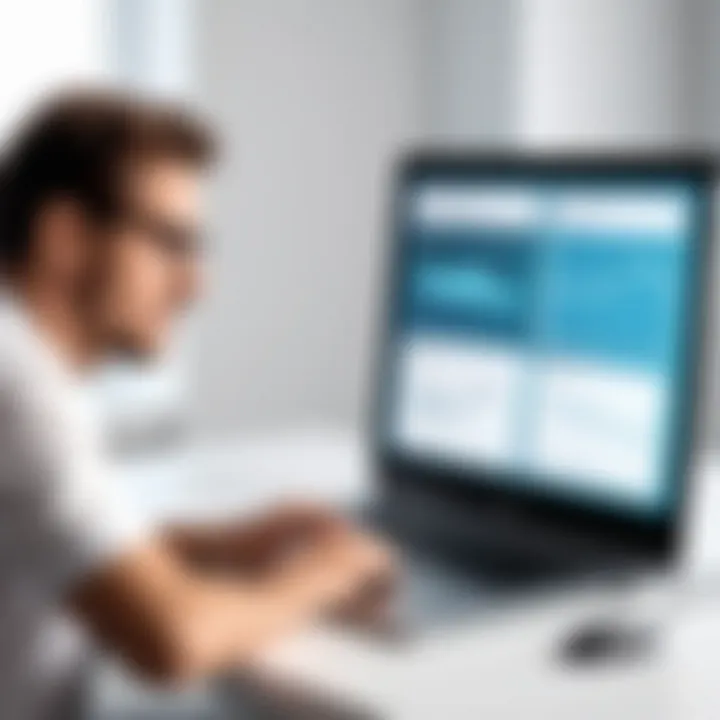
However, while FEA is powerful, it also demands a good understanding of the principles of mechanics and material behavior. Furthermore, the accuracy of FEA results heavily depends on the quality of the input data and boundary conditions defined by the user. Thus, continued training and education are essential for practitioners to leverage FEA effectively.
Computational Fluid Dynamics (CFD)
Computational Fluid Dynamics (CFD) software specializes in analyzing fluid interactions with solid boundaries. CFD plays a critical role in fields like aerospace, automotive, and civil engineering. It enables engineers to predict fluid behavior around various shapes, offering insights into phenomena like drag, lift, and turbulence.
CFD models allow for real-time simulations of airflow, fluid flow, heat transfer, and chemical reactions. These simulations help identify potential issues early in the design process, significantly reducing costs associated with physical prototyping and testing. For example, engineers can predict how a vehicle will perform aerodynamically before producing the actual model.
Despite its advantages, CFD has challenges. The computational resources required can be substantial, especially for complex simulations. Moreover, users must have a requisite knowledge of fluid dynamics principles to set up accurate simulations. Without this expertise, the results might lead to incorrect conclusions.
Multibody Dynamics (MBD)
Multibody Dynamics (MBD) software focuses on the behavior of interconnected rigid or flexible bodies. It is paramount in applications where the interaction of multiple components affects overall performance. For instance, MBD is widely used in automotive design, robotics, and biomechanical simulations.
The software simulates how parts move relative to one another, capturing the dynamics resulting from forces such as gravity and contact forces. This capability is crucial for performing an accurate analysis of system responses under various loading conditions.
An important advantage of MBD is its ability to help engineers optimize mechanisms early in the design process. By previewing how components will interact, they can make informed adjustments to project designs. Nevertheless, MBD also requires a firm grasp on mechanical principles and system dynamics, posing a barrier for some users.
Key Features of Stress Analysis Software
The significance of selecting the right stress analysis software cannot be overemphasized. The features incorporated in these systems often determine their functionality, effectiveness, and the overall user experience. In this section, we will break down the key features of stress analysis software, shedding light on user interface and usability, integration with other tools, and customization and flexibility. Understanding these elements helps ensure that the software chosen meets specific project requirements and user needs.
User Interface and Usability
A user-friendly interface is paramount for effective stress analysis software. Engineers and designers generally prefer software that allows for smooth navigation and quick access to various tools. A well-designed user interface can significantly enhance productivity. It should present a clear layout with logical workflow that minimizes the learning curve for new users.
Often, intuitive design features such as drag-and-drop capabilities, tooltips, and customizable dashboards contribute to better usability. For instance, software like ANSYS and SolidWorks are known for their straightforward interfaces, which help in rapidly conducting simulations and visualizing results.
The usability aspect also involves the software's ability to provide feedback. It should be capable of presenting immediate visual insights through graphs and charts. This enables users to identify issues in designs or simulations early in the process. Overall, the combination of a clean user interface and strong usability aspects is essential in choosing software for stress analysis purposes.
Integration with Other Tools
Another crucial feature in stress analysis software is its ability to integrate seamlessly with other engineering and design tools. Effective integration enhances workflow efficiency across various stages of projects, which is especially important in multidisciplinary teams. Popular software solutions often come with compatibility for tools like AutoCAD, Catia, or MATLAB.
Integration allows for data sharing between tools without the need for redundant manual inputs. For example, if a design is altered in CAD software, the changes can be reflected in the stress analysis software automatically if both tools are well-integrated. This integration not only saves time but also reduces errors that can occur during manual data entry. With features like API support, users can even develop custom integration solutions to meet their unique requirements.
Customization and Flexibility
Customization options in stress analysis software cater to specific project demands and individual preferences. Being able to modify the software to align with a team's workflow can significantly enhance its effectiveness. Many leading solutions offer flexible features that allow users to create custom reports, adjust simulations parameters, or tailor user profiles.
Flexibility also extends to the software’s capability to handle a variety of analysis types, such as static, dynamic, linear, and non-linear analyses. For instance, software like Abaqus provides users with such flexibility, allowing them to adapt tools according to the needs of different engineering projects.
In summary, the key features of stress analysis software—user interface and usability, integration with other tools, and customization and flexibility—are vital components that can influence the effectiveness and user satisfaction. By understanding these features, professionals can make more informed choices when selecting the software that best suits their technical and operational requirements.
Methodologies in Stress Analysis
The field of stress analysis is crucial for ensuring the safety and integrity of structures and mechanical systems. Various methodologies play a central role in this domain. Understanding these methodologies equips professionals with the tools needed to effectively assess stress distributions, make informed design choices, and predict potential failures. Incorporating different methodologies enables robust and reliable analysis tailored to specific engineering challenges.
Static and Dynamic Analysis
Static analysis examines how structures respond to loads that do not change over time. This approach is particularly useful for evaluating the strength of a component under constant conditions. For instance, engineers might use static analysis to determine the stress on a bridge under the weight of vehicles.
Dynamic analysis, on the other hand, addresses loading conditions that vary with time. This includes seismic events, vibrations from machinery, or aerodynamic forces affecting an object in motion. A dynamic analysis is vital for systems subject to fluctuating loads since it helps predict how the stress state evolves during such fluctuations.
The importance of both approaches cannot be understated. A thorough understanding of static and dynamic behaviors leads to safer and more resilient designs, potentially avoiding catastrophic failures. Here are some considerations:
- Static Analysis:
- Dynamic Analysis:
- Assumed loads are steady and consistent.
- Easier to compute due to simpler equations.
- Typically used in preliminary design phases.
- Requires sophisticated models to account for time-dependent phenomena.
- Higher computational demand.
- Essential for safety-critical applications, such as aerospace and automotive industries.
Linear vs Non-linear Analysis
Linear analysis assumes that material properties and responses remain constant under varying loads. It's often more straightforward but may not always provide accurate predictions, particularly for materials or structures that experience significant deformations. When considering materials like rubber or metal alloys subjected to high loads, linear assumptions might lead to unsafe design.
Non-linear analysis, however, accounts for changes in material properties and geometrical factors as stress increases. This methodology is critical for real-world applications where structures experience complex stress states, such as buckling or yielding.
Moreover, non-linear analysis is necessary when working with complex geometries or large displacements. As a result, this method provides a more realistic assessment of a system’s performance.
Key points to remember include:
- Linear Analysis:
- Non-linear Analysis:
- Easier to implement.
- May yield adequate results for simple structures.
- Limits applications in severe load cases.
- Complex and often requires advanced computational resources.
- More accurate in predicting failures or unusual behaviors.
- Necessary for detailed evaluations in high-stakes engineering tasks.
Understanding these methodologies allows professionals to select the appropriate approach based on project requirements, ensuring both efficiency and safety.
Choosing the Right Stress Analysis Software
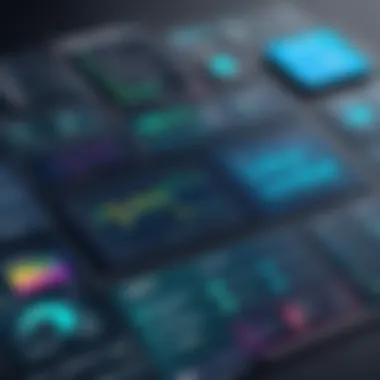
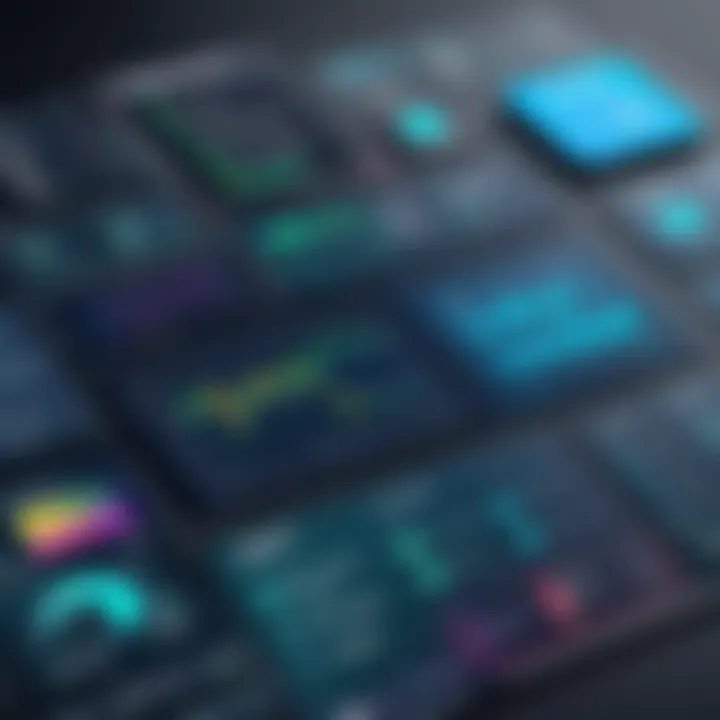
Selecting appropriate stress analysis software is critical. The right tool can streamline processes, enhance design accuracy, and affect project outcomes significantly. This section dives into identifying project requirements, evaluating user needs and skill levels, and considering budget implications. It highlights how these facets intertwine, ultimately guiding the decision-making process for engineering professionals.
Identifying Project Requirements
Understanding project requirements is the first step in choosing stress analysis software. Different projects demand unique functionalities. For example, a structural analysis of a bridge will have distinct needs compared to a fluid dynamics assessment in aerospace engineering. Here, specifications like the size of the project, complexity, and type of materials involved play essential roles.
To start, define the objectives clearly. Are you looking for detailed simulations, or do you need quick evaluations? Tools such as ANSYS or SolidWorks have diverse capabilities tailored for various engineering tasks, from dynamical evaluations to thermal performance studies. Such analysis helps in narrowing down options, ensuring the selected software aligns with the project scope.
Key Considerations:
- Type of analysis required: static, dynamic, thermal, etc.
- Material properties and behaviors to simulate.
- Project scale: Small prototype versus large infrastructure.
Evaluating User Needs and Skill Levels
User proficiency is another critical aspect. Both novice users and experienced professionals have unique requirements. A complex interface may deter beginners while offering advanced features for experienced engineers. Evaluate the existing skill levels of your team. Some software, like COMSOL Multiphysics, may have a steep learning curve but offers robust capabilities for users with a proper background.
Consider providing training sessions for teams who need enhancement in their skills. This investment can improve efficiency and exempt organizations from the risks associated with improper software usage. Also, evaluate features that allow customization; these might suit different user capabilities.
Important Points:
- Assess experience with previous software tools.
- Ensure technical support is available.
- Identify the necessity of training programs.
Budget Considerations
Budgeting is often a decisive factor when selecting stress analysis software. Prices vary widely across platforms. High-end solutions like Abaqus may deliver comprehensive features but require significant financial investments. Alternately, tools such as Fusion 360 provide essential features at a lower cost.
Moreover, factor in potential additional costs. Licensing fees could become a recurring expense. Subscription models might have lower upfront costs but accumulate over time. Look for options that offer trial periods. This can help gauge effectiveness without a financial commitment.
Financial Considerations:
- Upfront costs: purchasing or leasing options.
- Ongoing costs: licenses, maintenance, updates.
- Hidden costs: training or support services.
Choosing the right stress analysis software is about analyzing all these factors. It’s not just a tool; it’s a comprehensive solution that should serve both present and future needs.
Market Overview of Stress Analysis Software
The landscape of stress analysis software is vast and evolving. Understanding this market is crucial for professionals in engineering and design. With advancements in technology, the complexity and functionality of these tools have increased significantly. This section will explore leading software solutions and notable emerging technologies in the field.
Leading Software Solutions
The stress analysis software market features a range of established solutions widely adopted by various industries. Among the most recognized names are Autodesk Simulation, ANSYS Mechanical, and Siemens NX. Each of these tools offers distinctive capabilities:
- Autodesk Simulation: This software provides a user-friendly interface and integrates well with other Autodesk products. Its ability to perform various types of simulations makes it a popular choice among engineers.
- ANSYS Mechanical: Known for its robustness and extensive capabilities, ANSYS Mechanical is ideal for finite element analysis. It supports complex simulations, thus facilitating accurate results in structural and thermal analyses.
- Siemens NX: A comprehensive product design and engineering software, Siemens NX features advanced simulation tools. It effectively supports multi-disciplinary designs, making it applicable in numerous engineering sectors.
Emerging Tools and Technologies
With the rapid pace of technological advancement, several new tools are making their mark in the stress analysis industry. Some of these tools focus on niche applications or leverage cutting-edge technologies like AI and machine learning. Examples include:
- Fusion 360: This cloud-based tool by Autodesk is gaining traction among small to medium enterprises. It combines CAD, CAM, and CAE capabilities, allowing for seamless transitions between design and analysis tasks.
- COMSOL Multiphysics: This software enables multiphysics simulation, addressing complex engineering problems involving multiple physical phenomena. Its versatility positions it well for research and industrial applications.
- SimScale: Operating entirely in the cloud, SimScale provides easy access to computational power. It allows users to perform stress analysis and thermal simulations without the need for local resources, promoting collaboration and efficiency.
As the industry evolves, staying informed about both leading and emerging tools is vital for making informed software selections.
User Experiences and Case Studies
User experiences and case studies play a vital role in understanding the practical implications of stress analysis software in real-world scenarios. They offer insights into how various industries leverage these tools to solve complex problems, improve designs, and ensure safety. Case studies illustrate successful applications, showcasing the tangible benefits that different sectors have achieved by using stress analysis software. This section will explore two key aspects: industry-specific applications and comparative user feedback.
Industry-Specific Applications
Different industries utilize stress analysis software in unique ways, addressing their specific challenges and requirements. For instance, in the aerospace sector, engineers rely heavily on software like ANSYS for simulating aerodynamic properties and optimizing structural components of aircraft. Stress analysis helps predict failure points under various loads, ensuring safety and performance.
Alternatively, the automotive industry uses SOLIDWORKS Simulation to analyze crashworthiness of vehicles. By assessing materials and design under stress, engineers can significantly enhance safety features and reduce weight, all while maintaining performance.
Construction and civil engineering also benefit from these tools. Design firms often use Autodesk Robot Structural Analysis to evaluate loads on structures such as bridges and high-rise buildings. Stress analysis software assists in confirming safety and compliance with legal standards, which is crucial in large-scale projects.
The versatility of stress analysis software across industries demonstrates its broad applicability and importance in engineering decisions.
Comparative User Feedback
When selecting stress analysis software, user feedback reveals key insights into functionality, user experience, and overall effectiveness. Professional reviews and discussions on platforms such as Reddit point out specific features that users value.
For example, many users appreciate the intuitive user interface of COMSOL Multiphysics, enabling quick navigation between different modules. This ease of use significantly reduces the learning curve, making it attractive for teams with varying levels of expertise. On the flip side, some feedback highlights that complex functionalities may require additional training, which is a consideration for project managers.
Furthermore, comparative studies often reveal preferences among engineers regarding computational efficiency. Users of ANSYS frequently commend its robust simulation capabilities, particularly in handling non-linear problems, suggesting that its advanced algorithms allow for accurate stress predictions in demanding environments. Conversely, some users may report slower processing times with alternative tools under certain conditions.
"Feedback from users shows that while multiple software solutions can achieve similar results, the choice often comes down to specific features that align with project needs."
In summary, the evaluation of user experiences, along with industry-specific case studies, provides a comprehensive understanding of stress analysis software in practice. This analysis goes beyond mere specifications, capturing the subtleties of how these tools are effectively employed in various engineering contexts.
Advanced Techniques in Stress Analysis
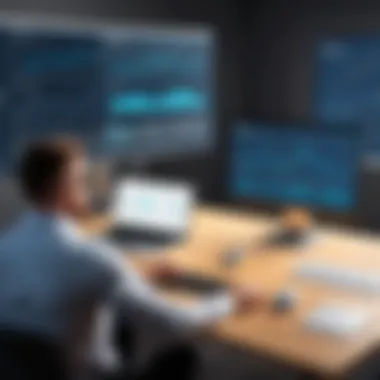
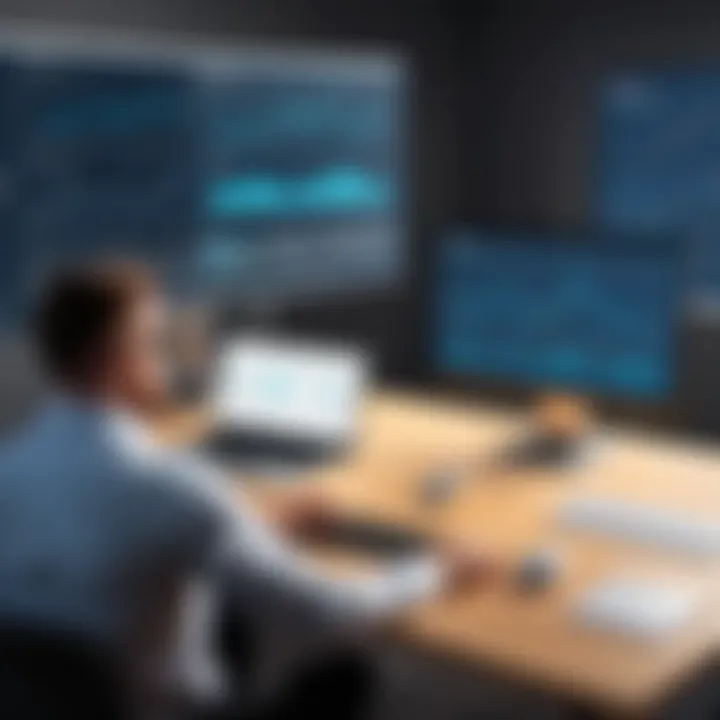
Advanced techniques in stress analysis have become crucial in meeting the growing demands of modern engineering projects. These methods enable engineers and designers to predict material behavior under various loading conditions with higher precision. The importance of this topic lies in its ability to improve safety, reduce project costs, and enhance overall design efficiency. As industries evolve, the need for more sophisticated tools becomes evident, paving the way for innovative methodologies that leverage real-time data and emerging technologies.
Toward Real-Time Analysis
Real-time analysis represents a major breakthrough in the field of stress analysis software. With the integration of live data feeds, engineers can monitor structural integrity and assess stress levels continuously. This technique reduces the time between data collection and analysis, allowing for rapid decision-making.
Some benefits of real-time analysis include:
- Immediate Feedback: Engineers receive instantaneous data on how structures perform under different conditions. This immediacy enhances the responsiveness of maintenance teams, potentially preventing failures before they occur.
- Dynamic Load Adjustments: With real-time analysis, the system can adapt to changing loads or environmental conditions. For instance, in civil engineering, structures such as bridges and skyscrapers can be monitored for wind-induced stress variations.
- Cost Efficiency: By addressing issues immediately, projects can save money related to repair costs or delays resulting from failures.
Artificial Intelligence in Stress Analysis
Artificial intelligence (AI) is making significant strides within stress analysis software, greatly enhancing its capabilities. Through machine learning algorithms and neural networks, AI can process vast amounts of data to provide actionable insights. This ensures that engineers have the most reliable information regarding material performance and structural resilience.
Key aspects of AI integration in stress analysis include:
- Predictive Analytics: AI can analyze historical data and forecast potential issues in design or material selection. This can save companies significant financial resources by avoiding mistakes early in the design process.
- Enhanced Accuracy: Machine learning models can improve the accuracy of stress predictions by learning from past analyses. These models fine-tune themselves as more data becomes available.
- Automation of Design Optimization: AI tools can automate complex calculations and adjustments in designs, thereby speeding up the analysis process while maintaining accuracy.
In summary, the incorporation of real-time analysis and AI into stress analysis software represents a significant advancement in the field. By leveraging these technologies, engineers can achieve unprecedented precision and efficiency in their projects, ultimately leading to safer and more reliable structures.
The potential for innovation in stress analysis is vast, making it a critical area of focus for engineers and software developers alike.
Challenges and Limitations
In the rapidly evolving field of engineering, stress analysis software plays a pivotal role. However, it is essential to address the challenges and limitations inherent in these tools. A nuanced understanding of these issues not only helps in better software selection but also informs users on how to maximize the benefits while mitigating potential drawbacks. This section will delve into two primary challenges: accuracy and reliability issues, as well as computational resource demands.
Accuracy and Reliability Issues
Accuracy is a cornerstone in the field of stress analysis. When engineers employ software tools, they rely on these systems to produce precise simulations of real-world conditions. However, several factors can hinder the accuracy of the results. For example, the underlying algorithms are crucial in determining the fidelity of the analysis. If the algorithms are not robust, the outputs may be misleading, leading to potential design flaws.
Common factors affecting accuracy include:
- User Input: If the data entered is incorrect or imprecise, the results will be similarly flawed. Users must have a thorough understanding of material properties and load conditions.
- Mesh Quality in FEA: In Finite Element Analysis, the quality of the mesh affects the accuracy of the simulations. Inadequate meshing can result in significant errors in stress distribution assessment.
- Software Limitations: Some software may not support complex shapes or loading conditions, thereby restricting the accuracy of the analysis.
If accuracy issues arise, it can lead to serious repercussions in engineering projects. These can range from over-engineering a solution to risking structural integrity. Hence, it is critical for users to routinely validate software results against experimental data where possible.
Computational Resource Demands
Computational resource demands represent another significant challenge with stress analysis software. As simulations increase in complexity—especially with multi-physics analyses— the resources required can soar. This is particularly concerning for small companies or individual practitioners that may not have access to high-performance computing infrastructure.
Several aspects to consider regarding computational resource demands include:
- Hardware Requirements: Advanced software solutions often necessitate powerful processors and substantial memory. Without adequate hardware, users may experience slow performance or the inability to run simulations.
- Time Constraints: Longer computation times can lead to project delays. Engineers must balance the need for detail in analyses against time limitations, optimizing models where possible.
- Licensing Costs: High-performance software often comes with high licensing fees, which can be a barrier for smaller entities seeking competitive edge through advanced analysis capabilities.
"Understanding the computational demands of stress analysis software is vital for efficient project planning and resource allocation."
Ultimately, addressing these challenges involves careful planning, investment in training, and equipment. As companies adopt more advanced tools, they must ensure the supporting infrastructure is in place to maximize performance and accuracy.
Future of Stress Analysis Software
In the realm of engineering and design, understanding the future of stress analysis software is paramount. This segment explores significant advancements and projections which will shape the way professionals conduct stress analysis. Emerging technologies and methodologies are enhancing analytical processes, making them more precise and accessible. The evolution of these software tools directly impacts various industries, providing better solutions to meet the demands of complex engineering projects. Future developments in stress analysis tools are poised to facilitate optimization, leaving behind traditional limitations.
Technological Trends
Numerous technological trends are redefining the landscape of stress analysis software. One key aspect is the integration of artificial intelligence and machine learning. These technologies can analyze vast datasets quickly and identify patterns that might not be visible through traditional means. As AI tools continue to evolve, they will not only enhance prediction accuracy but also automate several routine analytical tasks.
In addition, advancements in data visualization are becoming increasingly essential. Professionals now expect intuitive and interactive interfaces that allow them to interpret results effortlessly. This shift towards visual data representation leads to faster decision-making processes in critical engineering scenarios.
Moreover, the incorporation of virtual and augmented reality (VR/AR) offers immersive experiences. Engineers can visualize stress distributions in three-dimensional formats, making it easier to comprehend and address structural weaknesses.
The Role of Cloud Computing
Cloud computing is changing how stress analysis software is accessed and utilized. By shifting resources to the cloud, businesses can benefit from scalable and flexible solutions. This means users can access their tools anytime, anywhere, promoting collaboration among globally dispersed teams.
The collaborative aspect of cloud computing supports real-time data sharing. This feature allows several users to work on a project simultaneously, streamlining workflows. Additionally, cloud providers often introduce regular updates and enhancements, ensuring that users have the latest tools without the hassle of manual upgrades.
Security is another critical consideration. Many cloud services invest heavily in securing sensitive data, offering users peace of mind regarding the safety of their analyses. Ultimately, the role of cloud computing in stress analysis software not only optimizes resource allocation but also enhances the efficiency and security of engineering processes.
"Future trends in stress analysis software highlight a shift towards intelligent, collaborative, and cloud-based solutions that prioritize efficiency and modern needs."
End
The conclusion of this article serves as a vital summarization of the intricate world of stress analysis software. It reflects on the significant points discussed throughout the narrative and emphasizes the critical understanding of this software for professionals in engineering and design.
In today's engineering landscape, stress analysis software is more than a tool; it is a cornerstone of modern design and engineering practice. Its applications span across various disciplines, including structural and mechanical engineering. By understanding the methodologies intrinsic to these tools, such as finite element analysis and computational fluid dynamics, professionals can enhance their approaches to design and problem-solving.
Summary of Key Points
- Importance of Software: Stress analysis software helps identify potential issues before physical testing, reducing costs and time in the development phase.
- Methodologies: Various methodologies enable deeper insights. Static and dynamic analysis, along with linear and non-linear analysis approaches, allow for comprehensive evaluations.
- Market Landscape: Leading solutions like ANSYS and Autodesk Fusion 360 provide robust capabilities, while emerging technologies push boundaries in real-time analysis.
- Challenges: Despite the advancements, accuracy and resource demands remain critical issues for end-users. Being aware of these challenges allows for more informed decisions.
- Future Directions: The influence of artificial intelligence and cloud computing is reshaping the future of stress analysis software, promising improved accessibility and performance.
Final Thoughts on Software Selection
When selecting the right stress analysis software, it is important to consider several factors:
- Project Requirements: Understanding project specifications guides the selection of the software that can best meet these needs.
- User Needs: Evaluating the skills of the users is essential. A software that is too complex may hinder productivity, while one that is too simplistic may not meet the necessary demands.
- Budget Constraints: The cost of software can vary widely. Aligning features with budgetary limits ensures the best value without compromise on capability.
The process of selecting stress analysis software is not trivial. It requires careful consideration of both present and future needs. This decision can profoundly affect project outcomes and long-term operational efficiency. As technologies continue to evolve and revolutionize engineering methodologies, staying informed about potential software solutions remains crucial.